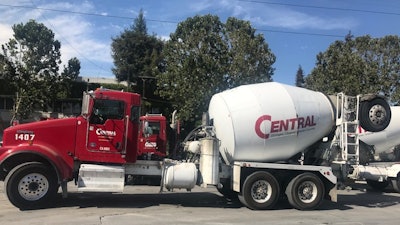
Serving the San Francisco Bay Area for more than 70 years, Central Concrete Supply Co. Inc., a Northern California business unit of U.S. Concrete, invests in products, people, and technology to drive ongoing success. Central Concrete designs and delivers concrete with high early strength, low shrinkage, and superior permeability for diverse projects, from commercial enterprises to large public works projects. The firm has in-depth experience designing and delivering higher-performing concrete while significantly lowering the carbon footprint of its mixes.
As part of its commitment to delivering the best possible products and production capabilities, the firm wanted to measure slump and temperature as concrete batches move from the plant to jobsite, and to gain insights for improvement throughout the concrete production process. The firm's choice in technology and investment in the associated concrete admixture has yielded considerable quality and operational improvements.
Each of Central Concrete’s trucks is now equipped with the VERIFI in-transit concrete management system, which combines sensor technology with predictive analytics to measure and manage concrete in transit. The sensors on the trucks monitor slump, temperature, load size, age, water, admixture, drum speed, and drum revolutions for optimum concrete consistency. Thanks to these automated capabilities, Central Concrete’s batch men can now remotely confirm the appropriate slump for each batch. The system automatically adjusts the water and/or admixture on the truck as needed so that each batch arrives on spec.
“The data we get from the VERIFI system is like keeping score at a baseball game for every batch of concrete."
—Patrick Frawley, P.E., Central Concrete Director of Quality Assurance
GCP’s VERIFI team worked closely with Central Concrete to help them make the most of the new system. “Our local GCP rep is great,” says Central Concrete Director of Quality Assurance Patrick Frawley, P.E. “He was a quality manager before he joined GCP, so he ‘speaks concrete’ and knows how to drive value from our investment.”
Central Concrete was awarded the 2020 Spare the Air Leadership Award in recognition for reducing greenhouse gas emissions from construction projects, while reducing and recycling waste and wastewater, through their sustainable mix designs and sustainable practices.Central Concrete Supply Co. Inc.
The real power of the system is in the data collected from ready-mix trucks, which is readily accessible through a dashboard. With this actionable data, Central Concrete can identify and resolve productivity issues. “The VERIFI system helps us to be more efficient operationally and understand exactly how to properly design our mixes. It enables us to be more competitive on our projects,” says Frawley.
The VERIFI system uses sensors installed on ready-mix trucks to enable real-time sophisticated, automated process monitoring and control during transit from the ready-mix plant to the jobsite.Central Concrete Supply Co. Inc.
Central Concrete is also piloting the use of GCP’s in-transit management (ITM) concrete admixture at seven of its plants. As part of this process, the plant batches concrete at 2 in. below the target slump and relies on the potent ITM admixture, added in micro-doses while the concrete is headed to the jobsite, to bring it to the optimum slump. “When you try to batch so that you arrive at a target slump, the variability of what arrives at the jobsite can be high,” says Frawley. If we batch low and then use the VERIFI system to adjust the concrete along the way, the consistency is vastly improved. That’s very exciting for us. It represents a big step forward in the quality of our admixture usage.”
Enhancing Concrete Batch Consistency
“The VERIFI system helps on many fronts,” said Frawley. “We target the batch slump lower than the ordered slump and rely on the VERIFI system to increase the slump along the way, so slumps arrive with more consistency. Having the ability to automatically add exactly the amount of water and admixture to the mix in transit means the concrete arrives on site and will pump and finish with more predictability.”
Slump management is the foundation of what’s useful, Frawley explains. “It’s what goes into the slump that is really key for us to manage.”
“We’ve made great strides in our leave plant time, which is now just six minutes, compared to the national average of 10-11 minutes.”
—Juan Gonzalez, Central Concrete Supply Co., Manager of Strategic Development and Sustainability
“Early on, there was no way to measure the consistency and quality of concrete other than to wait for 28 days to pass,” says Christopher Schenone, Vice President of Concrete Operations. “The VERIFI system was a real eye-opener. In the first year or two of having trucks enabled with the VERIFI system, we reduced rejected loads by roughly 75%. It quickly allowed us to pull back and see if certain batches were water-starved or had too much water. This enabled us to better design our mixes."
The VERIFI In-Transit Concrete Management System benefits all parties in the concrete delivery process – from ready-mix producers, to contractors and engineers.GCP Applied Technologies Inc.
Frawley compares the system to the score of a baseball game. While the traditional method of waiting for the full concrete maturity would be only paying attention to the final score. Instead, keeping score throughout, each player's action would be tracked every inning. With the system, Central Concrete was able to know the batch, leave plant, arrival, and dispatch slumps for every load of concrete shipped - in addition to all water adds. They would then be able to look at a year's worth of data to optimize mixes for cost and efficiency as well as drill down into the data to uncover issues, such as batching out of tolerance or a driver in need of a refresher on protocols.
“Our customers are happy because the hardened concrete properties are improved and the concrete arrives in a consistent way and will pump the same way, for each batch,” says Frawley. “That’s been a big positive for us.”
Enhancing Safety
One of the highest incidents of injuries on the jobsite is from trips and falls. With the VERIFI system in place, explains Schenone, Central Concrete is able to perform load-checks and have wash systems without the drivers having to get out of the truck—keeping drivers safe.
As VERIFI measures and manages the slump of the concrete in-transit, ready-mix drivers no longer have to climb up their ladders and stick their heads into the loading hopper to visually inspect their loads. Because of this feature, some VERIFI customers have even removed the ladders from the back of their ready-mix trucks, eliminating a major source of injuries. Other customers are improving the safety of their end of day washout process by adding admixture and water to the trucks through the VERIFI system. This has an additional benefit of reducing concrete build up in the drums and conserving water.
Sustainability
“We set a big goal of targeting zero waste,” says Gonzalez. “The VERIFI system has been instrumental in documenting returned concrete volume. Now we can see how much concrete is left on board without getting the truck weighed. With this data, we can quickly dose the returned concrete and repurpose it for a new project.”
A leading ready-mix supplier of sustainable concrete, Central Concrete has deployed solutions that help reduce their carbon footprint. “Our ITM concrete admixtures have reduced our reliance on portland cement, which consequently reduced embodied carbon,” says Frawley. “And by understanding our processes better and implementing process improvements such as reducing batch overdesign, we’re inherently becoming more sustainable.”
About the author
Jason Straka is the VERIFI® Product Manager at GCP. He has worked with VERIFI® for the last seven years covering Central Concrete Supply in the Bay Area. In this role he has managed the utilization and value extraction from the VERIFI® in-transit concrete management system. Prior, his experience includes 15 years in various roles in the ready-mix industry including quality control, sales and operations.