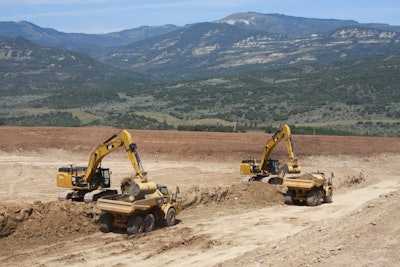
In 1999, John Kuersten and his wife purchased a small concrete business in Rifle, Colo., on the western slope of the Rocky Mountains. Since then, they have built Kuersten Construction into a successful civil contracting business that moves more than a million cubic yards of dirt annually and employs more than 70 people at projects across Colorado and Wyoming. Twenty percent of the company’s work comes from general contracting projects and 80% from heavy civil work.
Kuersten also operates DCP Civil (Dirt, Concrete and Pipe), a civil construction company headquartered 45 miles north of Denver in Berthoud, Colo. DCP Civil focuses on civil and earthmoving projects, gas and oil field construction, industrial plant locations, commercial development, road and bridge projects, large-scale irrigation, and mining and reclamation projects.
In 2012, the company began looking for a competitive advantage and strategies to win larger civil projects.
“At the height of the downturn, we were competing for larger civil projects and the competition kept getting cheaper and tougher. We knew we needed to find an edge,” said Kuersten. “We started by demonstrating Trimble grade control on one of our oil and gas compressor station jobs, and once we saw the benefits, it was clear that technology could make us more competitive.”
Kuersten purchased the Trimble GCS900 grade control system for several of its machines. Today, the team uses machine control for most medium and large-scale grading projects. Kuersten says the technology nets the largest returns on finished grading work and projects with frequent grade breaks because with manual grading, operators often dig through a finished surface without realizing it.
In 2015, Kuersten was hired by Piceance Energy as the civil contractor to build two reservoirs for the Harrison Creek Water Impoundment project in northwestern Colorado’s Piceance Basin. The lined reservoirs store fresh water for future oil and gas drilling. The 50-acre site included extensive grade variations, slopes, and swales and required moving almost 400,000 cu. yd. of dirt.
The Kuersten team worked with local Trimble dealer, SITECH Rocky Mountain, to equip several pieces of heavy equipment on the reservoir project, including scrapers, excavators, dozers and articulated dump trucks. Kuersten used two Cat D6 dozers and two Cat 336F excavators as their primary grading machines, each equipped with GCS900 grade control units − ranging from integrated GPS to systems rented from SITECH. The team deployed Trimble’s SPS985 GNSS Modular Receiver as a base station for GPS correction services.
The Kuersten team also mounted a SPS985 GNSS modular receiver as a rover on a utility terrain vehicle, which they used to measure quantities at the Harrison Creek job site. The rover and UTV collected volume data to create a baseline, which was then shared with the client’s surveyor to make sure everyone was in agreement on baseline volumes. As the earthworks progressed, the team used the rover data and Business Center-HCE to create quantity reports, which they included with their pay application. This quantity documentation eliminated mistakes in measuring or recording the volume of dirt moved, which helped the company get paid quicker and with less pushback.
“We’re loving the ability to create accurate quantity reports, and our clients appreciate it too,” said Kuersten. “So far it's been a huge benefit. In fact, on this particular project we had their surveyor come out and walk the job, and he couldn’t find anything more than 3/100 of a foot off design. The client’s surveyor told the owner, ‘Don’t waste your money, you don’t even need to pay a surveyor for this one.’ Customers appreciate that level of service from us.”
Kuersten figures he’s saved approximately $10,000 per project, on average, by eliminating the need for staking and grade checkers.
The Trimble GCS900 Grade Control System maximizes the machines’ and operators’ performance. The system uses ruggedized angle sensors, laser receivers, and GNSS technology to position the bucket or blade onsite. Design surfaces and alignments are then displayed on the in-cab control box. Trimble’s sensors measure distances and slopes and store measured elements as slope guidance models. Operators can follow the design on the screen and get to grade faster without sacrificing accuracy or quality of the final graded surface.
The team uses Business Center-HCE to prepare data for the build and to develop 3D site models. The designer collects information from the surveyors and the engineers and coordinates with the site to make sure the data matches. Then, the data is loaded into the control boxes and shared with the operators and job foreman so that all of the machines are reading the correct information. On the Harrison Creek Water project, Kuersten excavated 400,000 cu. yd. of dirt and met design targets without pounding a single stake – all in less than three months.
“Trimble GPS made grading easy,” said Kuersten. “Conventional staking and grading would have taken at least 30% longer. With steep slopes on the reservoir project, our operators ran the mass excavators and scrapers consistently within a foot or less of grade and we eliminated the surveyor entirely, so it keeps the job flowing smoother. We were then able to use a couple of dozers to get to finished grade without stakes or over excavation.”
Piceance Energy was extremely satisfied with the excavation and grading work provided by the Kuersten team.
“These Harrison reservoirs are 8,500 ft. above sea level, so completing work in the fall was critical so the liners could be installed before winter,” said Kuersten. “The grade control technology cut 30% or more time off the schedule for us, which is a huge time savings compared to traditional methods of staking and cutting. The owner has had nothing but good things to say, including how smooth the job went and how good it looks. That’s good for us and our customers.”
Kuersten explains that he is continually looking to balance the cost of investing in construction technology with productivity gains and ROI. In addition to tackling another water treatment facility project for Black Hills Energy, the company is now bidding modeling, sub grade and blue-top prep work for one of Denver’s largest paving companies.
“We know how to be successful with machine control technology on these grading projects, so we’re chasing as many of those as we can,” said Kuersten. “We're also continually looking for ways to use the technology to increase the scope of work we can do, including this new subdivision project. We think demand for this type of work will continue to grow, and we know we are more competitive using technology.”