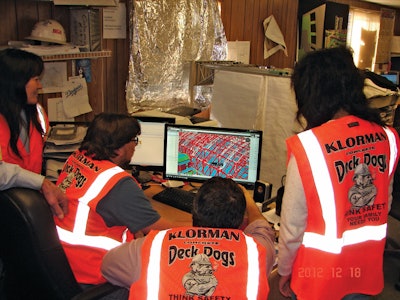
Developing closer connections between construction company offices and field offices is increasingly important now. Putting computers in construction trailers and connecting them to the web started the trend because reports, requests for information (RFI), payroll, and material use could be easily transmitted. More recently, tablets and smartphones are replacing some computer functions. By using a variety of software applications employees can transmit payroll information into company accounting software, upload photos of job progress for company-wide access, and receive messages in the field in real-time.
The new trend is to get up-to-the-minute, detailed information about productivity in the field in the form of cost account reports. Project managers and office management use the information to better plan and increase productivity on the job. This productivity information is also shared with company estimators so they can bid projects based on yesterday’s numbers. Depending on a company’s need, the increased productivity resulting from this process can be used either to bid more competitively or increase company profits. In the competitive, low-profit-margin world of today’s construction market, this can make all the difference in profitability.
The search to find new ways to mine data from construction activity can quickly take you to the edge of what’s known. Klorman Construction, based in Los Angeles, specializes in structural concrete high-rise building construction and is a good example of cutting-edge work in the technology age. Bill Klorman, the company’s president, says he is the champion for electronic and technical development for his company. “It’s good when the owner takes this role because when champions are lower in corporate ranks, management has to be convinced, slowing down the process.” He founded his company in 1980 with the goal of constantly staying technologically ahead in order to complete jobs better and faster than the competition.
The construction industry is much more competitive now, especially due to the downturn in the economy. Klorman believes the way to survive in this climate is to produce the same amount of building in smarter ways, with better planning and more efficient use of labor. His goal is to know what’s happening in the current moment and make decisions about how best to proceed. “The horse is out of the barn if you wait until after a construction task is completed,” he says.
The search for new ways to collect relevant data and summarize it in report formats for making decisions is Klorman's passion. His company is on the leading-edge in this technology area, and they consider Trimble, headquartered in Sunnyvale, Calif., to be one of their primary partners in this quest.
How Klorman cost accounts
Klorman Construction has always been interested in real-time cost accounting. They used spreadsheets to generate cost account reports when the company was organized. Then they began to experiment with software programs, adapting them to their needs. Next they included computer programmers on their staff to develop their own software solutions. But more recently their focus has shifted to mining field data from several sources and bringing them all together in report form to help managers understand how to make their jobs more productive. Here’s a brief rundown of software and hardware they use from Trimble for the exchange of information between the field and their office, as well as other project participants.
- Tekla. A Building Information Modeling (BIM) software specializing in structural concrete and steel design work. BIM drawings are intelligent 3-D project models with embedded data bases. They dramatically move data to the field for countless applications. BIM and Robotic Total Stations are the fundamental tools for real-time solutions.
- SketchUp. Recently acquired from Google, Klorman is able to use this program to quickly model 3-D ideas and share them with others related to a project.
- Meridian Systems’ Prolog Manager. A system of record for managing project information between the field and the office including: budget and cost management, change orders, communication, RFIs and field controls (QA/QC, daily reports etc.). It also incorporates jobsite data from other software into summary reports.
- Meridian Systems’ Prolog Converge. A collaboration solution to communicate work process and share files with the extended project teams over the Internet.
- Meridian Systems’ Prolog Mobile (for tablets). This system makes it possible to link tablet hardware to Prolog Converge for communicating RFIs, checklists, events, photos, payroll and material consumption from the field to the office. This helps project teams spend more time in the field.
- Robotic total stations. Offering layout and as-built QA/QC, they can be linked to the office via WIFI connectivity within the Trimble Field Tablet that is part of the Trimble Field Link construction layout solution. The software can interpret points defined within the Tekla Structures model. These instruments can control a wide variety of processes for concrete, structural steel, MEPS, excavation and grading.
- 3-D Laser Scanners. Instead of collecting just one point, these tools rapidly collect millions of points. Klorman uses theirs to collect as-built information for verification of design intent prior to construction, monitoring progress and QA/QC to show where the elements in a wall are located before it is closed up and provide as-built hand-over documentation.
- Vico Software. A virtual construction software solution that provides an integrated approach to coordination, quantity takeoff, cost estimation, project scheduling and production control.
- Thing Magic RFID. A wireless, non-contact system that uses radio-frequency to transfer data from a “tag” attached to an object or a person for the purposes of automatic identification and tracking. There are active and passive types. Active tags can transmit information to scanners up to 6,000 feet away. Passive ones must be scanned at close range. RFID tags can track materials, equipment and employees.
- Trimble AllTrack. Asset management software that allows contractors to track tools and equipment usage and reduce loss/theft.
Klorman Construction starts their real-time quest with BIM models of the construction; they build their own BIM from scratch to ensure anatomical accuracy for fabrication and erection. This might happen during the estimating phase of a project if the company particularly wants the job. Tekla is the BIM software they use primarily for concrete construction. The models are used to plan construction strategies, take off quantities, and make presentations to owners. In the field, project managers use the models for planning and for the construction.
Robotic total stations are used for laying out points, guiding excavating equipment and verifying work after it is installed — information the instrument can share directly to the office. Project managers log material usage into Prolog software each day and jobsite superintendents add payroll. Klorman says they set up 800 to 1,000 cost codes for a typical construction project so data is keyed to each code.
Klorman is using RFID technology too, deciding to track formwork first. They attached active RFID tags to form panels to track their locations. For example, when workers set form panels for a wall placement, the location is noted. As additional panels are placed, the percentage of completion for the task is adjusted. After concrete placement, workers move the panels to a new location and the sensors track that movement, initiating a new cost account. They are also experimenting with RFID chips placed in worker safety vests to track work by trade in each cost control area.
The company is also tracking tool and equipment use with RFID tags and bar codes for each cost code area. Klorman says an added benefit is they always know where their tools are so loss isn’t estimated anymore.
Bringing data from several places together in one report form is critical. Klorman uses Meridian Prolog and Vico Virtual Construction software for that. Their goal is to increase the amount and flow of data between their office and their construction sites to learn better ways to streamline the construction process. One of the benefits is real-time estimating is their estimating department can use data from the day before to create more accurate estimates.
The Trimble office project
Trimble is building a new office in Westminster, Colo.. It’s located across the street from the present office so Trimble staff can see the progress and visit the site often. Vince Stellino, a project manager for JE Dunn, the general contractor for the project, says it’s been a great opportunity for his company to learn new technology. They used Tekla to model the project for construction and are trying out Prolog Manager for cost accounting. Stellino says their accuracy is amazing. So far they have zero missed embeds and zero missed anchor bolts. “Because Trimble is located across the street we are often visited by their engineers to show us new products and discuss ideas. We are learning a lot from the experience,” he adds. The building is expected to open in April 2013.
How to begin the process
Real-time cost accounting provides you with up-to-date information, giving you the opportunity to make decisions that increase productivity and save money. It’s a process that requires time and you can’t just start doing what Klorman is doing.
Jon Fingland, business area manager for Trimble’s general contractor/construction management division, says your company's greatest asset is your past job cost history — no matter how informal it's your starting point to real-time cost accounting. Mining that data for the next similar construction project is a way to begin the process.
Another good first step is to start learning how to use BIM. Hiring employees with the skill is a way to do that. BIM models are rich in data and help to pre-plan jobs, increase efficiency and make fewer mistakes. Purchasing and learning how to use a robotic total station is another way to start.
Trimble sponsors the bi-annual “Dimensions Conference” in Las Vegas, with training both in a conference facility and at a quarry for hands-on demonstrations. It’s the best venue to learn about real-time costing and estimating, whether you are a beginner or experienced.
Why real-time is important
Klorman believes the world changes through the process of getting better information. “Ten years from now, real-time sharing with jobsites and real-time estimating will be the norm," he says. "None of this is going away and the process is becoming more affordable. In order to survive now, the ability to produce the same amount of building for less labor is what separates contractors.”
Jarrod Krug, the marketing communications manager for the building construction division at Trimble, says the goal for focusing on real-time solutions is to build lean, productive work forces. The effort also helps you get work in a more competitive environment.
In the past, production control has only available for billion-dollar projects. Now it’s available for jobs of all sizes at the same level of complexity. Working in a real-time climate lets you manage change; the data tells you where you are going, identifies cost implications and allows you to forecast. To survive in the construction world tomorrow, you need to start learning today.