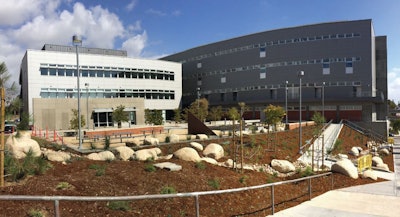
The challenge:
Design and construct a state-of-the-art science building at the San Diego City Community College with innovative methods and lean principles that allow the building to obtain LEED Silver Certification
The players:
Rudolph and Sletten
San Diego Community College District
The process:
For the construction of the $57.2 million, 98,000-square-foot, L-shaped science building at the San Diego City Community College the San Diego Community College District (SDCCD) sought out a contractor who would implement the most innovative methods available for construction of the high-tech science center. California-based general contractor, Rudolph and Sletten, led the construction of a new state-of-the-art science building with the help of Latista field management software solution. Designed to obtain a Leadership in Energy and Environmental Design (LEED) Silver Certification, the new science building will be four stories tall and house the Astronomy, Life Sciences and Physical Sciences programs at the San Diego City Community College.
The contractor wanted a QA/QC technology that could be used to implement its ‘Zero Punch List’ program and eliminate the error-prone and time-consuming traditional paper-based process. On a project this size, dealing with all the data entry could take one to two hours a day, said Jonathan Waltz, project manager at Rudolph and Sletten. “When we reviewed the Latista application, we recognized its capabilities as a cutting edge software tool that we could use to effectively implement our demanding Lean program. We wanted to provide our subcontractors with continuous up-to-date information on quality issues and prevent similar errors from re-occurring as we progressed through the project.”
All project stakeholders equally echoed the Rudolph and Sletten team’s sentiments and enthusiastically supported their efforts for an improved process. “Before Latista, I would have to hunt down a foreman for each trade when I saw something that needed to be fixed; then I would have to add it to a list. Then I would have to distribute the list to everyone with the updates,” said SDCCD project inspector Chris Thompson.
The Latista solution allowed the team to establish clear automated workflows, adding issues continuously throughout the project. It also allowed for capturing issues in the field with iPads and annotating with photos and marked-up drawings so subcontractors were clear on where and what needed to be fixed. Subcontractors were notified automatically when issues were created.
“The use of Latista web accessed through the Cloud along with the iPad app allowed us to pull technology into the field and underpin Rudolph and Sletten’s trend toward a paperless office,” Waltz said. “The technology provided up-to-date construction documents to my team, the inspector and the trade contractor’s field personnel, ultimately improving the owner’s perspective of us. They know that we’re delivering this building with zero defects and with zero issues at the end.”
Besides Rudolph and Sletten, owner representatives, project inspectors and subcontractors used the Latista system to communicate with each other about the project’s quality and status on a weekly basis. This allowed for complete transparency from the beginning.
Automating the quality management processes during construction facilitated the elimination of extensive corrective actions and cost for Rudolph and Sletten and the SDCCD owners. Specifically, the implementation of Latista increased the project team’s efficiency by purging double entries, time delays, vague cross-teams communications, and supplied the team with metrics they could use to analyze reoccurring issues, further improving their Zero Punch List program.
Implementation of Latista affectively reduced redundancy for all involved on the San Diego City Science Building project by as much as 25 percent. The team was able to save up to 10 hours per employee per week by automating their processes. “I’d say we saved about 1-2 hours a day and caught 99% of errors and corrected them before the punch,” Waltz said.