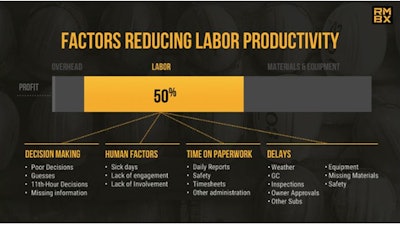
In 2007, Tim Berners-Lee, the inventor of the World Wide Web said, “It’s difficult to imagine the power that you’re going to have when so many different sorts of data are available.” He was right. Project management and ERP software has changed the construction industry, resulting in increased productivity, efficiency and return on investment.
In the same interview, Berners-Lee also said, “Most organizations are missing this ability to connect all the data together.”
Right again. Smart man.
What’s going on in the office is one thing but what’s going on in the field is another. Consider the foreman who, often with pencil and paper, will deliver information such as hours worked, delays and progress reports. By the time that information is processed, entered it into the system, and analyzed, issues that could have been addressed immediately are continuing to impact productivity. And because of the fluid nature of construction projects, the process repeats itself over and over again.
While our industry has been slower to adapt than some others, the writing is on the iPad. According to the World Economic Forum, in 10 years the construction industry will be almost entirely digitized, with an overall possible savings of $1.2 trillion globally due to increased efficiency and productivity. But today, the hurdle many who have digitized their office operations are facing is how to close that gap with what’s taking place in the field.
To truly improve labor productivity with data, the feedback loop has to be closed and data needs to be democratized. It can’t just sit on one person’s computer but needs to be widely disseminated so that the people who have the biggest opportunity to impact productivity in the moment - the workers on-site - can see the data and act on it.
Here are three ways to bridge the digital divide on the construction site.
Don’t confuse reporting with real time data
Construction firms rely heavily on Excel to create productivity reports. Reports are necessary, but firms shouldn’t expect them to make a big impact on their team’s productivity. Why? Because there are dozens of factors that can impact productivity. Especially when it comes to labor, which at 50% of project budgets, is the biggest lever that can impact whether a project is making or losing money on a day-to-day basis.
Instead of reports, firms need to start thinking about how to capture and combine qualitative and quantitative data from the jobsite. This means getting field notes from foremen and superintendents in the same system as accounting and financial data. The number of field collaboration tools available to contractors is growing every day, with more and more companies focused on field technology. Time cards, production quantities, materials, equipment and more are all potential field data sets that are rich with contextual insight into what went right (or wrong) on the jobsite.
Look or tools that are going to be easy for field workers to pick up and learn, and that integrates with existing ERP systems to ensure they are sticky enough to go the distance.
Avoid micromanaging
Let’s face it: no one likes the feeling of someone looking over their shoulder. Especially skilled craft workers who got into the trades because of the sense of accomplishment they get from seeing the physical and tangible results of a hard day of work.
Field technology has the risk of being perceived as a form of “big brother” on the jobsite if it’s not selected with the end user in mind. The key to flipping this perception is looking for technology that gives back. What if every foreman had their own view of budgeted versus actual hours available on their phone? What if they didn’t have to wait for a weekly report from a project manager to filter down to them? Closing the communication loop between the field and the home office means foremen are equipped to make better decisions faster. Imagine what that could do to boost project productivity.
Acquiring data is only the first step
For many firms looking to bridge the digital gap, starting at square one can be intimidating. Transforming disconnected and disordered field data into structured, well-defined pathways can feel like a big undertaking. And it is.
But the good news is that the benefits start showing up faster than one might imagine. While it may take a few years to see the full potential digitizing your field data has to offer, the immediate benefits of time saved from manual data entry, and improved morale are almost immediate. Field crews want to do their best work. They want to be productive. Equipping them with tools that empower them to play an active role in solving productivity challenges will absolutely serve as motivation to improve.
There’s an incredible treasure trove of productivity data waiting to be captured. Not back at the home office. Not off of the CFO’s Excel file but from the workers in the field. This field data is the key to dramatically increasing labor productivity as well as establishing benchmarks moving forward.
The rate of new construction technology is only going to increase. With more granular data sets being created and data quality increasing, the companies that institutionalize processes for bringing new technology to the field are going to help remove barriers to adoption with increased productivity and profit the result.
About Rhumbix
Rhumbix modernizes construction field operations, helping builders go paperless in the field and improving how they measure and manage labor productivity. Their Field Intelligence Platform is a cloud-based mobile workforce management solution that collects and digitizes data from previously paper-based workflows. Headquartered in San Francisco, California, Rhumbix was founded in 2014 by Navy veterans with deep experience in the construction industry. For more information visit: www.rhumbix.com