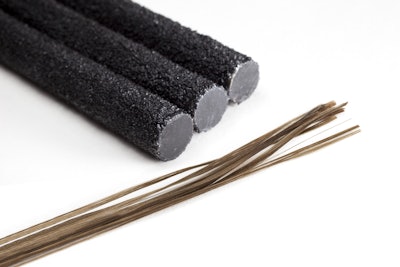
The Fiber Reinforced Polymer (FRP) rebar industry is about thirty years old. The industry started by molding aramid and carbon fibers with various thermoset resins, and then expanded to glass fibers mixed with both vinyl ester and polyester resins. It focused the majority of its time on glass fibers as they offer the best price of the three fibers mentioned.
Glass fibers come in three types:
- E-glass fibers – Low resistance to high pH (such as concrete environment)
- Corrosion resistant (CR) glass fibers – Same strength as E-glass with improved alkali resistance
- S-glass – Higher strength and alkali resistance.
As standards and usage guides have been developed by the American Concrete Institute (ACI) the FRP rebar industry has continued to grow and is found in many applications today.
About three years ago Erik Kiilunen started exploring the possibility of making FRP rebar using basalt fibers and along with co-founder Ken Keranen started the Neuvokas Corporation, Ahmeek, Michigan. Their product is basalt fiber reinforced rebar (BFRP) and they are calling their new product “Gatorbar” with sales starting in November of 2015. At this early juncture Neuvokas is only pursuing slab-on-grade and other “low engineered” markets while long-term testing is being completed.
Fibers from Basalt Rock
The quest to invent a fiber made from basalt rock goes back to the mid 1920’s when Paul Dhe of Paris, France received US Patent 1462446 A. In the 1970’s U.S. glass companies abandoned their development efforts to use basalt fibers in favor of S-Glass. It was in 1984 when the first commercial continuous basalt fiber (CBF) operations were established at a factory located near Kiev, Ukraine. Shortly thereafter the technology was declassified and released to the world. CBF is now manufactured in Russia, Ukraine, China and Ireland. The process of making the fibers involves crushing and washing basalt rock and then heating it to 2,550 degrees Fahrenheit. The fluid rock is then extruded through multiple tip bushings to make fiber 13 to 19 microns or .0005 to .0007 inches in diameter.
Basalt fibers are not toxic to water or air, will not react with any of the components of concrete and have a very high chemical resistance. Compared to other fibers such as S-glass, carbon or aramids used in concrete, they are also considered to be inexpensive.
Making basalt rebar
Most FRP rebar is made using the pultrusion process (a continuous manufacturing process of pulling composite materials with constant cross-section through a die) to wet fibers typically using vinyl-ester or polyester resins. Neuvokas worked out its own pultrusion process and Kiilunen adds that they preferred to use epoxy resin because of its advantageous properties. In the Neuvokas process basalt fibers are “wetted” with epoxy resin and then bars are shaped and compacted. The cost to produce FRP is very dependent on the manufacturing process speed and the ability to increase output speeds will yield significant cost savings. Kiilunen says the Neuvokas manufacturing method has been developed to produce rebar over ten times faster than the typical pultrusion process and he thinks they will be able to increase this speed significantly in the future.
Looking toward the future
Given that Gatorbar is a new product Kiilunen says their first marketing effort is to the slab-on-grade market. This includes floors, sidewalks, curbs, gutters, other paving projects, and other “low-risk” projects in terms of the engineering required.
“Engineers need a year’s worth of data before they can design our product into more complicated structural projects and we are currently only one month into a one year testing program being conducted by a neutral party.”
When testing is complete Neuvokas will put together design guides to enable engineers to use BFRP in their projects. Neuvokas will also look towards the ACI for further BFRP product acceptance.
Kiilunen says their first product is #3 bar (3/8 inch diameter) in 20-foot lengths. Their next introduction will be #3 bars in 40 foot lengths and after that they plan to begin production of both #4 and #5 bars.
A problem that all FRP products have is that bars can’t be field bent in the way that steel rebar can. So when engineers require bent bars for an application the bars must be pre-bent separately at the manufacturing plant. Kiilunen says they plan to provide this service in the future also.
Why you should consider using basalt bar
A primary goal for Neuvokas is to produce FRP rebar that is superior to steel rebar in many ways but also remain cost competitive with steel, perhaps even costing less in some applications. Their invention of a high-speed manufacturing process has helped them achieve this goal. As Neuvokas continues to increase its productivity the cost of FRP rebar will continue to go down. The low cost of their product compared to other FRP products and steel is a reason owners and contractors should consider its use.
Additionally in some cases the high tensile strength of BFRP allows engineers to switch project requirements from #4 steel rebar to #3 BFRP, allowing additional cost savings.
Corrosion resistance is another good reason to consider using BFRP rebar; it’s resistant to almost everything. Due to recent corrosion studies of epoxy coated rebar installed in corrosive climates, engineers are increasingly specifying rebar made from stainless steel or galvanized steel rebar and other more non-corrosive products such as FRP rebar. Compared to FRP and these other metal products BFRP offers great cost advantages.
Rebar weight is another reason to consider buying this product. You can ship seven times more product for the same cost and workers can assemble BFRP rebar mats easily, and then safely lift them into final position. On a recent parking lot project in Houston, Texas, workers set up layout jigs to assemble 20 foot by 20 foot mats with bars spaced on 12 inch centers, both ways. The completed assemblies weighed only 50 pounds and were easily lifted into position by two workers—safe and fast.
A primary reason for including rebar in slab-on-grade floors and pavement is to control both the amount of cracking in a slab and crack widths. BFRP has a much lower modulus of elasticity than steel rebar and this can be used to the engineer’s advantage. When slabs are properly designed, BFRP rebar can reduce the total number of cracks while keeping crack width within AASHTO specifications.
Closing thought
Basalt is one of the most common rocks on the planet, and is the only ingredient needed to make basalt fiber. In terms of corrosion or degradation there is almost nothing that affects it. GatorBar’s superior strength, low weight, zero corrosion, and finally product cost when compared to steel allow FRP rebar to be used in new applications. As more testing is completed and more design aids become available to help engineers include BFRP rebar in projects, its use will become more widely accepted.