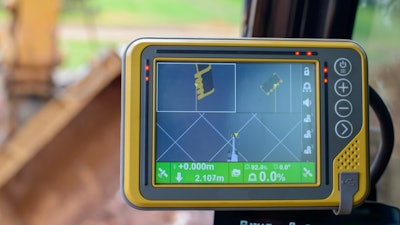
On the jobsite, safety, efficiency and uptime are key to success in a market that's facing tighter margins, a smaller labor pool and the need to do more with less. As contractors and crews face increasing demands for optimized productivity, advancements in machine control system capabilities are enabling operators to have more intuitive control over their work trucks.
From the ability to remotely customize cab settings and control attachments to improved diagnostic capabilities and troubleshooting, the benefits of control systems are revolutionizing the construction industry by taking the guesswork out of operations.
The best machine control systems combine strong, reliable hardware with flexible, intuitive software that leverages large amounts of data to help equipment operators more accurately position and operate attachments, such as electric, hydraulic and articulating cranes, and provides them with real-time load and safety information.
Oftentimes, a system's technology allows decisions to be made based on data, in addition to relying on the skill and experience of the operator. As the construction industry faces ongoing challenges with labor shortages, data-driven control capabilities will become even more critical. The construction industry averaged more than 390,000 job openings per month in 2022, the highest level on record, according to data from Associated Builders and Contractors.
A proprietary workforce shortage model developed by Associated Builders and Contractors found that the construction industry will need to attract an estimated 546,000 additional workers on top of the normal pace of hiring in 2023 to meet the demand for labor. In 2024, the industry will need to bring in more than 342,000 new workers on top of normal hiring to meet industry demand.
As the industry works to get operators onboarded and trained quickly, safely and efficiently, advanced control systems can help minimize the downtime needed for training while also helping to increase operators’ performance and accuracy as new hires learn the ins-and-outs of operating a work truck.
Continued technological advancements and optimized functionalities with control systems are enabling operators to have control over their productivity, reliability and safety in the palm of their hand.
Improved Safety, Efficiency
One of the biggest benefits of control systems is the focus it brings to safety and efficiency. Control systems provide operators with a host of controls to ensure safe operations on the jobsite.
Some safety features enabled by control systems include the ability to run stabilizers from a wireless remote control so that operators have a clear view of what's around them when deploying the stabilizers. This allows the operator to deploy stabilizers and observe the unit position for leveling from an improved vantage point. Data collected by the system also provides operators with information about the load and safety checks and warnings from the remote alert operators when they are reaching crane load capacity.
When it comes to efficiency, control systems help eliminate downtime between tasks by allowing the operator to not have to walk back to their truck every time they want to turn something on or turn something off. For example, operators are able to turn on a compressor or engage a PTO right from the remote to prevent them from having to climb off the piece of equipment they're operating, saving time and resources on the job.
Customization Capabilities
Machine control systems also allow for the customizable programming of work truck operations. Control systems can be easily adjusted from their default settings allowing work trucks, which are designed to take on many different applications, the ability to operate in different jobsite environments.
With control systems operators can individualize multiple operations, including things like flood lights, compartment lights, and more. Being able to easily program different lighting setups is a valuable feature that helps to ensure operators are able to accommodate every environment they work in.
Upgraded Diagnostics
In addition to the safety features and customization options, control systems enable improved diagnostic capabilities that help operators to be more productive. Operators have the ability to see inputs, outputs, crane fault codes and more, which empowers them to quickly and efficiently diagnose issues to maintain optimal uptime.
In the advent of electrification, greater operational precision and increased data collection will help to make machine control systems even more adept and efficient. Electrification improves data capture opportunities because battery powered equipment generates more data than traditional diesel-powered equipment and provides deeper connectivity, leading to improved equipment insights and diagnostics.
With advanced load management capabilities, improved crane diagnostics, customizable cab operations and more, advancements to control systems are helping to keep operators well-equipped for any job at hand.