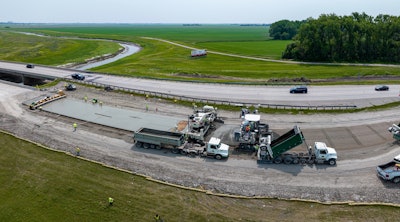
We’re nearing the halfway point of an election year, and roadbuilders, like many others in the construction world, are weathering changes. Despite increased material and labor costs, project managers employ solutions to increase profit margins during this paving season.
The Association of Equipment Manufacturers reports an increase in both asphalt and concrete prices and unstable diesel and oil prices for the rest of the calendar year. Meanwhile, many project managers are still looking for the right person for the job during the continued labor shortage. Project managers are left to budget higher salaries for roller operators, screed operators and laborers. Besides the business cost increases, several state or federal projects—as part of the Infrastructure and Investment Acts (IIJA)—require efforts to improve the sustainability of their project bids. All these factors have forced equipment professionals, project managers and original equipment manufacturers (OEMs) to identify what will pave the way to long-lasting roads without breaking the bank. The answer for most? Eliminating Rework.
Several times in recent years, when John Deere’s leadership team has talked about the company’s effort to help reduce emissions, they’ve highlighted their key tactic—reducing rework. After all, not having to run your equipment to complete a job a second time means, well, less equipment running and lower emissions. Construction rework is any unplanned work required as a direct result of missteps.
For example, if a slipform paver width must be reset because the mix density is off or a roller makes too many passes or not enough, the resurfaced road will not have the correct density to meet its specs. Without achieving the exact smoothness, grade and thickness specified by an engineer, the road’s likelihood of longevity is low.
Unplanned rework requires additional resources, whether materials, labor or fuel. During this paving season, a focus on the bottom line paired with high demand to pave roads sustainably has led many project managers to upgrade their paving tools.
To empower operators to safeguard against rework, OEMs like Topcon and Wirtgen offer different technologies and equipment to provide entire paving teams with a better view of the overall process. From the simple extension of an operator's platforms to going stringless with Wirtgen’s AutoPilot 2.0 control system or highway-speed road scans to create 3D models, project managers invest in tools, so their team has a windshield view during each paving pass. Check out ways roadbuilding teams are precisely paving roads on time and on budget with equipment and technology.
Choose Pavers With Versatility
During the last two years, OEMs have released slipform or offset pavers with more width versatility. With this ability to set the width to each road's specific needs, OEMs have also extended the operator's platform. For example, operators say Wirtgen's SP15i platform allows them to see the feeding system, transfer hopper and inside of the consolidation compartment of the mold. This expanded view and width allow operators to set the paver for each project accurately and better see its work.
The view from above before slipfrom paving.RDO Equipment Co.
Claunch said that his team is more than happy with their SP15i compact slipform paver and will still use it on future paving sites. However, Claunch decided that the latest model’s benefits could make a difference in the coming season.
He said both models have good maneuverability, tight turning angles and flexibility. However, the SP25i can pave roads up to 6 feet, 7 inches thick, and concrete surface widths up to 12 feet. His team will be paving in different cities this year, and he wants the ability to pave to the project's specs based on that region's environmental factors, like average temperature, moisture and frost levels.
Where Did All the Strings Go?
This season is the watershed moment: stringless paving is no longer the anomaly but is becoming the norm on many jobsites. Project managers say stringless paving dramatically reduces hazards and improves safety. In previous years, roadbuilders would stake out strings so the paver would follow a straight line and compact the concrete to the correct grade and width. Today, sensors and GPS technology precisely guide paving equipment without needing physical string markers.Dennis Howard at the North Dakota concrete paving site with Northern Improvement Company's President Greg McCormick and Foreman Ryan Ziegler.RDO Equipment Co.
Northern Improvement Company—a North-Dakota-based heavy, highway, and municipal construction company—has embraced stringless paving. Greg McCormick, northern improvement president, said that the company started onboarding the stringless paving system a few years ago.
On a North Dakota Department of Transportation project, McCormick said stringless paving significantly improved safety as the team reconstructed 6 miles of Interstate 94. Without strings, the team reduced hazards for laborers and improved the efficiency of haul trucks to deliver concrete, so the WPS 102i concrete placer continuously operated.
Scan Roads at Highway Speeds
When roadbuilders must ensure that their team achieves the right compaction rate as they quickly resurface a road, they turn to intelligent paving systems. Last year, Topcon introduced an intelligent paving system, a 3D scanning, modeling and automated machine guidance system (AMG) to capture a detailed road model using a vehicle-mounted scanner capable of collecting data in live traffic at typical highway speeds.
Operators on Hamm rollers ensure compact and smooth roads.RDO Equipment Co.
White and PRS team members entered the engineer’s 3D model which included the highway’s optimized smoothness, grade and thickness for the environment, into five milling machines. Each milling machine was outfitted with AMG, a form of automated machine control. The five milling machines simultaneously milled the road’s old asphalt into uniform material so it could be repaved in one pass with precision. In the end, PRS completed the project in a single weekend with a 70% road smoothness increase from its previous state.
Early Adoption
Roadbuilding teams will likely be early adopters of equipment and technology to meet the increased demand to build durable roads without increasing material or labor costs. By focusing on rework elimination, project managers have partnered with equipment experts to empower their operators with a holistic view of the project.
With simple equipment upgrades to complex technological advances in machine control automation, project managers and operators dramatically decrease production time on machines and emissions to pave in one pass. Accuracy is ensured through each team’s dedication to paving the road toward the future.