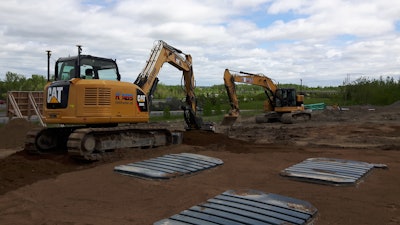
It appears that when S. Dilawri Automotive Group does something big, it is really big. Dilawri is Canada’s largest group of auto dealers with franchised dealerships representing 30 automotive brands throughout Quebec, Ontario, Saskatchewan, Alberta, and British Columbia. With more than 3,500 employees, Dilawri Group continues to expand its footprint in Canada, building on its 32-year-old history.
Its most recent venture is unfolding with the construction of a four-dealership auto mall in Barrhaven, Ontario. Situated in the greater Ottawa area on the northwest corner of Highway 416 and Fallowfield Road the prime location is expected to serve Nepean, Barrhaven, Manotick, South Kanata, and as far south as Kemptville.
Dilawri contracted Ottawa-based MB Ford Construction Ltd. as the general contractor and construction management firm for the project. MB Ford specializes in automobile dealerships and auto malls. The company, in turn, subcontracted the complete site prep of the 350 meters wide, 450 meters long site to Rabb Construction Ltd., Richmond, Ont.
Site Prep in Sequence
Founded by two brothers, Rabb Construction is a medium-size heavy-civil contractor serving the greater Ottawa and Eastern Ontario markets. The company was formed in 1992 after the brothers returned from the university with their civil engineering degrees.
The new Dilawri Auto Mall is a sizeable, heavy civil site work project for Rabb Construction. The facilities for the Auto Mall will be situated on the approximately 15-acre site. Rabb needed to level and grade the former stone quarry for the four auto-dealer elevated building pads and their surrounding inventory lots and customer parking. The contract also includes excavating three approximately two-acre stormwater runoff retention ponds. Rabb is also responsible for constructing the on-site sewage systems.
The project site was a rock quarry where blasting occurred to excavate out the bedrock, which was used to make crushed stone. The quarry was active in the 1970s. The very large open pit was converted into a dump site for clean fill, which benefited all of the local construction contractors.
“We were supplied a full set of design drawings, grading plans, stormwater management plans and structural plans, which were completed by a team of consultants and designers,” stated Brenda Burrows-Rabb, P.Eng., general manager of Rabb Construction Ltd. “Using this design information, we developed a 3D site model to use with our Topcon GPS machine control system on our equipment. This site model is also available on our Topcon Tesla tablet data collector hand-held rover. Having field access to the site model increased our efficiency and accuracy.”
Burrows-Rabb said: “We had a fairly aggressive timetable in order to accommodate the two dealerships that were to be built as soon as we finished the site preparation. Plus, there was a commitment for the third dealership, and we needed to complete enough work on the fourth location to help the owner market it.”
It was a frigid day, when Rabb Construction Ltd. first arrived on the snow-covered site. The dynamic compaction process was completed first, with the stone building-pad elevated 1– to 2-metres above existing grade. Once the building pads were constructed, the site was ready for the initial site work to begin.
The sequence of tasks that Rabb Construction tackled from day one included:
Initial site preparation
- STM sewers to manage surface water
- The building excavation, backfill, and interior plumbing
- Install the fire tank network – excavation, installation, backfill
- Install the water main for water service and fire protection
- The sanitary sewer system was established
- On-site septic systems installed
- Excavate and shape the storm water retention ponds
Tight Deadline and Critical Elevations
To perform the earthmoving on the project, Rabb used four large-size Caterpillar crawler hydraulic excavators including a Cat 321D equipped with the Topcon X-53i excavator system and two dozers, a New Holland DC80 and a Cat D6R high track dozer equipped with a Topcon 3D-MC2 systems. The contractor moved 20,000 to 25,000 cubic meters of material on the Auto Mall site. The site is balanced, so it became a matter of re-locating the fill material as per the design grades. The grade needed to match into the existing grades at all of the property lines.
“The Topcon systems helped us achieve grade on this challenging site and saved us a tremendous amount of time, which has helped us meet the tight deadlines,” Burrows-Rabb said. “The ROI on the technology was immediately obvious to us. We don’t feel a need to quantify what we already know, which is why we purchased a second unit as quickly as we did.”
Help in selecting the GPS machine control systems and training was provided by GeoShack Canada, based in Ottawa. According to Burrows-Rabb, the operator training on the GPS controls made a difference in confidence for using the technology.
“We learned that the Topcon 3D-MC2 dozer system is the latest technology on the market and is said to be twice as fast as any other 3D dozer system," she noted. "I don’t have enough experience with GPS machine control systems to verify. All I know is that it’s fast and precise. We’ve eliminated the necessity for multiple passes and there is no need to re-visit any of our work.”
The X-53i 3D control for excavators helped increase the Cat 321D’s versatility. Burrows-Rabb said the system’s 3D positioning capabilities helped the excavator for sewer installation for bedding grade, rough grade, and “just about every task – it is very useful.”
““We knew about Topcon machine control for some time – however, it is an expensive investment,” stated Burrows-Rabb. “It became evident as we used it that it is completely worth the capital investment. Our efficiency has greatly improved. For example, with the grading of the parking lot stone the D6R dozer with GPS control can be operated without foreman supervision. This frees up key personnel to complete other required work.”
For Rabb Construction, achieving the correct grade according to the provided design drawings and elevations was critical, since it was preparing the sub-grade for the asphalt paving and concrete contractors. All quantities of crushed stone, asphalt and concrete materials to be supplied are based upon the Rabb-produced sub-grade elevation. The elevation needed to be accurate and match the city-approved grading and servicing plans.
Elevation accuracy on the auto mall site was also critical for stormwater management and for the septic systems.
Open for Business
The project has progressed and the end is in sight. The Chrysler dealership and the Mazda dealership are now open for business. Nissan, the third dealership, is scheduled to open in June 2017. The building on the fourth stone building pad is currently in the design stage.
As Burrows-Rabb reflected, “We were met with difficult site conditions and a very aggressive schedule. Certainly, having the machine control technology has helped us tremendously. Without it, we would be less efficient and it would have been more difficult to meet the timeline pressures. I’m proud that we’ve done good work here.”