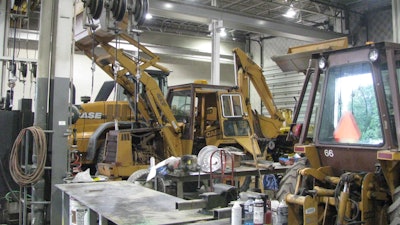
The equipment maintenance approach at a mid-size excavation and site work contractor was very typical. The owner has a mechanical background, knows every piece of equipment inside and out and takes pride in keeping his fleet in top condition. He was managing a relatively effective maintenance program based primarily on his individual knowledge and supported by some basic spreadsheets and paper-based processes.
But the owner is approaching retirement and the company is growing. The next generation of family ownership saw construction equipment maintenance software as an opportunity to make a smooth transition to a more automated, systematic approach to keep uptime high and costs low. Automating how preventive work was managed was one of their top priorities in making the move to fleet maintenance software, or computerized maintenance management system (CMMS).
No More Missed Maintenance
When the oil is changed in a car, the mechanic puts a small sticker on the windshield indicating the mileage and date for the next oil change. That works well for maintaining one or two family cars. A construction company, however, might have 50, 100 or several hundred expensive, sophisticated pieces of equipment, each with dozens of critical preventive maintenance requirements that should be completed at various intervals.
Unfortunately, many rely on systems not much more advanced than the sticker on the windshield. They track maintenance intervals on spreadsheets or on pieces of paper in files in the shop or on the equipment. One item that is often used is masking tape that is placed on filters and hoses with the date they were changed written with a Sharpie marker.
Offline analog systems make it too easy to miss or delay preventive maintenance. Equipment maintenance software, in contrast, brings automation to the process.
Contractors can populate maintenance software such as B2W Maintain with the timing and scope of preventive maintenance work for each asset.B2W Software
Contractors populate the software with the timing and scope of preventive maintenance work for each asset. This is based on recommendations of the manufacturer as well as the company’s own requirements and preferences. The system then alerts them automatically when the work is due, what should be done, what parts are required and if there is any relevant warranty information.
Maintenance managers specify how far in advance they want to see preventive maintenance notifications, which are triggered by dates, meter readings from equipment or both. The readings can be transferred from field logs, inspections or other sources or, ideally, they come into the system directly via telematics or GPS technology.
Construction equipment maintenance software, for example, can pull in engine hours, miles/kilometers, fuel consumption, as well as standardized data points for GPS positioning information from telematics providers. This software can also standardize the maintenance codes needed to ensure consistency and in-depth reporting capabilities of all preventive maintenance activities.
Cost and Time Savings
Automating preventive maintenance makes it far more likely that contractors will complete preventive work on time. When they do, the results are universal - breakdowns, downtime, and maintenance costs all decline.
When they don’t, these three metrics create a downward spiral. Skipping preventive maintenance increases the rate of unexpected breakdowns. That drives unplanned downtime, which disrupts productivity in the field and adds cost for rental or replacement equipment. Finally, as a maintenance strategy, waiting for something to fail and then fixing it is always far more expensive than preventing it from failing in the first place.
There are other benefits, as well. Equipment managers and mechanics are in high demand and their time is valuable. Automation optimizes that time by eliminating administrative work, improving scheduling and increasing “wrench time”.
With a computerized maintenance management system such as B2W Maintain providing visibility into the upcoming preventive maintenance requirements of the entire fleet, managers can plan work more efficiently.B2W Software
Finally, with a more automated and preventive approach to maintenance, contractors extend the lifetime of their equipment and make it safer to operate.
Personal knowledge and experience of mechanics, managers, and executives are vital to effective construction equipment maintenance. However, as companies and fleets grow, and assets get more advanced, that may not be enough. Supplementing expertise with software that makes preventive maintenance systematic and automatic is a proven way to increase equipment uptime and hold maintenance costs to a minimum.
John Kane is a product manager for B2W Software who has more than 15 years of project management, program management, technical data analysis and troubleshooting and reporting experience.