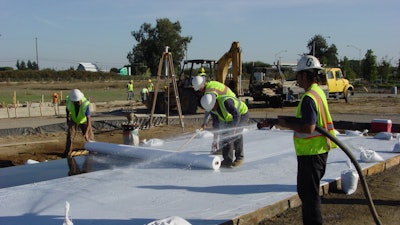
As discussed in Curing Part I – Why cure? (January 2016), curing is a critical concreting step that strongly influences the hardened concrete properties including strength, permeability, abrasion resistance, shrinkage, resistance to freezing and thawing and deicing chemicals, especially in the curing-affected zone or the near surface of the concrete.
There are many curing methods available for the initial, intermediate and final stages of curing concrete as shown in Figure 1. Initial curing occurs anytime between placing and final finishing of the concrete with the purpose of reducing the loss of moisture from the concrete. Final curing, between final finishing and the end of the curing period, reduces the loss of moisture from the concrete and controls the temperature of the concrete. Intermediate curing occurs between the final finishing and the start of the final curing and is typically required when the surface is too soft to start the final curing process.
Curing methods shown in Figure 1 consist of either adding water to the surface of the concrete after final set or techniques to minimize moisture loss from the surface of the concrete. Regardless of the curing method used, curing consists primarily of managing moisture loss and temperature of the freshly placed concrete.
While some of the curing methods listed in Figure 1 are applicable for vertical surfaces such as walls, columns and beams, the listed methods are primarily recommended for horizontal surfaces including interior and exterior slabs. Curing vertical concrete surfaces is less critical than curing horizontal surfaces. Because vertical surfaces are free draining and difficult to saturate, they are less prone to environmental attacks such as freeze/thaw damage.
Unlike vertical surfaces, horizontal surfaces such as floors and exterior flatwork must be hard and durable to resist wear from forklift, pedestrian and vehicular traffic and/or damage from exposure to freezing, thawing and deicing chemicals.
Sunshades and windbreaks
In most cases, erecting sunshades and windbreaks is easier said than done. For most projects, sunshades and windbreaks are not practicable or efficient options for protecting concrete from rapid evaporation and moisture loss. However, placing concrete indoors or under-roof is a workable and preferred option versus placing outdoors or in the open where the freshly placed concrete is defenseless against the ambient conditions. It is considerable easier and more economical to control moisture loss and to maintain proper concrete temperatures under-roof. In general, installing floors under-roof produces a higher quality product.
Fogging
By forcing water through special nozzles that atomize the water into a fog-like mist, the relative humidity above the slab can be increased and maintained to prevent surface drying of the concrete. As the humidity above the slab increases, the rate of evaporation from the concrete decreases. Standing upwind, direct the fog spray above the slab so the mist settles onto the slab creating a reflective or wet appearance on the surface. On a windy day, frequent or continuous fogging may be required.
It is okay if water accumulates on the surface of the concrete as long as the water does not mar, penetrate or erode the surface. Adding water to the surface by fogging is equivalent to replacing the bleed water that prematurely evaporated. Treat the accumulated water just like bleed water. Don’t finish the accumulated water into the concrete. Remove or allow the accumulated water from fogging to evaporate before finishing.
Liquid-applied evaporation reducers
When sunshades, windbreaks and fogging are not practical, applying an evaporation reducer (retarder) to the surface of the concrete after strike off and between the different finishing operations can help prevent surface drying. Similar to sunshades, windbreaks and fogging, evaporation reducers can minimize the risk of plastic shrinkage cracking and surface crusting.
Evaporation reducers are water-based mixtures containing chemical compounds that form an oil-like film over the surface of the concrete that reduce the evaporation rate of the bleed water. The effective time of these products is limited and depending on the rate of drying, time of concrete set and finishing operations, repeat applications may be required. Because evaporation retarders are about 90 percent water, they should not be worked into the surface of the concrete to restore the workability of the surface paste. Doing so will increase the water to cementitious materials ratio (w/cm) along the surface reducing both the quality and durability of the concrete.
Sprinkling with water and ponding
After final set, applying clean water by sprinkling (garden sprinklers and soaker hoses) or ponding provides excellent curing. However, these methods are difficult to use because of the challenges associated with obtaining an ample source of clean water, dealing with water runoff and building dikes or dams along the edges of slabs. If used, water must be free of harmful amounts of deleterious materials and impurities that will attack or stain the concrete. Also, the concrete must be sufficiently hardened so the surface is not damaged nor the surface paste diluted by premature application of the water.
Wet burlap, cotton mats and synthetic covers
A more practical means of applying water for final curing is wet burlap, cotton mats or other absorbent materials. These materials can wet cure by holding and supplying water to both horizontal and vertical concrete surfaces. Regardless of the material used, keep material saturated throughout the cure period and consider covering with plastic sheets or tarps to reduce the rate of evaporation.
When using burlap, thoroughly rinse with clean water before placing on the concrete to minimize the risk of concrete staining, do not let the burlap dry or it will absorb moisture from the concrete and always dry before storage to avoid mildew and rot that may affect the next job.
For commercial and industrial slabs, curing covers consisting of synthetic fabrics and bonded white-pigmented polyethylene films have become extremely popular due to the easy application, moisture retention and curing efficiency. Due to the polyethylene film, typically no additional water is required after the initial wetting, even for a seven-day cure period.
Wet sand, straw and hay
Wet sand, straw and hay are still viable options for wet curing but burlap, cotton mats and synthetic covers are more efficient, less likely to cause staining or discolorations of the concrete and provide more uniform curing. When using sand, it must be clean and thick enough (greater than ½ inch) to hold water uniformly over the slab. For straw and hay, thickness should be at least six inches and kept wet throughout the curing period to prevent concrete drying and to avoid the danger of fire.
Plastic sheeting and reinforced paper
Based on entrapping moisture within the concrete, plastic (polyethylene) sheeting, waterproof reinforced paper and liquid membrane-forming compounds reduce evaporative water loss from the surface of the concrete. For plastic sheeting, use a minimum thickness of 0.004 inches. Use white colored sheeting during hot weather and black for cold weather concreting. White sheeting minimizes heat gain by absorption of solar radiation and black sheeting maximizes heat gain.
When the as-cast appearance is important, plastic sheeting may not be the best curing choice. Plastic sheeting can cause patch discolorations or a mottled appearance due to variations in moisture and temperatures beneath the sheeting, especially if the sheeting becomes wrinkled. Periodically flooding the concrete under the sheeting can help minimize surface discolorations.
Reinforced paper is installed similar to plastic sheeting and like plastic sheeting, holes and tears should be repaired and if needed, the concrete re-wetted under the sheeting. For exterior applications and some interior applications, special attention is required to anchor or secure the sheeting to avoid the wind from tunneling under or displacing the sheeting.
Liquid membrane-forming compounds
These compounds are commonly referred to as spray-on curing compounds and work by forming a surface membrane that seals moisture into the concrete. Curing compounds are very effective and the preferred curing method for large surface areas or areas that are difficult to cure using other curing methods. Typically, these compounds consist of waxes and/or resins emulsified in water or solvents. Water-based compounds have become more common because of the VOC or volatile organic compound emission regulations. There are many different types and classes of curing compounds formulated for different applications. Be sure to read and understand what type and class of curing compound has been specified for your job.
Curing compounds must be applied uniformly and at the manufacturer’s recommended rate. For small areas, apply curing compounds with a wide, soft-bristle brush or paint roller. For large areas use a power sprayer with the appropriate wand and nozzles as recommended by the manufacturer of the curing compound.
Apply curing compounds immediately after the disappearance of the surface water sheen following the final finishing or texturing. Delayed application allows drying of the surface and increases the likelihood the curing compound will be absorbed into the surface instead of forming a water-retention membrane on the surface. If needed, re-wet the surface and allow drying to achieve a uniform damp surface before applying the curing compound.
Regardless of the curing method used, do not allow the concrete to dry during the curing period. If surface drying occurs, immediately re-wet the surface. Unfortunately, dry concrete will not absorb sufficient external water to restore the internal moisture loss.