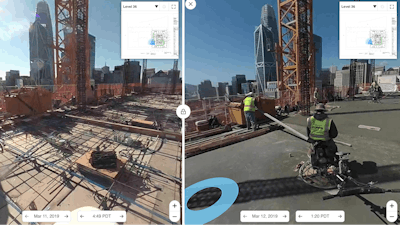
Many contractors will have processes to ensure a quality concrete pour--checklists or punch cards to standardize the material—verifications for fly ash, PSI, slump testing, even cylinder breaks. Curing plans too may differ, and this too must be communicated through to the field, with documentation to ensure plans were followed.
It makes a lot of sense to invest in methods to improve quality because rework is expensive.
One 2013 study found that major causes of rework were:
- Incorrect laying of forming
- Poor concrete quality
- Misinterpretation of the customer requirements
- Poor communication
- Inadequate project planning
Construction Project Management Software
Modern software-as-a-service (SaaS) construction project management software embeds these processes in a contractor’s overall business operations by extending enterprise software that extends from the early stages of project planning into field execution. Here are just a few ways construction software is addressing concrete quality.
According to Procore Vice President of Product-General Contractors Julian Clayton, Procore’s Action Plans enable contractors to standardize processes for their company or a specific project.
“After filling in general information fields, users can seamlessly proceed to assigning responsibilities and confirming essential steps,” Clayton said. “The initial phase of a concrete pour involves careful pre-planning. For instance, during the pre-pour meeting, discussion may revolve around logistics, equipment orders, and concrete mix design approvals. Leveraging the template, users can easily upload meeting minutes, equipment order specifications, and submittals. Subsequently, users can outline pre-pour activities and secure sign-offs from each trade, ensuring their work is completed before advancing to the pour phase.”
This pre-pour documentation lives on through later project phases in Procore for both back office and field users, from defining initial project requirements through to post-pour activities.
Concrete contractors' pour cards, time sheets, field reporting and more can be standardized in field productivity solutions like FieldFlo.FieldFlo
Specialty Contractor Software
FieldFlō, meanwhile, falls more into the field productivity software category, but does offer project management and other functionality for specialty contractors including dashboards, time and material tracking, inventory and equipment tracking and a form builder. But the software kicks in even before the project is won.
“We’re there in the beginning with our CRM (customer relationship management) software,” FieldFlō founder Roni Szigeti said.
This means FieldFlō captures customer requirements up front, with that data flowing into bidding, the plan and project specifications.
Customers can even have their own concrete pour card in the software.
“They're capturing the data and analytics that they need to from not only a daily field report, but also a QA QC,” Szigeti said. “That goes throughout the project lifecycle. And obviously, there's job costing and those are ancillary benefits for a concrete contractor, because at the end of the day, they're trying to make money. So they're doing jobs with job cost tracking and once the project is over, and after they've done their safety, a QA, QC, inspection, management reporting, they're required to generate a closeout report for the general contractor and the ultimate end user of the property. They can do the instant closeout report via FieldFlō, which has all the QA, QC, inspections, forms, documentation from the document vault, all in one package instantly. That can then be delivered to the end user, whether that be the GC or the building owner or property owner.”
But construction field productivity software products do more than standardize processes—they capture data from various sources and embed them in a system of record, in some cases using optical character recognition (OCR) to generate reliable information that can be used by everyone during and after the project.
“Those QA, QC inspections or concrete pour cards enable our customers to upload not only images, but documents,” Szigeti said. “So if they snap a photo or load a document, those resources are built into a report. If God forbid one of those situations happens and there's a failure on site, you can do root cause analysis, or get back up documentation within seconds, filtering down by date, or by form type, or close out report. The beauty of it is that testing for that day can be loaded right into the concrete pour card creating essentially one full document of the day, or of the pour.”
Reality Capture for Construction
Reality capture by Lidar or cameras on drones, tripods and handheld or wearable devices are powerful concrete quality tools. SiteAware’s product offering is used frequently to spot discrepancies before concrete is poured on complex vertical construction projects.
“Imagine all your projects ahead of schedule and zero dollars allocated for rework from your contingency budget,” SiteAware CEO Zeev Braude said. “That is what we can offer them in the areas we are very strong. For the first time, construction contractors can identify in real time the difference between the intent, the plans and the field work and address those gaps in real time so there is no rework. Rework is one of the biggest challenges in the industry. It creates unpredictable outcomes on a project—on the budget, the schedule or the final product.”
Braude said the company’s turnkey data capture approach can be viable even on smaller stick-built projects, but comes into its own on concrete-intensive vertical construction.
“If a contractor is doing concrete work, this is an immediate opportunity," Braude said. “Another thing that makes SiteAware a good fit is If you have a lot of systems in the walls, like hospitals where you have systems that go in the walls. And then those systems go from one level to the next. When you are pouring concrete and make mistakes and then pour concrete, those systems are at risk and you have to do a lot of rework. Another factor is exposure to budgetary risk and schedule risk, and that is more than 95 percent of the market.”
A pour can also be documented through construction photogrammetry data capture using helmet-mounted 360-degree cameras, according to OpenSpace Senior Sales Manager for Trades Josh Berger.
“Our customers are using OpenSpace Capture to document their job at each stage of the process, which in turn helps with coordination, progress tracking and safety inspections,” Berger said. “They see tremendous value in documenting before the pour, to ensure the reinforcement bars, spacers and ties are installed in accordance with the approved building plans.”
Capture, OpenSpace’s tool for capturing project walks, turns 360 photos into structured data in a system of record, making it more valuable for documentation than field notes in field productivity software that may contain cell phone photos of site conditions or completed work.
“Before the pour, OpenSpace customers are using our technology to improve coordination and quality control,” Berger said. “Pre-pour walks are improved with OpenSpace by capturing while you walk–saving a visual record with all of the areas viewed, automatically mapped to the drawings or BIM. They are able to be proactive and spot discrepancies, with a side-by-side comparison of reality to the drawings or BIM–sidestepping potential future complications. Our customer Nibbi Brothers General Contractors was able to confirm every cable, every opening, and every steel plate was in the right place before pouring the concrete for a complicated deck. In one case, they found their shop drawings had reversed east and west. By identifying this before the pour, they were able to make the critical adjustments and avoid significant rework.”
Another OpenSpace customer, Baker Concrete, uses OpenSpace for issue management.
“Using the Field Notes feature, they identify issues that need to be addressed, tracking them in the drawing and the capture,” Berger said. “When an engineer walks the site and asks to change something, they’ll easily note it in OpenSpace. This makes it easy to close out any fixes needed and keeps a record of these requested changes that can later be used as a backup for costs associated with a change order.” This in turn streamlines the request for information (RFI) process.
“Instead of a super or party chief seeing an issue and having to go to the office to talk with the PM team, with OpenSpace they tag an RFI requirement to the capture, adding notes to expedite the process with the visual record and context right there for review,” Berger said. “They also like how easy it is to create punch lists. Using OpenSpace, they are able to document in 360-degree view the walk-through and have an item-by-item punch list generated from it with easy access for all through a cell phone, iPad or CPU. The punch list items can be marked completed, assigned due dates, etc., and is much more efficient than loading photos into planning software or a PDF document.”
The indelible project record created by solutions like OpenSpace will also support contractors in documenting that work was performed according to requirements—which is invaluable during dispute resolution.
“After the pour, OpenSpace is used for site investigation–our customers are able to troubleshoot and solve issues, minimizing rework, by ‘seeing through the concrete’ and understanding where the footings are,” Berger said. “Concrete Frame Associates, for example, has been able to offer services and efficiently fix issues by going back in time to understand the dimensions and the location of the concrete members–and not just in the structural plans. They have also seen the benefits of having documented with OpenSpace for dispute resolution. You can go back in time and resolve any disputes over whether the job was done correctly or not, with a historical record of the job. Concrete Frame Associates has been able to answer questions that arose a year after the job when a chip appeared, as to whether they were at fault or not.”