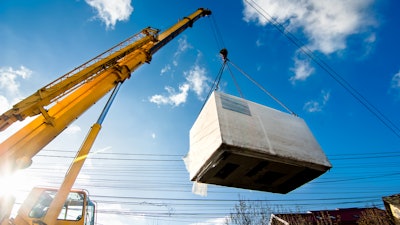
To the untrained eye, cranes do all the hard labor as they lift substantial amounts of material throughout the daily routine. However, if you look closer, you will see the real heavy lifters — the people behind the cranes.
Before crane operators can even operate a machine, they must go through a rigorous certification process that teaches must-know knowledge, industry best practices and crucial skills. However, before a crane operator can be classified as certified, they must also receive specific training for operating a crane, according to the Final Rule passed by the Occupational Safety and Health Administration (OSHA).
This training process is specifically dedicated to the machine model that the worker will be operating. However, even the most trained personnel must be aware of extenuating circumstances while operating a crane. Simply put, overlooking a small factor could mean a fatal injury.
According to the U.S. Bureau of Labor Statistics, the Census of Fatal Occupational Injuries reported 297 crane-related deaths over a seven-year period. These deaths could have been avoided if certain factors were monitored closer.
Here is a list of seven factors crane operators should be aware of prior to and during crane operation:
1. Inspect equipment and the load for any signs of wear
Even before hopping into the crane’s operating cab, the machine and its load must be checked for any visible signs of wear and tear. For example, chains links are one of the most prominent places for deterioration over a period of time due to the force it withstands.
In addition, cranes, both inner and outer, must be inspected for rust and corrosion. This factor should be addressed frequently to avoid replacing the crane as a whole.
Other important aspects to check:
- Stabilizers, sliders and outriggers
- Main boom
- Lattice boom extensions
- Safety Devices
- Jib
For a more comprehensive list for preventative expectation, please reference the Crane Preventive Maintenance Checklist.
If any parts are found to be in less-than-optimal condition, the damaged crane parts must be taken out of use, as well as repaired or replaced. By checking this prior to operating the crane, accidents from faulty parts can be avoided.
2. Ensuring ground workers are clear of operation
Once the crane has been checked and has the ‘green-light,’ crane operators can begin operating the machine. However, they must check their surroundings and ensure all jobsite personnel are outside of the crane’s operational area.
This is an issue that needs to be readdressed often to ensure that all worksite personnel are actively conscious of keeping a safe distance. In the same study by the U.S. Bureau of Labor Statistics, more than half of the injuries reported involved a worker being struck by an object or piece of equipment.
If both the crane operators and worksite personnel are consciously engaged in avoiding accidents of this nature, these types of accidents can be reduced, in not eliminated entirely.
3. Watch out for unsecure loads
In addition to being mindful of workers in the area of crane operation, loads should be continually monitored. In the past, there have been instances where loads were not entirely secure leading to construction mishaps. Since loads are usually extremely heavy, a slip can cause extreme damage, including fatality.
To be safe, loads should be continuously monitored, as well as slings and attachments. It is always better to double check a secure load than to miss an unsecure load. In this case, cautiousness pays off.
Unsecure loads come from three reasons:
- Equipment wear (See Step #1)
- Improper loading
- Mechanical malfunctions
4. Crane Hand Signals
On the job, crane operators have to recognize hand signals that direct them to move the boom and load — raise, lower and shift horizontally. In some cases, hand signals will direct the crane operator to stop the crane in action.
Watch this video for some advanced hand signals for crane signals.
Hand signals cover:
- Stop signals
- Boom and load signals
- Travel signals
It is important that the crane operator not only knows the hand signals, but that they are always on the lookout for them. If a crane operator misses a signal, like an emergency stop, it could be detrimental for the project, equipment and workers.
5. Watch out for electrical hazards, scaffolding and overhanging branches
As many know, avoiding electrical hazards in the field is an extremely important factor. Unfortunately, watching out for them is not always the easiest job, as powerlines and other hazards are often not in plain sight.
Contact with powerlines are one of the most frequent hazards on a job site, accounting for 50 percent of crane accidents, says OSHA. Hazards that come along with powerlines include extremely high voltage, burns and falls caused by electrocution.
Other electrical hazards come from a missing path to the ground, equipment misuse, extension and flexible cord misuse, and lack of ground-fault protection.
According to OSHA, there are multiple ways to avoid electrical hazards, some include:
- Looking for overhead powerlines and buried powerline indicators
- Contacting utilities to find buried powerlines
- Marking all electrical hazards and keeping a watchful eye out for markers
- Maintaining 10 feet of distance from overhead powerlines
- De-energizing and grounding powerlines, power supply systems, electrical circuits and electrical equipment
- Using ground fault circuit interpreters
While looking for electrical powerlines, also survey the area for other potential hazards, including but not limited to scaffolding and overhanging branches. Unlike powerlines, there is no electrical current, however encountering these objects can still pose a threat to the safety of the crew, equipment and jobsite.
6. Be mindful of the weather
Unlike jobs located indoors, crane operators, supervisors and managers need to be aware of outdoor conditions. These conditions, although may not cause a simple pedestrian any concern, may be detrimental to a crane’s operation.
Because of the height of some cranes, heavy rain and high winds can cause accidents. This is something that contractors need to be aware of before starting to schedule for a project. By alotting the extra time prior to, it will allow for safe decisions based on unforeseen weather delays.
In instances of high winds, it is best to stay on the cautionary side of things to avoid a catastrophe of tipped equipment or other dangerous consequences.
Watch Lifting in Bad Weather Conditions | Sims Crane Minute for an in-depth idea of the impact of weather on crane operation.
7. Watch out for unstable ground and obstacles
When setting up equipment, be mindful of the ground you will be working on. It is important to notice these factors early and avoid setting up a crane on unsteady ground — avoiding worry and mistakes down the road.
Other factors to make note of are ditches and drop-offs on the job-site. By surveying the area and noting things prior to the start of the project will allow you to create a game plan for safe crane operation. Operators and job-site workers can mark danger zones for reference throughout the project.
As aforementioned, being mindful of the weather is extremely important. With heavy rains, runoff and other environmental factors, comes ground wear and tear. What seems like stable ground one day, can be unstable the next due to these conditions. For example, rain can dampen the ground making equipment sink in certain areas, causing instability.