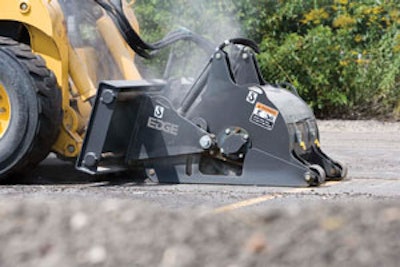
An attachment is only as strong as the host machine that provides its hydraulic power," notes Kelly Guthrie, marketing, Coneqtec/Universal. Consequently, cold planer attachments and skid-steer loaders must be properly matched to ensure optimum performance.
It's important not to underestimate the hydraulic demands that will be placed on the carrier. "Case does not recommend using a planer that is oversized for the base unit," says Bill Harris, attachments engineer, CNH. "Some skid-steer manufacturers tend to be optimistic regarding the maximum hydraulic output, and some planer manufacturers tend to be optimistic regarding minimum requirements. If the loader just makes the planer's recommended requirements, the user will likely be disappointed with performance."
Also consider engine speed. "Available horsepower is critical to production," Harris states. "There needs to be enough engine horsepower left for traction."
According to Justin Odegaard, attachment product specialist, Bobcat, "The machine needs to be run at high idle, or throttle open completely, in order to achieve maximum horsepower. Some contractors will run at three-quarters of maximum to save fuel." Yet, this can prove counterproductive. "The engine actually has to work harder to achieve the performance required for the planer attachment."
He adds, "Planers are one attachment where it's hard to have too much power. More power will typically make production increase."
Size/power ratio
As planers go up in size, they usually require a carrier with both higher engine and hydraulic horsepower. "The requirement for machine size/power will be related directly to the job at hand," Odegaard points out. "The wider a planer gets and the deeper it goes, the [higher horsepower] it needs to plane effectively."
"The general rule of thumb is 2 hydraulic horsepower (hhp) for every 1-in. width of drum," says Guthrie. "For example, for a 24-in. planer to be productive, it will require around 48 hhp. Otherwise, there will not be enough power delivered to the attachment for it to run effectively when milling more than 1/2 in."
Gallons per minute (gpm) taken alone can be misleading, he cautions. "The power needed to effectively run a particular attachment is determined by the hydraulic horsepower," he states. This is calculated by multiplying the gpm by the psi, then dividing by 1,714. To account for system inefficiencies, 10% is then subtracted to estimate net hhp.
For example, a loader rated at 40 gpm at 3,000 psi would have 70 gross hhp. Subtract the 10% for system inefficiencies and you have 63 net hhp. A second loader rated at 34 gpm at 4,500 psi would have 89 gross hhp. Minus 10% leaves you with 80.1 net hhp. "That's a lot more power with less gpm," Guthrie comments.
Of course there are going to be slight differences in hydraulic system efficiencies between the various units on the market. "Hydraulic systems are set up in many different ways for loaders and planers," says Odegaard. Some systems are able to better put the power to the ground."
Using math to calculate hydraulic horsepower produces a theoretical number. "As the hydraulic fluid moves through hoses and valves in the system, it loses efficiency," says Odegaard. "Bobcat has found in its M-Series loaders that significant actual gains can be achieved with a more efficient system. M-Series loaders with less 'theoretical' hydraulic horsepower will actually outperform other models that have more theoretical hydraulic horsepower."
Balance is important when it comes to hydraulic components. "The planer also needs to have hydraulic components that match the carrier's flow and pressure," says Odegaard. "Planers need to have a balance between speed and torque. A planer that is set up for a high flow, lower pressure will perform better on a machine that has those specifications. Putting the same planer on a machine with higher pressure and lower flow may see decreased performance."
When ordering a new planer, the systems are matched by the attachment manufacturer. "Planers are configured with different motors to match the skid steer hydraulics at the time of ordering," says Guthrie. It's not a situation where one planer will work with one kind of loader and another planer will work for another kind of loader. "If buying used at auction, look at this before purchasing."
Weight influences depth
In addition, the loader must be able to effectively lift the attachment. "You want the hydraulic flow and then the lifting capacity," says Ron Peters, product manager, CEAttachments. "These are heavier attachments, so you need a machine that can lift it off the ground and move it around."
Generally, the heavier the planer the better, since it will reduce bounce and keep the attachment in the cut. "A pivoting or self-centering planer head keeps all of the depth control surfaces in contact with the ground. Individual depth control for left and right side maintains depth control surface contact when making adjacent, step and taper cuts," says Harris.
Guthrie adds, "A center pivot puts the skid steer forces directly to the drum for unmatched stability."
Guide wheels may also prove beneficial. "Our cold planer has wheels on it," says Peters. "The weight is distributed on the wheels and you can drive forward fairly easily. Some manufacturers have skid shoes on them and it causes a lot of friction when you put a lot of down pressure on it. The result is you cannot put a lot of down pressure on the attachment and you are going to bounce."
Don't force it
How you operate the carrier and attachment further influences performance.
"A comfortable, steady operating speed should be selected, and the base unit should not be crowded so that the auxiliary hydraulics are constantly spiking relief," advises Harris. "Also, when milling near the max depth of the planer, it's generally more productive to make two or three shallow passes rather than one full-depth pass, especially in tough material."
The deeper you run the cold planer, the slower you have to go. "If you have to take out 6 in. of asphalt, you are probably better off doing two passes to get to your 6 in. rather than doing it in one crack, because you are able to drive a lot faster and your cold planer will perform a lot better," says Peters. "The deeper you go, you have to drive slower. If you drive too fast, your drum speed will start slowing down and you have to back off a little bit."
Drum type and bit placement
"One of the most important factors in determining performance is drum type," says Guthrie. "The open drum provides much less re-milling of asphalt and thus increases productivity.
"Re-milling occurs at depths below 1 in., when the previously milled asphalt is trapped and milled again," he explains. "This results is less desirable, finely milled asphalt, more dust and much less productivity. More energy is consumed if the material is finely ground vs. coarsely ground. Fine grading requires the continuous fracturing of the aggregate in the asphalt vs. removing the aggregate unfractured in the shavings."
There is no industry standard for bit placement and spacing. "Planer manufacturers have different thoughts on bit placement and spacing," says Odegaard. "A drum with larger spacing between the teeth will leave a rougher surface but have higher production. For this reason, it's important to evaluate a planer on the job to ensure the quality of the cut meets the specifications for the job."
Ensure Rotation to Keep Pics at their Peak
Given the current focus on road repair/restoration, it's more crucial than ever to maintain cold planer attachments to reduce downtime and ensure projects are completed in a timely, cost-effective manner. Perhaps the most important maintenance consideration is to ensure the pics (bits) don't seize up during use.
"The first thing I always tell people is to inspect the pics on the cold planer frequently," says Peters. "You want to make sure the pics are free so they can rotate."
Harris agrees noting, "Pics must rotate freely for maximum planing efficiency and pic longevity."
Pics consist of a tip (or head) and a shank. "The shank slides into a pic block or holder," explains Guthrie. "Often, there is a collar on the shank that allows it to spin in the block. In use, the pic rotates in the block when it makes contact with the road surface. This allows the pic to self sharpen and not grind down to a dull stump or break off. If the area [around the shank] becomes lodged with dirt and spoil, it cannot rotate."
The rotation allows the pics to maintain their point, similar to how a pencil sharpener keeps a pencil sharp, says Peters. "If they are sharp, they bite the asphalt and you will get more performance out of the cold planer," he states. "If the pic stops rotating, a flat spot will develop on the pic. Then it will take more horsepower to slice away, and eventually you are just going to wear your pic out. That is the most important thing that people overlook. If it stops turning, it will be damaged and eventually it will have to be replaced."
"Replacing a full set of pics can cost hundreds of dollars each time," Guthrie adds. "Keeping the pic areas clean and getting two to four more weeks of use makes good sense."
In addition to providing dust control, water kits can assist in extending pic life. "Water spray kits help keep the pics clean and free to rotate in their holders," says Guthrie.
Peters advises cleaning and lubricating the pics every five hours or daily, especially when grinding in asphalt. "As you are using the cold planer, the teeth will warm up and start to melt some of the tar from the asphalt," he notes. "Then, when it cools down, it will gum up the teeth and they will not rotate." Pics are usually lubricated with a product similar to WD-40. "You want something that will attack the asphalt that builds up around the teeth."
Also periodically open the access panel on the cold planer to check pic condition. "The points of the teeth will have carbide on them," says Peters. "You will be able to see if that carbide is worn away. Once that happens, they will start wearing real fast. They will mushroom over.
"If you are an experienced operator and you sit in the seat, you will be able to tell pretty quickly when the teeth are worn out," he continues. "It just will not perform like it used to."
Using the right pics for the application can influence performance and longevity, as well. "Manufacturers typically offer multiple types of bits for their planers," says Odegaard. "Some contractors do most or all of their work on asphalt and others on concrete. If that's the case, discuss what type of work you will be doing with the dealer and he may be able to offer bits that will perform better in one place or the other."