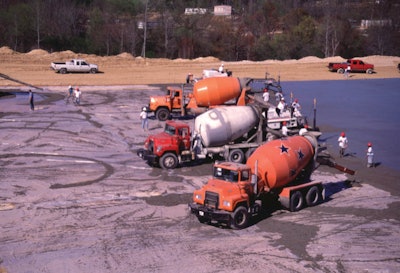
Some specifers limit the single-placement area of concrete slabs-on-ground to 2,000 to 5,000 square feet, but specifications sometimes place a very stringent single-placement limit of 900 square feet (a 30x30-foot panel). The major rationale for these limits is a belief that they reduce shrinkage cracking by allowing some shrinkage to occur before the next placement. There are no ACI documents, however, that support this reasoning. In fact, ACI 302 has stated since 1980 that this limited placement size concept has not achieved any better shrinkage results, is more expensive and adds time to the schedule. The ACI documents are discussed below.
ACI Concrete Craftsman Series: Slabs-on-Ground
ACI uses CCS-1(10) "Concrete Craftsman Series: Slabs-on-Ground" as the training manual for certifying flatwork finishers. This manual states that "Slab-on-ground placements can range from very small to more than 50,000 square feet in a single placement. Construction schedules and contractor economics typically dictate daily concrete placements of 10,000 to 20,000 square feet unless a laser-guided, wheel-mounted screed is used, in which case daily placements from 30,000 to 50,000 square feet are possible." The manual also lists "Factors to consider when determining appropriate placement size.” Reduction in shrinkage or shrinkage cracking is not listed as a factor to consider when determining appropriate placement size.
ACI 302 Guide for Concrete Floor and Slab Construction
ACI 302 stated its objection to placing small slabs as a way to minimize joint shrinkage in 1980. The same provisions and objection were stated again in 1989, 1996 and the 2004 editions. ACI 302 has maintained this objection to small placement sizes for over 30 years. And while specifiers often reference ACI 302 in the contract documents, they fail to use part of the document to develop the specifications. See the sidebar "Placing Sequence Recommendations" for the provisions in ACI 302.1R-04.
ACI 302 also includes 11 different recommendations as good practices that help to limit shrinkage cracking. Note that a placement size limitation is not on the list.
"Thus, drying shrinkage of concrete containing water reducers can still cause unsightly cracking, unless the following good practices are employed:
- Contraction joints not spaced too far apart;
- Contraction joints deep enough;
- Contraction joints sawn early enough;
- Slabs not strongly restrained at their perimeters by bond of floor or slab concrete to foundation walls or other construction, or by tying-in reinforcement to foundations, docks, and tilt-up walls;
- Isolation joints provided around columns;
- Joint or extra reinforcing steel placed diagonally to reentrant corners;
- Concrete mixtures of necessary strength with the proper amount of cement and water, also, mixtures that do not include any ingredient, such as aggregates or admixtures, with high-shrinkage characteristics;
- Proper curing;
- Slabs not restrained by a rutted or uneven base and changes in slab thickness;
- Discontinued reinforcement at joints, thus encouraging joints to open; and
- Slabs cast upon a base which has a low coefficient of friction, such as a fine- graded crushed stone. This will provide a smooth surface on which the slab can slide.
ACI 360R-10 Guide to Design of Slabs-on-Ground
ACI 360R-10 discusses the design of unreinforced concrete slabs and the desire to control shrinkage cracking. Note as shown below, and as highlighted with an underscore, shrinkage potential, not placement size, dictates the joint spacing.
"Controlling the effects of drying shrinkage is critical to the performance of unreinforced concrete slabs. Two principal objectives of unreinforced slab-on-ground design are to avoid the formation of random, out-of-joint cracks and to maintain adequate joint stability. The slab’s anticipated live loading governs its thickness and cross-joint shear transfer requirements, whereas shrinkage considerations dictate the maximum joint spacing."
Similar to ACI 302, ACI 360 also provides recommendations for reducing the effects of slab shrinkage and curling. Note that there is no recommendation to limit placement size.
"Appropriate design and specification provisions can reduce shrinkage cracking and curling. Such provisions should include:
- Relative shrinkage of various concrete mixtures;
- Type and location of reinforcement;
- Subgrade friction;
- Concrete planarity;
- Permeability;
- Slab thickness;
- Shrinkage restraints;
- Location of sawcut contraction joints; and
- Properly designed vapor retarder/barrier and aggregate blotter systems".
ACI 301-10 Specifications for Structural Concrete
ACI 301-10 "Specifications for Structural Concrete" added a new section on Industrial Floor Slabs. This section includes minimum default specification provisions for ground-supported industrial floor slabs. While provisions on concrete shrinkage, maximum joint spacing, and details on isolation, construction, and contraction joints are included, the specification does not limit the placement size. The specification only requires a submittal showing the extent of each placement, placement sequence and schedule for each placement.
Avoid specification limits on placement size
If the specifications include placement size limits, exclude them from your bid. As an alternate in your bid, price the specified small placement sizes and include the impact on schedule. The Owner will then clearly see an increased cost and an extended schedule as a result of this specification clause. And with no compensating benefits.