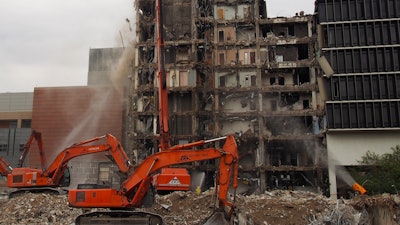
Information from this article was first published in Demolition Magazine and is being reused with permission from the National Demolition Association.
By Mike Lewis
On a brisk day in March, onlookers and local television station crews gathered a few blocks away to witness the implosion of the University of Colorado’s eight-story Biomedical Research Building. To mitigate fugitive dust emissions in the surrounding area, the operation was meticulously planned with dust control cannons spraying atomized mist at key locations during the event. Upon successful completion, National Demolition Association (NDA) member Colorado Cleanup Corporation (CCC) began the methodical 18-month demolition of the rest of the former University of Colorado Health Sciences Center, with the entire construction project scheduled to conclude by early 2020.
Located three miles southeast of the Denver core business district, the Hale neighborhood is comprised of single-family homes, townhomes and condos surrounding the 13 buildings making up the site. Ranging in age from the 1920s to the 1990s, the buildings and land were sold to 9th Avenue Land LLC, which chose Saunders Construction as the general contractor in charge of constructing the brand new mixed-use neighborhood called the “9th & Colorado Mixed-Use Redevelopment Project” (9th and Colorado).
Among the many reasons CCC was chosen for the task was the company’s history of completing complex large-scale demolition projects. Opened in 2002 and based in Englewood, Colorado, the company has quickly risen to become one of the demolition operators of choice for major contractors in Colorado, due in part to the company’s environmental approach.
“A project of this magnitude in a densely populated area requires the expertise to know when and where fugitive dust is produced,” says Chris Formanek, senior project manager at CCC. “But just knowing how it’s created isn’t enough. You need to know how to stop the dust before it leaves the project site.”
Breaking down a demolition project
Out of the 2.5 million square feet of land containing 13 structures, only one had steel construction, and the rest were poured-in-place concrete. Thus, CCC employed several different types of machinery, from standard excavators and large dump trucks to high-reach excavators with hydraulic demolition attachments.
Stretching high up and over debris piles to access hard-to-reach places, hydraulic concrete processors act like vice clamps, applying thousands of pounds per square inch of pressure to break apart thick reinforced concrete supports. The boom attachments — specially designed for this type of heavy-duty concrete work — cut the support structure into measured chunks, which are directed to specific safety zones, creating a more precise and efficient landing for debris and a safer, more predictable worksite. The concrete, rebar and ancillary material (drywall, ceiling tiles, etc.) that collected in the safety zone were loaded onto dump trucks and hauled to a separate location to be processed further.
The entire system required CCC to remain compliant with the strict regulations of allowable particulate emissions and control wastewater runoff as mandated by the state of Colorado and further restrictions specified by the municipal permit.
Demolition air quality regulations
Prior to the launch of the demolition project, CCC managers sat down with the Colorado Department of Public Health and Environment to go through requirements and expectations. One of the largest concerns for regulators was preventing dust from potentially leaving the site boundary.
When concrete is broken apart, the resulting dust may contain some silica, a crystalline particle common to minerals found in concrete. Unless the proper suppression method is used, silica particles can travel long distances on atmospheric currents.
Dust monitors were set up around the site perimeter to examine dust migration. Dust levels were measured entering and leaving the site to determine the amount of fugitive emissions. An independent company contracted by 9th Avenue Land then assessed particle levels collected from the air by the dust monitoring machines.
Further, CCC outfitted workers assigned to specific tasks with personal dust monitors, worn throughout their eight-hour shifts for three consecutive days. During these “Negative Exposure Assessments,” the dust monitors collected and measured levels of respirable PM10 (particulate matter that is 10 microns in diameter or smaller). A micron (µm) is roughly equal to 0.00005 inches. For perspective, a cross section of the average human hair is 50-75 µm in diameter (0.0025-0.00375 inches), illustrating that the most hazardous dust particles are the ones too small to see. Respirable PM10 can avoid the body’s natural barriers and penetrate deep into the lungs, potentially causing long-term health issues.
Fugitive dust emissions from demolition
“The two areas in the process that create the most dust are where the concrete breaks and the point of impact with the ground,” Formanek says. “Large and small chunks of debris would fall into the safety zone, which kicked up a lot of dust. Also, every time the processor uses hydraulic pressure to break the concrete, it creates a plume of dust. This usually happens high up, so the particles can travel pretty far. We needed a method that effectively controlled dust in both of these areas.”
The most common method of dust suppression used in demolition projects across the industry involves manually controlled and/or boom-attached hoses spraying copious amounts of pressurized water over an area. To address fugitive dust emissions in the safety zone caused by falling debris, workers holding fire hoses connected to municipal hydrants would wet the surface of the impact area, both on the safety zone outside of the building and the inner building, as some debris can fall inward. Additionally, excavators disrupted the debris as they loaded the dump trucks, causing more dust.
On the extended excavator boom, hoses were attached above the hydraulic attachments. Controlled by the operator, the hose would spray on the general area where the processor was breaking the concrete in order to suppress some of the resulting dust. But operators found that it was not effective at pulling smaller particles out of the air.
CCC knew that these methods would not adequately stop the migration of dust at the level it was likely to be produced, so managers employed both traditional hose methods and modern atomized dust suppression. “The hoses were all right for ground suppression, but they just weren’t good at controlling airborne dust,” Formanek says. “We needed something more.”
Addressing dust particle by particle
Having seen DustBoss atomized dust suppression in trade magazines and at industry conferences, project leaders contacted the manufacturer, BossTek, for more information. “We looked at similar technology on the market, but we chose to test the DustBoss DB-60 because it was trailer-mounted, heavy-duty and more versatile than other models,” Formanek says.
Dust particles below the size of 200 µm remain airborne and can be carried long distances on air currents, even without the assistance of a strong wind. Using a specialized nozzle and industrial fan configuration, atomized dust suppression machines introduce millions of tiny droplets roughly 50-200 µm in diameter into a large area, which travel on air currents with the dust particles, collide with them and drag them to the ground.
The size of the droplet is important, because hoses and water cannons common to demolition projects typically produce droplets between 200 µm and 10,000 µm in size, which are large enough to create a phenomenon known as the “slipstream effect.” A slipstream is created when a mass moves swiftly through the air. Like the air moving around an airplane wing and keeping the craft aloft, a slipstream also travels around a large falling water droplet. Smaller dust particles get caught in this slipstream and are directed away from the droplet, remaining airborne. Due to the small size, atomized mist droplets produce virtually no slipstream and linger in the air much longer, increasing the chance of a collision with an airborne dust particle.
Either mounted on a roadworthy mobile carriage or a heavy-duty metal skid, the DB-60 has a specialized open-ended barrel design with a powerful 25-horsepower industrial fan on one side and a misting ring on the other. A 10 -horsepower booster pump sends pressurized water through a circular manifold fitted with atomizing nozzles. The nozzles fracture the water into an engineered mist that throws millions of tiny droplets in a 200-foot-long (60 m) cone.
The mist can be directed at a specific activity or fanned out over a large area using the 359-degree oscillator, which allows the machine to cover approximately 125,000 square feet in calm conditions. Powered by a 60-kilowatt diesel generator set, the machine’s functions are controlled either via digital touch screen display mounted on the unit, by remote handheld device or by PLC (Programmable Logic Control). This makes it easy to be adjusted by workers on the ground or even by excavator operators.
CCC project managers discovered that atomized mist was more effective against dust than standard methods. “It created a big curtain around the zone where we directed it, which pulled the dust right out of the air,” Formanek says. “It covers a large area and does a great job. We especially like how little water it uses.”
Controlling wastewater runoff
Hoses attached to fire hydrants deliver around 100 gallons per minute (gpm) of water, which can create an excessive amount of runoff. To comply with federal and state wastewater and storm water regulations, CCC site managers set up a filtration system in storm drains and a temporary sediment basin. The filtration system stopped any large debris from entering into the city sewer, while the sediment basin controlled the majority of the collected water, allowing surface dust and fines carried off by rainwater and dust suppression to settle. However, when using hoses that discharge a high volume of water, not all pooling can be controlled, resulting in standing water in some areas that can cause a potential workplace hazard.
The DB-60 uses only 12 gpm to 26.7 gpm, depending on the water source, however, CCC had access to municipal hydrants, which provided more volume and pressure. Using a 1.5-inch cam-and-groove quick disconnect female coupling for the hose, the unit only needs 10 psi delivered to the booster pump. The low psi requirement allows the machine to be far away from the source, while still providing effective airborne dust control and surface suppression.
“The water from the hose pours into one small spot and causes a lot of runoff and pooling,” Formanek says. “The mist from the DustBoss settles over a very wide area, so the ground more easily absorbs it. Our water bill certainly shows the difference.”
Results
After the first week of testing on the site, project leaders saw how well atomized mist controlled dust and decided to order another DB-60 unit. With multiple buildings being demolished at once, the two units have been shared across the site and placed at critical areas using only a pickup truck or small ground vehicle to move them.
During the demolition project, the company received no complaints about fugitive dust caused by standard demolition operations. No dust migration was observed outside of the site boundary, and readings from both the perimeter monitoring machines and from the workers’ personal dust monitors registered below required thresholds throughout the project.