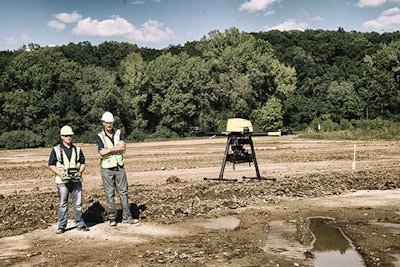
We’ve been working with a new piece of equipment on construction and quarry sites around the world. It doesn’t dig, push, load or haul. But it does fly – at speeds of up to 100 miles per hour – taking pictures and capturing data that can be used to improve safety, efficiency and profitability. Some call it a “drone.” At Caterpillar we call it a “UAV” (which stands for Unmanned Aerial Vehicle). No matter what you call the technology, now is a great time to learn more about it.
UAV Basics
A UAV is defined as an aircraft with no pilot on board. It can be remote-controlled from the ground or it can fly autonomously, guided by a pre-programmed flight plan. UAVs can be used for recreational or commercial purposes.
- Recreational users in the United States are required to register with the Federal Aviation Agency (FAA) at a cost of $5.
- Commercial use in the US is only legal if the user has obtained what’s called a Section 333 exemption from the FAA. It grants permission to make an income flying a certified, licensed UAV in the presence of a licensed pilot. Caterpillar has a Section 333 exemption.
In our business, contractors and aggregates producers are sending camera-equipped UAVs into the air to take dozens — if not hundreds or thousands — of images. The pictures, which are linked to GPS data, can be stitched together with special software, transforming them into a 2D or 3D site model.
UAVs in Action
Caterpillar has a small team of UAV experts whose focus is determining how the technology can be used to improve site safety, efficiency and profitability. Recently, we tested a fixed wing UAV in a U.S. quarry that produces between 800,000 and 1 million tons of aggregate per year. Our pilot flew three 25-minute missions over the 350-acre site, capturing thousands of images that were converted into a 3D model within 24 hours. Had the owner gathered the information manually, the process could have taken an extra week or more. Costs and safety risks would have been higher and the data would have been less accurate.
The company has used the data in a variety of ways.
- Calculating stockpile volume — quickly, safely and accurately — to ensure they’re paying the right amount of taxes and to help determine/measure production levels from the plant.
- Identified the next area of the site to be mined — are now planning where to put the haul road; its length, width and elevation; and how much material will be required to build it.
- Calculated how much overburden to be removed — at the next site and can now determine when to start stripping, what size fleet they’ll need and whether they should do the work themselves or hire a third party.
- Monitoring site activity near a creek on the property, giving them easy access to information they need to meet environmental regulations.
Plus, they’ve got a new aerial image of the site hanging in the office and interesting graphics for marketing communications.
This owner — like others we’ve worked with — started the process with a general plan for using the data, but ended up finding many more ways to leverage the technology and analytics.