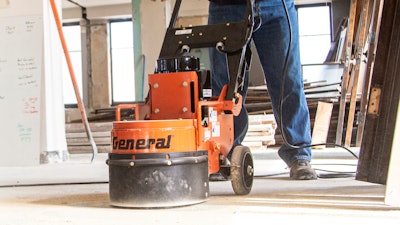
Surface grinders are the clear tool of choice for a variety of applications ranging from concrete polishing to surface preparation to coatings removal. But you’ll need more than just surface-level knowledge to achieve the desired outcome on a project. Errors can lead to more than just poor results; they can cause costly damage.
Getting the job done right requires the proper machine and attachments, as well as understanding the correct way to use them.
A relatively recent development on the market are high-speed grinders. Newer high-speed units have a higher price tag but they also can complete concrete grinding and polishing jobs more quickly. Of course, with faster grinding performance comes an increased risk of accidentally damaging the floor surface, making these best reserved for the most experienced contractors.
Low-speed grinders have been available for many years and are an ideal option for operators of all experience levels, since they provide better control over the operation and minimize the risk of surface damage. Since more users will gravitate toward this selection, the following is focused on low-speed grinders.
Power Source
The chosen power source for a surface grinder will often be dictated by the job location. Gas-, electric- and propane-powered surface grinders are all available. Electric models are the best choice for indoor applications where an electrical source is available. Keep in mind, however, that some models may work with a 115-volt power source, while others require 230-volt.
Gas-powered surface grinders may fit the bill for jobsites that don’t have electrical power sources, but these products should only be used in outdoor concrete applications, never inside. For indoor projects with no electricity, whether building or generator supplied, propane-powered models can be used.
General Equipment's MAGNETACH removal tooling system includes three attachments: PCD (polycrystalline diamond) coatings (bottom), Tungsten carbide coatings (middle), and the Diamond segment grinding system (top).General Equipment Company
Traditional or Magnet Attachment Systems
Surface grinders rely on attachments to perform the work, but there is more than one type of attachment system available. A traditional surface grinder design uses wood or plastic wedges to hold the grinding stones, diamond segments, or other attachments in place. Veteran concrete contractors know that it’s not uncommon for grinding elements to shake loose and fall off during operation. Keep in mind, though, that this can be a good thing. If the grinder catches a crack or obstruction, the machine may jump and/or the attachment will release helping to prevent damage to the machine. The gimbaled head of the grinder will flex/give to provide additional protection in such situations, plus it will follow floor contours for better results.
Another common attachment style for surface grinders features a magnetic retention system. The attachments compatible with these machines have magnets to hold them in place on the surface grinder head. Since attachments may need to be switched multiple times on a single application, the convenience of magnetic can provide a major advantage.
Magnetic systems also have a lower cost compared to traditional-style attachments. Furthermore, they attach more securely to the grinder. As mentioned above, having the attachment held too tightly to the grinder can result in machine damage or the grinder jumping when hitting an obstruction; however, a well-engineered gimbaled head design will help minimize these conditions when they occur.
If faced with the choice between a traditional or magnetic attachment system, my suggestion would be to invest in magnetic tooling. When you consider the lower purchase price, extensive matrix formulations, and wide range of available suppliers, the magnetic option provides a high ROI with a lower acquisition cost for the same, or better, performance.
More Information
Efficient Operation
Fully mastering the operation of a surface grinder requires experience; however, there are some basic tips for getting started. For example, many first-time users try to remove material faster by pushing and pulling the machine back and forth. Instead, a more effective—and more comfortable—technique is to slowly pivot the machine about its wheels.
The M-series gasoline-powered dual-head surface grinder, model SG24GHM, features a welded, unitized frame. Comes equipped ready to accept General's MAGNETACH tooling system attachments plus, products that use the Lavina/EDCO magnetic tool mount set up.General Equipment Company
Oftentimes, external weight is required for efficient concrete grinding and material removal. For instance, the removal of tough urethane coatings is often aided by adding weight to the top of the surface grinder, using objects such as cement blocks or bags of cement, to apply more pressure to the work surface. Many surface grinders are designed to support up to 300 lbs. of external weight. The best approach is to add weight gradually until the desired removal rate is achieved, rather than stack the maximum weight on the surface grinder all at once and inadvertently causing surface damage.
Finally, be sure to replace or rotate the attachments as needed to ensure maximum productivity. If necessary, contact the equipment manufacturer to find out the life expectancy of each attachment.
Successful surface grinding takes a combination of helpful advice and common sense to get started until an operator gains experience. While this was hopefully useful, always consult with the operator’s manual for the specific surface grinder in use; equipment manufacturers, distributors and rental centers can be helpful resources as well. Take advantage of the knowledge around us to help increase efficiency and lessen the daily grind.
About the author
Dennis Von Ruden is President of General Equipment Company, a family-owned manufacturer of specialized light construction equipment based in Owatonna, MN. He holds an engineering degree from the University of Minnesota, a number of design patents and has developed several surface preparation product innovations, which are in wide use. With 50 years of construction equipment industry experience under his belt in multiple market segments, he humbly admits, “I’m still learning.”