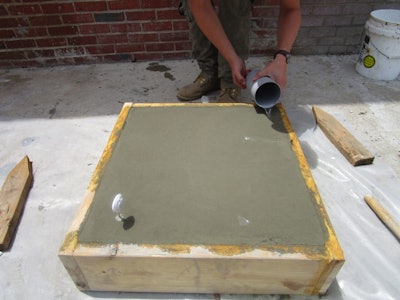
For many years it’s been assumed that applying cold curing water to hot concrete surfaces can cause thermal shock and cracking. As early as 1971, Section 2.2.1 of ACI’s Recommended Practice for Curing Concrete (ACI 308-71) advised that curing water used for ponding should not be more than about 20 degrees Fahrenheit (11 degrees Celsius) cooler than the concrete, because of temperature-change stresses which would be introduced with resultant cracking. More recently, ACI 308R-01 (reapproved 2008) “Guide to Curing Concrete” broadened the recommendation to not just water used for ponding, but to water used for continuous sprinkling and initial water application before covering with sheet materials.
“Curing water should not be more than 11 degrees Celsius (20 degrees Fahrenheit) cooler than the internal concrete temperature to minimize stresses due to temperature gradients that could cause cracking (Kosmatka and Panarese 1988). A sudden drop in concrete temperature of about 11 degrees Celsius (20 degrees Fahrenheit) can produce a strain of about 100 millionths, which approximates the typical strain capacity of concrete.”
Some people believe the cold water will result in shallow craze cracking and others believe it will result in deeper thermal cracking.
Section 11.3.7 on Industrial Floors in ACI 301-10, Specifications for Structural Concrete, changed control of curing water temperature for all applications from a recommendation to a mandatory requirement with the statement that: “Temperature of applied [curing] water shall not be more than 20 degrees Fahrenheit colder than the concrete surface temperature.”
That means, in many cases, curing water would have to be heated to meet specification requirements. If a contractor is placing an industrial floor during hot weather and is using well water for curing, the water temperature is likely to be between 55 degrees Fahrenheit and 60 degrees Fahrenheit. That would limit the concrete surface temperature to between 75 degrees Fahrenheit and 80 degrees Fahrenheit unless the contractor first heated the curing water. Ponding water to a depth of one inch on a 20,000 square foot slab would require about 12,400 gallons of heated water. The largest water trucks will hold between 4,000 and 5,000 gallons of water, so three of these would be needed for ponding. For an initial water application before covering with sheet materials, the required amount of water to be heated would be significantly less, perhaps 1,600 gallons. Do contractors ever heat curing water? We don’t know, but we’ve not heard of it. Does the surface temperature of flatwork often exceed 75 degrees Fahrenheit to 85 degrees Fahrenheit? Yes. But if the curing water wasn’t heated, would the concrete crack? Data was needed to answer the second question.
One form was was filled to the top. An immersion thermometer was inserted in the slab and the concrete temperature was recorded for two hours and 40 minutes until right after curing water was applied.
The Test
Forms were built with 2x8-inch lumber, with crushed stone put in the bottom to simulate a base course. Two 2x2-foot square slabs were cast in a parking lot—one to be cured by ponding and the other by wetting the surface then immediately covering it with plastic sheeting to prevent evaporation. Mixing water was heated to achieve a concrete temperature of about 90 degrees Fahrenheit and curing water cooled to 35 degrees Fahrenheit to achieve a temperature difference much greater than 20 degrees Fahrenheit.
The concrete batch quantities for a cubic yard are shown in Table 1. Previous testing of concrete with these proportions produced an fc’ (specified strength) of 4,000 psi. Cement, sand, and crushed stone were stored at an ambient temperature of 89 degrees Fahrenheit prior to batching and tap water at 108 degrees Fahrenheit was used for mixing.
To avoid possible head pack in the tilting mixer, about 80 percent of the mixing water and all of the crushed stone was first added and mixed for less than a minute before adding the sand, cement, and the rest of the water. The standard laboratory cycle—mix three minutes, rest three minutes, and mix two minutes—resulted in a low slump so more water was added to produce the final slump of 3-½ in. Total mixing time was 10 minutes. The concrete temperature was 85 degrees Fahrenheit and density was 149 pcf. Because the tilting mixer was loaded to capacity, there wasn’t enough concrete to make test cylinders. Instead, the slabs will be cored at 28 days to determine in-place strength.
During the test, one form was filled with concrete to an elevation about two inches below the top of the form to allow ponding.
Water was added on the ponded specimen. In one minute the curing water temperature rose from 35 degrees Fahrenheit to 50 degrees Fahrenheit.One form was filled with concrete to an elevation about two inches below the top of the form to allow ponding. The other was filled to the top of the form. An immersion thermometer was inserted in the slab filled to the top of the form and the concrete temperature was recorded during the following two hours and 40 minutes until right after curing water was applied. After consolidation by tamping, strikeoff, and a float pass, the concrete was monitored during the waiting period to determine when to start final floating and troweling.
After the initial floating there was no bleedwater, so final finishing was started when a footprint indentation was about one-quarter inch. After floating the surfaces of both slabs, they were hand troweled, then checked periodically to make sure the troweled surface was hard enough not to be marred by adding curing water.
As soon as water was added to a depth of one inch on the ponded specimen, an immersion thermometer was used to measure ponded water temperature. Results are shown in the graph. Note that in one minute the curing water temperature rose from 35 degrees Fahrenheit to 50 degrees Fahrenheit, and 15 minutes after ponding, the water temperature had risen to within 21 degrees Fahrenheit of the concrete temperature.
After seven days, the surface of the slab cured with plastic sheeting was wet and also checked for cracks. No craze or thermal cracks were noted in the slab.Several gallons of curing water were slowly poured on the other slab at one edge, flooding the entire concrete surface for several minutes. This was done because it had been suggested that adding all of the curing water in one area would cool that area more than other areas. Plastic sheeting was then placed on the slab and smoothed to eliminate most of the air bubbles. Boards were placed on the slab to hold down the plastic and shield the surface from direct sunlight to minimize mottling so any cracks would be more observable.
And The Results Are…
The surfaces of both slabs were examined for cracking just before curing water was added, and observed for cracking each time the ponded water temperature was measured. No crazing or thermal cracking was noted, including the area where all the curing water was added. The following day the surface was examined through the ponded water and no cracking was noted. The boards and plastic sheeting were temporarily removed from the other slab and a slight discoloration (zebra striping) was noted but no crazing or thermal cracking.
Table 1
After one week, water was drained from the ponded slab and the surface was examined as it dried to check for cracks. The surface of the slab cured with plastic sheeting was wet and also checked for cracks. No craze or thermal cracks were noted in either slab.
A temperature difference of about 60 degrees Fahrenheit between the concrete and curing water produced no crazing or thermal cracking. Thus a specified maximum temperature difference of 20-degrees Fahrenheit is extremely conservative.
This graph shows the measurement of the temperature of the ponded water after water was added to the ponded specimen. Note that in one minute the curing water temperature rose from 35-degrees Fahrenheit to 50-degrees Fahrenheit, and 15 minutes after ponding, the water temperature had risen to within 21-degrees Fahrenheit of the concrete temperature.
Pictured here is the dried surface of the ponded slab after seven days with the rim still on and caulk visible at the edges.Based on these results it would be interesting to know the origins of the 20 degrees Fahrenheit limit. Other than the statement that a 20 degrees Fahrenheit difference in temperature can produce a strain of about 100 millionths, which approximates the typical elastic strain capacity of concrete, there is no further explanation in the ACI documents cited. The 20 degrees Fahrenheit difference may have been the result of an elastic analysis based on the thermal coefficient of expansion of concrete, and assumptions that thermal contraction was fully restrained and there was an immediate drop of the surface concrete temperature to the curing water temperature. Based on the results of this experiment, assumptions made to calculate the 20 degrees Fahrenheit limit must be incorrect. It would be interesting to determine which assumption or assumptions are incorrect by performing a similar experiment in which sensors would measure concrete temperature and curing water temperature simultaneously during the curing period.
About the authors
Heather J. Brown, PhD, FACI is Chair and Professor for the Concrete Industry Management Program at Middle Tennessee State University. She can be reached at [email protected].
Jason Crabtree is Laboratory Manager for the Concrete Industry Management Program at Middle Tennessee State University. He can be reached at [email protected]
Acknowledgements: The authors appreciate the assistance of two participants in the National Science Foundation Research Experience for Undergraduates program, Caroline Pounal and Kyle Schuetrum, while conducting this pilot study. We also thank the American Society of Concrete Contractors for assisting with the study.