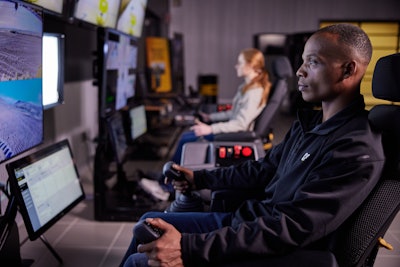
It’s a bit of a stretch to realize zero human interaction in the operation of heavy construction equipment. However, make no mistake. The move is on to make it happen.
An operator controls an excavator using a belly box.Caterpillar
“Part of the problem involves the environmental context,” said Scott Hagemann, senior market professional for Caterpillar. “Autonomous trucks work in a mine, where the location is isolated; there’s no traffic or people in harm’s way during the operation. But with grade control, you’re usually operating in a densely populated area, where there are too many factors to trust safe operations to pure robotics.”
So, for now, automated grade control is the best way to improve precision, safety and efficiency on a construction site. That is...for now.
On the Road to Full Autonomy
The Society of Automotive Engineers identified six stages of automation, starting at Stage zero and progressing to Stage 5, the yet-to-be-realized holy grail of vehicular automation. These stages progress as follows:
- Stage 0 – No automation
- Stage 1 – Singular automated driver assist (for example, cruise control)
- Stage 2 – Dual automated driver assist (for example, cruise plus braking control)
- Stage 3 – Human monitoring and interdiction of autonomous operation
- Stage 4 – Full autonomy within set boundaries (for example, driverless taxis inside geofenced areas)
- Stage 5 – Fully self-driving vehicles without drivers or boundaries
Where haul trucks might operate at a Stage 4 level of autonomy in a mining environment, Stage 3 bulldozers and excavators are equipped to support automated grade control on construction sites. Common operator assists might include blade and bucket controls, monitored by an in-cab operator who reads grading progress on an output display and can override or refine the operation using onboard commands.
Remote control is also possible when performing grading operations under Stage 3 conditions. In this instance, the operator is not on board the vehicle but operating it from a separate location using a joystick or belly box.
“Technically, you could perform the operation from your living room, oceans away,” said Cameron Clark, earthmoving industry director for Trimble. “The idea would be to ensure safety in a diverse work environment, such as along a steep dam or embankment or provide convenience where travel or labor shortages might inhibit job progress.”
Advancements in Grade Control
Automated grade control is the best way to improve precision, safety and efficiency on a construction site.Caterpillar
“The last mile in the journey to fully autonomous will come when we can consistently and accurately read and react to dynamic elements in the immediate environment around a fully equipped machine in motion,” Hagemann said. “When we can fully know the position of everything on the machine, not just the blade but every corner, elevation, from the top of the machine to the bottom of the tread, we’ll at last be into Stage 5 autonomy.”
In the meantime, automated grade control is continuing to advance. The ability to make data-driven design decisions and push a button to automate them has been enhanced by ever-more sophisticated software used on earthworks systems. As geo-sensors send data from the extremities of the machine to the operating system, onboard software steers and controls the blade to execute the grade accordingly.
“Data fusion is the enabler behind any automated grading system,” said Clark, who helps product managers and developers push the envelope toward improving grade control. “As more intelligence gets added to grade control systems, we get closer to autonomous grade control and the goal of getting the operator out of the cab.”
Get into the Game
GNSS Technology and grade control eliminated the need for survey stakes or need for surveyor to re-stake when one is knocked down.Trimble Construction
Operators can use control pads on smart phones to connect to a system wirelessly and update plan changes or troubleshooting information. Simple 2D technology that integrates onboard inertial measurement sensors with an in-cab monitor can produce highly accurate single or dual angle slopes efficiently, potentially paying off a technology investment on a single large project.
“Starting small, with a 2D system and basic laser technology, is usually the easiest way to see results and get familiar with the technology,” said Bob Flynn, construction precision sales manager for CASE CE. “For more experienced users, I’d recommend investing in off-board solutions that help with data management. These are typically under-utilized but can offer valuable insights into jobsite productivity.”
The key is to make sure the system matches the application and not to overspend. Most solutions are upgradable and evolve over time, so the best advice would be to visit a dealer, discuss your situation, and demo a few products.
“Just as you wouldn’t use a 20-pound sledgehammer to nail a picture into a wall, you never want to purchase technology simply for technology’s sake.” said Hagemann. “Go in with a few use cases and solve those first. The rest will fall into place.”
Noteworthy Concerns
Until automated grade control makes the leap to autonomous, contractors would do well to pay attention to a few basic best practices when using automated technology. Training may be at the top of the list.
Most manufacturers offer excellent training materials and support to get new operators up to speed quickly on the technology. Some even provide remote or onboard training by way of downloadable videos for instant playback in the cab. An operator can simply punch up a help topic and watch a how-to instructional video to correct on-the-job issues without contacting an expert or leaving the site. This is critical for the safe use of automated systems and for accelerating the contractor’s return on investment (ROI).
As tight labor markets continue to press contractors to do more with less, the adoption of automated grade control in construction continues to rise.Caterpillar
Also, be wary of how reliable your technology really is. Ask around and do your homework before you buy.
“It can be easy to fall in love with technology just because it’s technology,” said Trimble’s Clark. “If a cable breaks or a sensor gets damaged on site, suddenly your machine can’t be used. So, from entry level to premier offerings, work with reputable dealers and make sure to keep quality and reliability high on your list of solution priorities.”
Enjoy the Benefits Along the Way
While the journey to full autonomy may not be complete yet, the benefits provided by positioning yourself for the breakthrough are many. Within the confines of automated grade control, consider these benefits:
- The safety afforded by not having to position surveyors on the site
- Reduced rework, material usage, fuel cost, environmental impact, and need for skilled labor
- Increased job completion
- Enhanced productivity
- Competitive stance that accompanies lower costs and improved margins
You don’t need full autonomy to enjoy these benefits. By adopting existing technology as it moves toward the holy grail, you set yourself up as a front runner in the quest. When full autonomy at last becomes available, you will have a jump on the competition. Your people will already be familiar with autonomous technology by virtue of their understanding of automated grade control, and they will be eager to claim the benefits that come with it.
Looking Ahead
In the march toward Stage 5 autonomy, remember, everyone is still learning. Haul trucks, compactors and other heavy equipment in mining and farming merely point the way to greater economies in construction and related industries. Where mundane and repetitive tasks are replaced by machines today, finesse work, such as grading, will likewise be managed using advanced technology.
“The ability to coordinate whole fleets from a remote site is coming soon,” said Flynn. “No one wants to work onsite in 100°F weather.”
Clark reports that Trimble is already adding features and functions that will minimize operator involvement in the grade control process to a point where the operator may be the only safety mechanism onboard.
“Once we figure out how to get the operator out of the machine altogether, it will be game over,” he said. “Jobsite safety and productivity will make a quantum leap, making construction in even the most hazardous locations practical.”
Trials are underway at research and development labs across the globe, in pilot projects designed to take semi-autonomous, human-directed operations to full autonomy with artificial intelligence and machine learning. As these pilots prove out, new options will become available, leading to cost reductions on the very technology designed to lower overall job costs for improve safety and profitability.
For early movers, renting autonomous equipment may be the economical way to sample its effectiveness without incurring steep, upfront costs. As well, retrofit kits for many existing machines will become available that preserve existing investments, allowing full autonomous operation without replacing manual operations altogether.
Keep Your Eyes on the Prize
While autonomy looms on the horizon today, automation is available, here and now. Automated grade control can produce huge returns on investment by way of improved grading accuracy, lower cost and enhanced productivity and safety.
“Autonomous control is already making inroads in unsafe conditions where a task is reliably repeatable,” said Hagemann. “Keep your eyes on the ‘secret squirrel’ stuff that’s happening now behind the curtains. You’ll be seeing more of it online, in showrooms and at tradeshows very soon.”