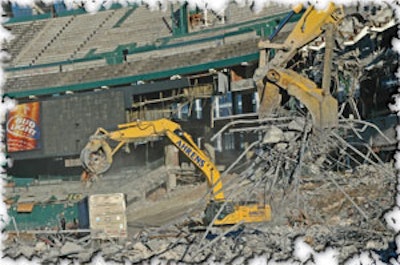
Many attachments allow your excavator to efficiently handle irregular-shaped objects, including thumbs and grapples. The first step is to assess whether you really need a grapple or if you could be just as productive with a bucket and thumb.
The bucket/thumb combination can handle most tasks. "If you handle a lot of different material over a wide range of applications, a bucket with a thumb will do the job eight times out of 10," says Bo Pratt, marketing manager, Rockland Mfg.
So the choice really boils down to the efficiency in your particular operation. "The contractor's grapple will typically be much more productive in most applications (demolition, rock handling, scrap handling, land clearing, etc.)," says Uwe Kausch, product line manager, Stanley LaBounty. "You should use a grapple if a good part of your business is anything other than dirt. For demolition and serious material handling, the grapple is the way to go."
Pratt agrees, adding, "The productivity is going to be much better with a grapple if you are handling the same material over and over and you don't have to dig with your machine." He attributes this to the ability of a grapple to grab more material in a pass than with the bucket/thumb combination.
Grapples also tend to work better on irregular objects. "Some items grapples can lift easily are hard pressed to fit between a bucket and thumb combo," says Tracy Black, operations manager, Kenco. "In many situations, grapples are used to allow soil and small rocks to fall through to the ground. This cuts down on the amount of material moved, thus saving time and money. Buckets tend to retain more unwanted material. Grapples offer more precise picking options, as well."
"However, if a contractor is foremost a dirt contractor and only occasionally needs to handle material or do smaller demolition jobs, then a bucket/thumb combination may be better suited to him," says Kausch. "The bucket/thumb is also better suited if he is trenching and needs to remove rocks from a trench and other applications where the material is very fine."
Selecting a grapple
After you have determined that a grapple is the best choice, you must choose the right one for your application. The simplest configuration is the contractor's grapple. Contractor's grapples feature a stationary jaw and an upper jaw that operates off the bucket cylinder. "It is very simple to use and does not require any additional hydraulics," says Kausch.
"The fewer hydraulic functions you have on a grapple, the easier it will be to use and the more reliable the grapple will be," notes Pratt. The end result is the contractor's grapple costs a lot less and there is less maintenance. "It has been our experience that if a contractor is handling the same material over and over, then a fixed-jaw grapple will meet his or her needs." However, if the application demands precise material handling, a rotating grapple may be the better choice.
Rotating grapples require auxiliary hydraulic circuits. "The advantage with the rotating grapple is that they are better suited for applications where precise picking, sorting and placement are necessary," says Kausch. "For example, in applications where timbers or structural steel is to be salvaged, the rotational ability allows the operator to get a better handle on the piece. It also excels in applications such as rock rip-rapping, and it can do a more efficient job in loading trucks. (The operator doesn't need to be at a 90° angle)."
Less time is spent maneuvering the excavator. "The operator can position the grapple without moving the machine," says Black. "In the right job situation, these grapples can outperform any fixed grapple. The down side is with hydraulics and rotators the price goes up. The contractor must weigh the initial cost vs. the expected gain."
Dual-acting cylinders also provide the grapple with extra dexterity. Stanley LaBounty has designed a link to synchronize the opening and closing of the tines. "We have found this to be advantageous with most applications, and it makes it easier for the operator," says Kausch.
Kenco offers grapples with a standard stay arm or optional hydraulic cylinder. "The hydraulic version allows the operator to close and open the grapple quicker," says Black. "Also, if the operator needs to pick an object elevated above the end of the stick, the hydraulic cylinder can move the lower jaw assembly up further than the fixed stay arm models."
The use of a quick coupler also influences grapple selection. "If a customer has the intention of using a coupler in the future, they should purchase this at the same time with the grapple," says Black. "Grapples should be set up to work with a coupler at the factory. It is quite expensive to retrofit grapples at a later date. Direct pin-on grapples typically do not work well on couplers."
Build quality varies
You also need to look at the strength and durability built into the grapple. "Beware when you come across two similar-sized grapples and one is priced significantly higher than the other. The lower priced unit is most likely not made of the same steel or built to the same tolerances," says Pratt. "There are a lot of different steels available. The differences in wear life and reliability that come from using good steel are tremendous. The materials that are in them is usually what controls the price."
The higher grade steels wear much longer and require less maintenance. "As a general rule, any steel that is above 400 Brinnell hardness works best when handling rugged and abrasive material," says Pratt. "We recommend hardened plate over hardsurfacing softer plate to the majority of our clients."
"All of our grapples are made from a high-strength steel (130,000-lb. yield). The grapple frames employ a box tined design with internal reinforcement plates," says Kausch of Stanley LaBounty's grapple line. He adds that each tine can withstand the full excavator breakout force. "A high-strength torque tube is employed on both grapple frames to distribute stress loads and prevent the grapple from twisting when uneven loads are handled."
But keep in mind that while you want a durable attachment, weight must also be considered. The weight of the grapple plus the material that it lifts must not exceed the rated lifting capacity of the machine.
Consider tine configurations
There are many different tine configurations available. "Typically, if a customer is working with smaller debris, a larger number of tines is the way to go," says Black. "Demolition grapples usually have a two-over-three tine configuration for picking larger items. Brush or debris grapples are normally a three-over-four tine design. The more contact area the grapple applies to the load, the more the clamping force will decrease."
Some contractors opt for maximum durability over volume. "The two-tine upper jaw, three-tine lower jaw is the most popular and strongest design," says Kausch. "It can be used in all types of applications where you see contractor's grapples being used.
However, we also offer a four into five design which is used primarily in trash-handling applications. The four into five tine grapple is a bit wider and better suited for this application, but the two into three tine grapple will work fine in this application, as well."
Pratt agrees that a two-over-three tine heavy-duty grapple can be applied universally to most applications. They are generally a little heavier and don't hold quite as much as the lighter-duty four-over-five tine grapple. But the overall difference in productivity when handling lighter materials is not much. "Our experience has been the tines really don't deliver that much difference in productivity," he adds.
The majority of grapples that Rockland Mfg. sells are the heavy-duty two-over-three tine configuration because many contractors want one grapple that will handle a wide variety of tasks. "The majority of the grapples we sell are heavy duty," say Pratt. "It is better to have a slightly wider grapple for trash handling and other light material-handling applications. But the difference is not going to be that significant for contractors that want to use one grapple for a variety of tasks."
There are also three-over-four tine designs that fall in between the heavy-duty two-over-three and light-duty four-over-five tine designs.
The overall frame size will impact visibility. "Obviously, the smaller the grapple frames (width and height), the better the visibility," says Kausch. "However, you gain more capacity with larger frames."
Pratt adds, "When you are talking about visibility, the narrower the grapple, the better visibility the operator is going to have. However, the grapple will handle less per pass."
The intended purpose of a particular grapple will also affect operator visibility. "Any brush grapple will offer better visibility," says Black. "The tines are smaller, which creates larger openings to see through. Demolition grapples have smaller box tines that are wide and deep. These are much more durable, but visibility is sacrificed."
Installation issues
Some grapples are designed to stay as a single unit when unpinned from the excavator, while other grapples consist of two halves that come apart when unpinned from the machine. "On a lot of the cheaper grapples out there, when you unpin the grapple from the machine, the halves fall apart," says Pratt. "It is very time consuming to line both sides up — especially if the contractor has a large grapple — and pin the halves back together. It's going to be a lot easier to pin up to your machine if the brackets are on one side of the grapple."
Rockland places the mounting brackets on the half of the shell that curls. This keeps the grapple halves together as the unit is unpinned.
LaBounty has also engineered a design that keeps the grapple halves mated as the attachment is unpinned. "Our pivot uses a spool design that goes through both grapple halves. This serves to keep the grapple halves together when the pin is removed and also to better distribute stress loads," says Kausch. "The main pin slides through the spools and the upper jaw pivots on the spool vs. the pin, significantly reducing pin wear and increasing overall life of the pin components."
Kenco takes yet another approach. "We build two independent hinge points on either side of the lugging," says Black. "This allows for the grapple halves to stay attached. And by keeping the hinge pins in line with the stick pin there is no performance loss."
Placement of the hinges in grapple design is critical. "Hinges can change the opening and closing movements," Black notes. Without good hinge placement, your grapple may not open wide enough, which cuts down the payload.