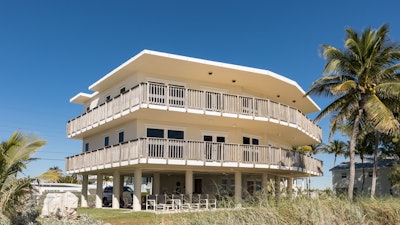
When John Pistorino set out to create the “Sandcastle,” a hurricane resistant demonstration building in Islamorada, Fla., he knew it would need to withstand the high winds and storm surges of the hurricanes that plague the Florida Keys.
Florida is the hurricane capital of the U.S., and Islamorada has been home to several hurricanes since construction on the Sandcastle started in 1991, including the powerful and destructive Category 5 Hurricane Andrew in 1992. A 1935 hurricane, one of the biggest to ever hit the area, had a storm surge of 25 ft. and 135 mph winds. Pistorino wanted this demonstration home, which sits 50 ft. from the Atlantic Ocean, to withstand that kind of battering.
"All the sand below the house was scoured away down to the bedrock by the storm surge, but the house itself wasn't impacted."
—John Pistorino, Principal of Pristorino & Alam Consulting Engineers Inc.
Pistorino brought a unique perspective to his demonstration building. As the Principal of Pistorino & Alam Consulting Engineers, Inc. (P&A), a Miami-based engineering firm, he had extensive experience in residential design and construction. He also served as a consultant to FEMA and other organizations, providing expertise on hurricane damage control, building codes, and related legislation.
"Early in my career, I had a contract with the U.S. Coast Guard to maintain the lighthouses that dot the Florida coast," he says. "Some of these lighthouses have been standing since the 1850s and I was fascinated by how they were designed and built by General George Gordon Meade. I wanted to use some of the same techniques for the “Sandcastle.”
After years of storms and saltwater, refreshing the appearance of the Sandcastle Hurricane resistant demonstration building (Fla.) required a coating to last. Image shows the building prior to the recoat.APV Engineered Coatings
What Does It Take to Make a Home Hurricane-Proof?
Pistorino took his cues from General Meade and designed his home as a three-story elevated structure with curved lines to deflect wind, a concrete frame, and round cast-in-place concrete support columns that would withstand hurricane-level storm surges. The support columns—rated to withstand 5,000 psi of pressure—extend down to bedrock. The foundation is drilled into the hard coral rock, keeping it from being undermined and eroded by storm surges and waves. The bottom floor consists of breakaway walls.
"I developed this hurricane-proof design approach for FEMA in the 1970s, so I knew it would stand up to whatever Mother Nature could throw at us," he says.
Find More Stories on Hurricane-Proof Homes:
Rebuilding the Smith House After Hurricane Sandy
4 Natural Disaster Preparedness Tips for Construction Contractors
FEMA Examines How Stronger Buildings Lead to Less Disaster Damage
Pistorino also specified laminated, high-impact glass for the home's windows and doors, along with 18-ga. solid steel protective shutters. Interior walls are a special form of drywall that won't dissolve like gypsum-based drywalls when saturated with water. The home's roof is a solid concrete slab with no shingles or other type of roof coverings.
"The idea is that when a hurricane hits, there is nothing to blow off and create damage to the interior," he says noting that the Sandcastle is designed to withstand winds of up to 200 mph.
Pistorino's design and construction strategy paid off. When Category 4 Hurricane Irma hit the Keys in 2017, most buildings in the area sustained heavy damage. The Sandcastle, however, stood up to the 120 mph winds with no damage at all.
"All the sand below the house was scoured away down to the bedrock by the storm surge, but the house itself wasn't impacted," he says. "We use the home as a demonstration house to prove its hurricane worthiness, and it was even featured on the Discovery Channel."
Durable Coatings Resist Weathering from Storms and Sun
A close-up of the Sandcastle's facade. The exterior coating needed to stand up to the Florida coast's high humidity, extreme UV rays, and corrosive saltwater - all without fading for a minimum of five years.APV Engineered Coatings
"It can be difficult to find an exterior coating that stands up to high humidity, extreme UV rays, and the corrosive power of salt spray for more than five years without fading," said Roberts. "NeverFade® Coatings with Kynar Aquatec® has demonstrated 15 years of performance in South Florida with no fading and chalking. I knew the product would be a perfect fit for the Sandcastle."
NeverFade® Coatings contain Kynar Aquatec®, a water-based weather-resistant resin that is ideal for air-dry, field-applied coatings. It can be easily applied to a variety of substrates, including metals, plastics, wood, concrete, stucco, EIFS, and previously painted surfaces.
Contractors applied NeverFade® Coatings from APV Engineered Coatings.APV Engineered Coatings
"The use of Kynar Aquatec® and complex inorganic pigments gives NeverFade® the ability to resist film erosion, chalking and fading caused by harsh UV exposure," explains Ernie Porco, an application engineer for APV Engineered Coatings. "Degraded and faded paint is so commonly seen throughout Florida, which is one of the harshest environments in the country." APV backs the coating's no-fade performance with a unique 15-year product-and-labor guarantee (transferrable to future building owners). If the coating fades by a ΔE of five or higher, APV will replace the product and cover the labor cost of re-coating.
"I was familiar with Kynar®-based finishes that are baked onto aluminum door and window frames in the factory," says Pistorino. "The finishes do a great job protecting the aluminum from pitting and corrosion caused by the salt-laden spray so common along the Florida coast. When Michael told me that I could get that same protection in a field-applied coating formulated for all surfaces on my home's exterior, I was very intrigued."
Each batch of NeverFade® Coatings is custom blended to match the individual customer's requested shade. In the case of the Sandcastle, APV matched the classic sand-color hue Pistorino specified for the home's stucco. The home's aluminum window trim and shutters were coated in a white and an ultra-bright white was chosen for the home's polyurethane-covered concrete roof to give it a high total solar reflectance (TSR) value.
"Because NeverFade® contains Kynar Aquatec®, it can maintain its high TSR for a long time, with minimal need for cleaning," explains Porco. "Other roof coatings—even those marketed at 'cool white'—are made of acrylic, which breaks down under UV exposure, allowing dirt, mold, and mildew to infiltrate the coated surface and reduce the TSR. Those other roof coatings also need to be applied at extra-high thicknesses because of this erosion, whereas just one thinner coat of NeverFade® provides longer-term protection and higher TSR values."
"A white roof with high reflectance values makes a big difference in keeping our A/C costs low," Pistorino says. "The roof shines very bright, especially compared with the other houses that surround the Sandcastle."
Project Team Extends Through Supply Chain
Michael Roberts of Lazer Distribution served as the project manager throughout the entire process. He worked closely with Capital Contractor Services, a South Florida-based NeverFade® certified applicator, to ensure a smooth application. NeverFade® certified applicators go through special training to learn about the chemistry behind the product. APV makes sure they understand details around substrate testing, color matching, application mock-ups, adhesion testing, and post-coating quality assurance so every job they do is perfect.
The coating process on the Sandcastle took the crew about five weeks to complete, which included a short pause for COVID-19-related travel restrictions. The crew used rollers to coat the home's 10,000 sq. ft. of concrete, stucco and masonry with 25 gallons of primer and 45 gallons of topcoat. Spray equipment was used to apply five gallons each of primer and topcoat to the home's 175 ft. of metal surfaces and 15 gallons of topcoat to the 4,000 sq.-ft. roof. One coat of primer and one coat of topcoat provided good coverage of all surfaces.
APV Engineered Coatings
Lazer Distribution's Roberts and APV's Porco were on hand throughout the project, from an initial site inspection to gauge the condition of the home's exterior substrates, to adhesion- and color-test mockups, checks of mil thickness and film build, and final inspection of the finished project.
"We paid special attention to all the details of surface preparation," says Porco. "We addressed areas where corrosion was present and fixed portions of the stucco that required minor repairs. This was a critical step to ensure that the coating system would last more than 20 years.”
"I've been working with Ernie for several years and they, along with the entire APV team, is incredibly committed to making sure the job is done right," says Roberts. "I don't see other suppliers with that kind of dedication and integration into the project team."
Lazer Distribution's Roberts also brought together other key players on the project team, including Arkema Inc., manufacturers of Kynar® Aquatec, and Bostik (the 130-year-old sealant and adhesive division of Arkema), which supplied PRO-MS 50™ hybrid sealant for the home's windows and doors.
The Sandcastle after a new fresh coating of APV Engineered Coatings' NeverFade® Coating.APV Engineered Coatings
"Michael Roberts introduced us to John Pistorino several years ago," says Ron Partridge, senior account manager, Fluoropolymer Coatings, Arkema Inc. "We've invited John and his team at Pistorino and Alam to attend our University of Kynar® training sessions, and we've worked closely with Lazer to generate awareness of NeverFade® among building owners and contractors. Together, Arkema, APV, Bostik, and Lazer act as one company with a shared mission and sense of integrity."
APV's Porco echoes Partridge's sentiment: "Even though scheduling conflicts prompted by the weather and the COVID pandemic, the entire supply chain was invested from start to finish to get the job done right. The Sandcastle serves as a perfect example of how we can bring the expertise of our supply chain partners together with superior products like NeverFade® and PRO-MS 50™ to protect buildings for the long haul."
"Michael at Lazer Distribution pitched in at the very end by doing some final detail finish work, and the project was completed a week before my daughter was married," Pistorino adds. "The house looked absolutely beautiful for the reception we held at the Sandcastle. I couldn't have been more pleased with the way everything turned out."
About the author
Erin Neff is director of marketing & business development for APV Engineered Coatings. She is responsible for generating new business accounts and managing key product development projects in strategic markets including architecture and building products. She also oversees external communications, public relations, advertising, as well as website and digital marketing efforts. She has been with the company since 2008.
Erin has a Bachelor of Science degree in Business and Marketing Management from the University of Akron. She is a NACE®-Certified Coating Inspector and is certified in sales and negotiations in professional selling via Sander Training®.