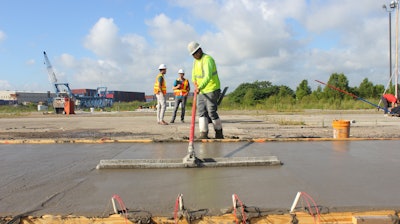
Work on developing an engineered cementitious composite, or bendable concrete, for mass adoption by LSU Construction Management researchers continues and the results are promising.
Most recently, the team constructed three 60-foot-long overlay sections on top of a section of deteriorated asphalt at the Louisiana Transportation Research Center in order to restore its condition. Section one was a jointless 2.5-inch-thick ECC overlay, section two was a jointless 4-inch-thick ECC overlay, and section 3 was a jointed 4-inch-thick regular concrete overlay that acted as a control.
“During construction, we gained insight on the large-scale manufacture of our ECC material, as well as the constructability of overlays with ECC,” said Gabriel Arce, research assistant professor in the Bert S. Turner Department of Construction Management and principal investigator on the project. “We realized that it was much easier and faster to build overlays with ECC than regular concrete. This was mainly due to the excellent workability of ECC and the lack of joints.”
Assessment of the sections was done by Falling Weight Deflectometer, or FWD, test, which evaluates the structural capacity of pavement by dropping a weight and measuring the deflection of the pavement due to the load drop. Next comes testing using the LTRC Pavement Research Facility’s 65-foot-long Accelerated Transportation Loading System (ATLas 30) to simulate truck loading for pavement testing. The ATLas 30 equipment is capable of compressing many years of road wear into a few months of testing to obtain performance data on the ECC material.
“FWD evaluation conducted before and after construction revealed a significant increase in pavement stiffness after construction, which means that the structural capacity of the pavement was increased,” Arce said. “This was expected due to the stiffening effect of the overlays.
“Now the interesting results will be the ones obtained after loading the sections with the ATLas equipment. Then, we will be able to quantify the deterioration of ECC against that of regular concrete; thus, demonstrating if ECC performs better than regular concrete.”
The ECC project is funded by Tran-SET, a collaborative partnership between nine major institutions and two community colleges, led by LSU, and established to address the accelerated deterioration of transportation infrastructure through “cutting-edge technologies, novel materials, and innovative construction management processes.” Its members are LSU, Arkansas State University, Baton Rouge Community College, Navajo Technical University, New Mexico State University, Oklahoma State University, Prairie View A&M University, Texas A&M University, University of New Mexico, University of Texas at Arlington, and University of Texas at San Antonio.
Additionally, The Lemoine Company, Quality Concrete, and the Concrete & Aggregatees Association of Louisiana (CAAL) have donated materials, equipment, and labor to the project.
Sweet concrete
Another Tran-SET project undertaken by Arce and his fellow researchers involves using sugarcane bagasse ash as an ingredient in their ECC materials to increase ductility. Preliminary testing has shown that the deformation capacity of the ECC has nearly doubled without losing any strength.
“Based on the experimental results we currently have, when replacing the fine river sand typically used in our ECC mixtures with SCBA, both the ductility and strength can be enhanced,” Arce said. “The degree of ductility and strength enhancement depends on the amount of sand replacement with SCBA and the type of processing that the SCBA is subjected to. We have managed to replace up to 100% of sand with SCBA with excellent results. Partial cement replacement with SCBA has not yet been evaluated and is the next step in our research.”