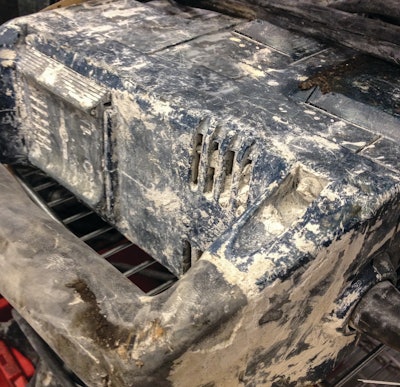
The durability of a tool is seldom discussed in articles or product reviews because the focus is on tool features and not how long its useful life will be. Tool reviews usually compare a single tool produced by several manufacturers; how they feel in your hands, how much power it has, how much work can be achieved in a unit of time, how long the battery will last doing a repetitive task, or by what contractors think as they test them in the field.
Here’s what some contractors who like working with tools, say influences their choices:
- How comfortable a tool “feels” in your hand and whether it feels “balanced”
- Brand loyalty; they buy the same brand tools time after time
- Being able to share batteries between tools is important
- They buy the tool brand their construction supply house sells
- For specific tools, such as a mixing drill, they buy only one brand because they believe it’s the best tool on the market
- Word-of-mouth recommendations
- They buy what they consider to be “industrial strength” or “professional grade”
- They buy brands with the best and fastest customer service when there is a problem
- They look for the most power
- Tools with the best dust control systems
You’ll notice that durability isn’t listed as a primary concern by the contractors above. Maybe contractors just assume “professional grade” tools will last a long time. That’s a valid assumption because tool manufacturers all have research departments that test new tools and tool parts to failure, redesign them and start the process over again.
Many also give tool prototypes to contractors to field test before they go on the market. But you should consider durability when you buy a tool too. Listed below is how manufacturers think about durability and address the issues. But durability also depends on how you take care of your tools.
The enemy
Mitch Burdick, product manager for Concrete Tools at Bosch Tools says the two biggest threats affecting tool life are debris (dust) and heat — driving over tools, dropping them in water, or baking them under a hot sun doesn’t help either. Dusty environments go hand-in-hand with almost all types of construction work, especially concrete work. In addition, many hand-held electric tools produce dust. Excessive heat can be just as destructive as dust and can occur by overworking a tool for a long period of time.
Heat and dust accumulations inside tool housings cause bearing destruction, armature problems, gear wear, and switch failure (replacing switches is the most common repair reported by most manufacturers’). Excessive heat buildup also causes tool battery problems.
How manufacturers build durability into their tools
Jim Bohn, director of product development for Bosch Power Tools USA, says users of hand-held electric tools — battery or corded — want them to be lighter, smaller, more powerful, dust free, and safer to use. Achieving all this is the challenge as they design, test and produce next generation tools. Here’s how manufacturers address durability issues.
Tool housings: You want them to “feel” right in your hands and look great. But they must also reduce vibration levels and be strong enough to resist physical abuse. Housings are made with plastic and metal — plastic surrounding the motor, switch and hand grip, and metal for housing gears, shafts, and bearings. Tool housings must absorb shock from drops and hold internal parts firmly in position.
If plastic resins are too brittle they will crack easily and break when dropped, so they are blended to be more flexible. This is indicated by “PA” numbers, often molded on plastic parts. PA-6 is good for tools. Fiber glass (GF) is usually added to the resin to increase toughness and this is listed as a percentage. GF 30 percent and above is considered good.
Tool manufacturers’ drop-test new tool models to be sure they can survive the rigors of jobsite construction. Each manufacturer has test protocols for each tool category. Depending on the manufacturer, tools are dropped from heights of 6 to 12 feet onto concrete floors — a process that can be repeated several hundred times. When parts fail they are redesigned.
Housings must prevent internal parts from moving and there are two types; “sleeve” (also referred to as “stacked”) and “clamshell.” Sleeve systems are the strongest. Paul Fry, vice president of Product Marketing for Milwaukee Tool, Brookfield, Wis., says they use stacked housing for tools such as rotary hammers because they can resistant extreme vibration.
Bohn says motors and bearings are solidly fixed to one sleeve to prevent movement. The other sleeve becomes a cover that slides onto the primary sleeve. Clamshell housings are less costly to produce and work well on tools with little vibration or ones subjected to less abuse such as laser devices. Tools for a non-professional market are often clamshell designs also.
Motors: Good airflow thru tools keeps motors and housings cool but the air should be relatively free of dust inside the housing. To minimize dust most manufacturers draw fresh air in from the back of tools such as angle grinders, pushing it out the front where dust is being created.
“But the challenge is to maintain good air flow thru tool housings as they become smaller and smaller,” Bohn adds.
Wayne Hart, communications manager for Makita USA, LaMirada, Calif., says they developed a system of channels and a “zig-zag” varnish system over motor windings to improve airflow and remove heat.
The use of brushless motors is increasing because they are smaller in size and more powerful. They also have fewer problems with heat and dust. Aaron Brading, Hilti’s business unit manager for Power Tools and Accessories, Tulsa, Okla., says their product line is currently about 30 percent brushless with their impact drivers and breaker lines being 100 percent brushless.
Gearboxes: Excessive vibration of shafts and gears affects both durability and worker experience. Bohn adds that how gears are made is sometimes an issue of first cost versus life cycle cost. Gears are spiral (helical) or straight cut (planetary). Spiral cut gears are generally considered to perform the best but they are more expensive to manufacture. Gear construction along with sealed ball-bearings (to keep grease in and dust out) and bearing location manage vibration and wobble. In addition manufacturers have backup systems to prevent dust from getting close to bearings.
Tools such as hammer drills, demolition hammers, and reciprocating saws produce a lot of vibration so each tool company has dampening systems such as counterbalances and air compression devices to increase user comfort without affecting a tools efficiently.
Gearboxes are packed with grease now, oil bath applications are a thing of the past, and increasingly tools are lubricated for life. Manufacturers closely monitor the development of better grease products to improve gearbox life. Significant heat can be generated in gearboxes so it’s wise to give tools a rest when they get hot.
Batteries: Lithium-ion batteries (LI) have changed everything, quickly replacing many corded tools. They are light weight and can store more energy than Nickel-Cadmium batteries. Brading says they sell three battery operated tools for every one corded tool now. Tool batteries are collections of 1.5 volt batteries connected to produce higher voltages and the desired amp hour ratings. The most used battery platforms for tools are 12 volt and 18 volts.
Battery capacity is rated in “amp hours” and this number is printed on every battery. Some also include “watt-hour” ratings (volts times amp hours) on their batteries. These numbers tell you how big the gas tank is—how much energy can be stored. For example, Chris Keffer, vice president DEWALT Cordless Products says 4 amp hour batteries can double the run time when compared to a 2 amp hour battery. Jason Feldner, group product manager for Cordless Power Tools at Bosch, says 4 amp hour batteries are the current state of the art, but 5 amp hour batteries at the same size and weight will be in the marketplace soon. Hilti sells a 6 amp hour battery by adding additional cells.
Fry says it is important to control heat buildup in batteries. This starts by designing and executing the very best battery cell, pack construction and electronics to reduce heat from ever building up in the first place. Some companies implement both mechanical and electronic designs to help limit and manage heat generation in their battery packs.
Lithium-ion batteries must be monitored for temperature and discharge rates so the best packs have sensors and proprietary software to manage temperature, current flow, and overload protection. This prevents batteries from operating when they exceed limits to prevent damage. The development of more efficient motors reduces heat in batteries, as do the heat dissipating materials and design of the housing around battery cells. Depending on the brand, the current operating temperature range for lithium-ion batteries is approximately -4-degrees to 140-degrees Fahrenheit.
A word about laser measuring and leveling tools
Hand held tools that measure distance and laser levels — including lasers that indicate plumb and perpendicular — are becoming increasingly popular so it’s worth including them in the discussion about durability. The two big areas of concern are damage due to dropping or vibration that affects accuracy.
Making robust laser measuring tools is easier to accomplish than with leveling instruments because there are no moving parts. Manufacturers focus more on housings that prevent the intrusion of dust and water. Olivier Vareille, group product manager, Measuring Tools, for Bosch says the screens for these instruments are a sensitive part. Surrounding them with rubber “over-mold” housing material is one way to offer protection.
Laser levels that automatically find level when you set them up have small pendulums holding the laser diode. Vareille says pendulum locks help prevent damage when the instrument is being transported. Some companies require that you engage the lock when you are done using it; other companies like Bosch automatically lock the pendulum when the instrument is turned off.
The biggest risk with laser tools is dropping them, so tool housings are designed to absorb shock. Companies perform drop tests onto concrete floors to ensure they have some resistance and still retain accuracy.
Ingress protection (IP) is the next most important durability issue. It relates to a device’s ability to keep out dust and water. IP numbers can often be found in tool specs. For instance an IP of 44 is where most entry level tools start — no real protection. The first number 4 refers to solid particle protection and the second number is for water. IP54 means the tool is fully dust protected and can resist splashing water; this is considered the minimum for a pro-grade measuring tool. Some units are IP 67, meaning they are completely dust tight and can be immersed in three feet of water without damage.
How you can increase durability
Professional tool companies do their best to produce durable tools; the rest is up to the user. How a tool is treated can add or subtract years of tool life. Here are some things you can do to increase durability:
- Use quality accessories, they can cause excessive tool vibration.
- Feel the gear box frequently if you work a tool hard. If it gets hot, give the tool a rest.
- Give batteries a rest when they feel hot.
- When you are done using a tool, return it to the case it came in for storing and transporting — especially laser equipment.
- Keep tools and batteries away from water, heat, and from direct sunlight.
- Perform preventative maintenance. Use an air compressor to blow dust away and bring them in for preventative service and re-calibrations.
How to buy durable tools
Tool stores and construction supply houses are a good place to buy tools because staffs are constantly updated by manufacturers and are aware of repair issues. Ask them about housing construction, motors, switches, gear boxes, and batteries.
When you buy:
- Don’t make your decision based on the lowest price
- Put durability on your want list
- Check tool specifications for vibration dampening systems, this is very important to your health.
- For corded tools, note how cords are anchored (or not) to the tool
- Read tool warranties carefully, there are significant differences between warranties concerning what’s covered and what’s not — what you are responsible for and what the manufacturer covers.