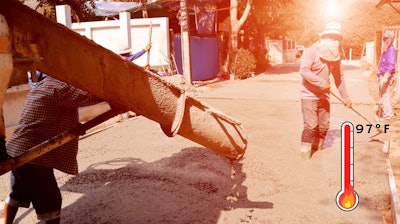
As a contractor, you’re likely used to ordering, placing, and curing concrete in hot weather. If precautions are not taken, this ambient environment can have an adverse effect on water demand, slump loss, and the time of setting of the concrete. Do you know what to do to ensure that the concrete develops the right strength and durability? The proper selection and use of concrete admixtures can be one of the most effective ways you can protect concrete quality. Follow these tips for a successful project in hot weather.
Tip #1. Understand the Definition of Hot Weather
Before we get to admixtures, we need to talk about what constitutes “hot weather” and how to measure it. According to the American Concrete Institute (ACI) Committee 305, hot weather is defined as any combination of high ambient temperature, high concrete temperature, low relative humidity, wind speed, and solar radiation that can impair the quality of fresh or hardened concrete. Generally, concrete temperatures of 80° F (27° C) or greater can be harmful to concrete. In warm tropical or arid climates, the potential for problems with hot weather can occur any time of year, and in other climates, issues typically arise during the summer months.
As the ACI definition shows, this is about more than air temperature. Higher humidity means an increased amount of water vapor in the air, and lower humidity means a reduced amount of water vapor in the air. For the purpose of concrete flatwork, high humidity can be beneficial because it lessens the chance for the concrete surface to dry out and develop plastic shrinkage cracks.
As for wind, the effects of high ambient and concrete temperatures, solar radiation, and low relative humidity on concrete may be more pronounced with increases in wind velocity. Combined, the air and concrete temperatures, relative humidity, and wind speed affect the rate of surface moisture (bleedwater) evaporation from the surface of the concrete. If conditions are right, rapid evaporation of the moisture can lead to premature drying of the concrete surface and the development of plastic shrinkage cracks (see Figure 1, below). If the rate of evaporation approaches 0.2 lb/ft2/h (1 kg/m2/h), precautions against plastic shrinkage cracking are necessary.
Figure 1. The effect of temperature, relative humidity and wind speed on evaporation rate.Master Builders Solutions, a Brand of MBCC Group
Tip #2. Know the Potential Issues That Hot Weather has on Concrete
Concrete issues can arise in freshly mixed concrete, hardened concrete, and decorative concrete, especially in hot weather. Some problems associated with freshly mixed concrete placed during hot weather conditions include:
- Increased water demand (see Figure 2, below)
- Increased rate of slump loss and a tendency for retempering
- Increased rate of setting
- Increased difficulty in handling, placing, consolidating, and finishing
- Increased occurrence of plastic shrinkage cracking
- Increased amount of air-entraining admixture to entrain air
- Increased need for early cutting
- Increased risk of cold joints
Figure 2, the effect of concrete mix temperature on water demand.Master Builders Solutions, a Brand of MBCC Group
In hardened concrete, hot weather can increase drying shrinkage and differential thermal cracking and permeability. It can also decrease compressive and flexural strengths, durability, water tightness, and uniformity of surface appearance.
It’s also important to note that decorative concrete should be handled differently. When placing decorative concrete in hot weather conditions, consistent water content from batch to batch should be taken into consideration, and not adjusting the slump with water. The use of a hydration control admixture is recommended, rather than a traditional retarding admixture as is the use of a workability-retention admixture to ensure slump retention and the utilization of a good-quality curing compound is essential. Decorative concrete needs more care than regular concrete, especially in hot weather, to ensure the color remains consistent and to the owner’s expectations.
The rate of setting depends on the temperature of the concrete. Concrete typically “sets” in six hours at 70° F (21° C) assuming no set control admixtures are used in the mix. At higher temperatures, the set rate is accelerated, losing approximately 33% of the set time per every 10-degree increase in ambient temperature. Consequently, at temperatures higher than 70° F (21° C), the setting time is shortened or accelerated. Ultimately, up to 50% of the strength could be lost in concrete is not protected or cured properly. Use the following table temperature to approximate setting time as tips for a successful project in hot weather.
Setting Time of Concrete at Various Temperatures
Temperature | Approx. Setting Time |
100° F (38° C) | 2 hours |
90° F (32° C) | 3 hours |
80° F (27° C) | 4 hours |
70° F (21° C) | 6 hours |
60° F (16° C) | 8 hours |
50° F (10° C) | 11 hours |
40° F (4° C) | 14 hours |
*Data provided by Master Builders Solutions (MBS)
What Affects the Temperature of Concrete When It's Batched?
Though this is more a consideration for the concrete producer, contractors need to understand what affects the initial temperature of concrete and, if applicable, what measures can be taken to control it to meet project specification requirements.
Concrete temperature at the time of mixing is influenced by the prevailing ambient temperature, specific heat and quantity of its ingredients. The approximate temperature of freshly mixed concrete can be calculated from the following equation:
T = [0.22(TcMs + TaMa + TcMc) + TwMw + TsMws + TaMwa]
[0.22(Ms +Ma + Mc) + Mw + Mws + Mwa]Where:
T = Final temperature of the concrete mixture
Tc, Ts, Ta, and Tw = Temperature of Portland cement, fine aggregate, coarse aggregate, and water, respectively
Mc, Ms, Ma, Mw, Mws, and Mwa = Mass of Portland cement, saturated surface-dry fine aggregate, saturated surface-dry coarse aggregate, mixing water, free water on fine aggregate and free water on coarse aggregate, respectively.
The temperature of concrete can be reduced by 1° F (0.5° C) by reducing:
- Portland cement temperature by 8° F (4 °C)
- Water temperature by 4° F (4° C)
- Aggregate temperature by 2° F (1° C)
Water is the easiest to cool and using ice as part of the mixing water will help reduce the concrete temperature. The ice must be included as part of the mix water and should not be more than approximately 75% of the amount of water required to meet the specified water-to-cementitious-materials ratio. ACI 305R has additional guidelines for the use of ice in concrete. As coarse aggregate is the ingredient with the greatest mass in concrete, changes in its temperature have a considerable effect on concrete temperature. The following measures will help to further control the concrete temperature at the time of batching or during the hydration process:
- Sprinkling and spraying of aggregates with water
- Shaded storage for aggregates
- Use of liquid nitrogen to cool the entire mixture
- Use of fly ash/slag cement
- Placing concrete at night or off-hours
The use of slower setting cements may improve the handling characteristics of concrete in hot weather. A 10-15° F (5-8° C) temperature rise per 100 lb. (45 kg) of cement occurs from cement hydration. The temperature increase from cement hydration is directly proportional to its cement content.
Fly ash, other pozzolans, and slag cement are used as partial replacements for portland cement and impart a slower rate of setting and strength development to concrete, both of which are desirable in hot weather concreting.
The requirements to achieve good results in hot weather concrete placing and curing are not different from those for other seasons. Concrete should be placed where it will remain and in shallow layers to allow adequate vibration. Exposed surfaces should be protected from moisture loss especially before final curing operations. If necessary and where feasible, shades and windbreaks should be used to help minimize moisture loss. Adequate curing measures should always be followed.
Tip #3. Use the Right Concrete Admixtures
Certain chemical admixtures are beneficial for concrete placed during hot weather. Benefits of using chemical admixtures in concrete include:
- Reduced water demand
- Improved workability during placing
- Slower rate of setting
- Lower rate of heat evolution
- Workability retention without added retardation
- Increased compressive strength
- Expanded concrete delivery range
- Reduced friction among aggregates
- In mass concrete, the peak temperature and/or rate of temperature rise is lowered, reducing the potential for thermal cracking to occur
Retarding/hydration control admixtures slow down the hydration reaction, slowing down the rate of setting of the concrete mixture. By slowing the initial set rate, the concrete mixture remains plastic and workable for an extended period of time. Hydration control admixtures, depending on the addition rate, can be used as a conventional retarder in freshly batched concrete, or to control hydration in situations where discharge could be delayed for an extended period of time, such as long-hauls. Workability retaining admixtures provide slump and workability retention without affecting the set rate of a concrete mixture. Depending on the specific application, they can be used in combination with retarding admixtures to provide exceptional slump and workability retention and the desired time of set. It should be noted that retarding admixtures alone will not result in quality concrete. Retarding admixtures should be used in concert with established concreting best practices to ensure quality concrete in hot weather.
Under adverse ambient conditions, contractors should order and take advantage of the benefits provided by synthetic microfibers in a properly proportioned concrete mixture to reduce or limit the formation of plastic shrinkage cracks. In addition, contractors can spray an evaporation reducer on the concrete surface to reduce plastic shrinkage cracking. Evaporation reducers form a monomolecular film that reduces surface moisture evaporation and, if necessary, they can be reapplied prior to final finishing operations.
When it comes to selecting a product, look for a company that has not only high-quality products but also the technical expertise to assist the entire construction team in the design, production, delivery, placement and curing of quality concrete in hot weather. Products that provide benefit in hot weather include those conforming to ASTM C 494/C 494M and AASHTO M194, the Standard Specifications for Chemical Admixtures for Concrete for Type B, retarding, Type D, retarding water-reducing, Type F, high-range water-reducing and Type G, high-range water-reducing and retarding as well as the requirements for Type B, Type D, Type F and Type G admixtures in the Corps of Engineers CRD-87. Workability-retaining admixtures should conform to ASTM C 494/C 494M Type S, Specific Performance.
Tip #4. Follow the Proper Curing Methods
As you know, concrete curing is critical to get the desired, long-term properties. The minimum recommended curing period is seven days (see Figure 4, below). While inadequate early protection of a concrete surface can cause plastic shrinkage cracking, inadequate curing will impair strength development and durability.
Figure 4. The effect of curing on compressive strength by age in days.Master Builders Solutions, a Brand of MBCC Group
Methods of curing include:
- Moist curing (ponding, continuous sprinkling, and fogging)
- Wet coverings (wet burlap, etc.)
- Impervious paper and plastic sheets
- Membrane-forming curing compounds
Tip #5. Speak to Your Concrete Supplier
There are many chemical admixtures available, so make sure to adhere to the project specifications or discuss options with your local producer or admixture supplier. They will have prior experience with a particular admixture and can help you conduct trial mixtures that best serve your needs.
Hot weather can cause a variety of issues in fresh, hardened, and decorative concrete. However, through the use of cooling concrete ingredients, avoiding prolonged mixing of concrete materials, protection of materials and equipment from hot weather, good scheduling, and the use of the appropriate chemical admixtures you can have the strength and durability needed in your concrete with the higher temperatures of the summer.
About the author
Richard Hubbard III, LSSGB, is the senior technical specialist for Master Builders Solutions. He has 45 years of experience in the industry with a focus on concrete admixtures.