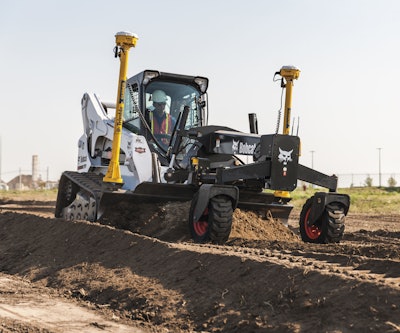
The integration of hydraulic systems and recent electronic engine systems with software enables features that simplify attachment operation and reduce operator fatigue. Electrohydraulic (EH) controls were introduced on skid-steer and compact track loaders almost 15 years ago, and have become popular on larger models over the past five years. They are also gaining popularity on mid-size machines.
Three primary methods control hydraulic valves on skid-steer and compact track loaders — manual, pilot and electric. Each has its place depending upon the application and operator preference. Pilot controls were the first advancement over manual controls, reducing the effort needed to manually open and close hydraulic valves. But expanding the actual functionality of pilot controls meant adding additional hydraulic lines or ports to the hydraulic valve.
With EH controls, joysticks are connected to an electronic control unit (ECU) by wires. The ECU is then wired to an actuator on the hydraulic valve.
“Electronic controls allow us to add features and have variable settings that may not be available with hydraulic pilot controls,” says Mike Fitzgerald, product specialist, Bobcat. “When you get electronic control systems adjusted properly, they can accommodate the operator’s preferences better and meet the needs of individual jobsite requirements.”
Both EH and pilot controls remain popular. “Both styles allow operators to perform their work very well. But EH controls really show their value when working in varied applications where the operators want a different feel from their skid steer as they move from task to task,” says Scott McElroy, SSL/CTL training manager, Case Construction Equipment.
Software Drives Flexibility
Software is the key enabler. “Dynamic mapping of input to valve output characteristics allows the operator to change how the machine responds to a given command,” says Chris Schottler, engineering manager, Advanced Technology, Eaton. “EH controls enable capabilities such as remote operation and adjusting the sensitivity of the machine based on the work being performed. EH can also tie in operator input commands with other machine information, including engine speed and power demands, to make smarter decisions about what the machine needs to be doing.”
One drawback is EH controls command a price premium. “Though the gap is closing, currently EH controls are still a premium in our industry when looking at up-front costs,” says Nadine Powell, global strategy and planning manager, Eaton.
However, there are several advantages to EH systems that help offset those costs. “For example, installation is faster and less complex. Pilot-operated controls require each joystick to have six hoses, which can be a challenge to route in a compact machine like a skid steer,” Powell notes. “Another advantage of EH systems is the ability to add advanced diagnostics, which make it easier to maintain and prevent downtime.”
EH controls let the operator adjust to the preferred control pattern at the flip of a switch. “The ability to switch operating patterns with the simple push of a button is something that is consistently praised by operators,” says McElroy. “That ability to easily switch the control pattern can mean the difference between a new employee expertly operating the machine in a pattern they are familiar with vs. trying to muddle through and make due because they are unsure of how to change the pattern.”
Operators are also able to adjust the “feel” of the controls as needed. “The challenge is that ‘feel’ is very subjective — each operator has their own interpretation on what feels right,” says Steve Zumbusch, director, Technology Development, Eaton. “EH control enables the user to match their ‘feel’ preferences to how the machine actually responds.”
EH controls offer greater speed, as well. “You can make electronic controls fast and reactive to the point that they are significantly faster than pilot controls,” says Bobcat’s Fitzgerald. “Control systems are tested at maximum speed initially. We then manage settings internally through software to make them smooth and work properly for the operator.”
Since software serves as the interface between the hydraulic controls, it is possible to add features in the future via upgrades without having to change hardware. “Software is an enormous part of EH systems and the flexibility they provide,” says Zumbusch. The importance of such features is likely to increase as sophisticated attachments become equipped with positioning and telematics technologies.
EH systems allow a new degree of customization. “In the digital world, customization is easier and has fewer recurring costs,” says Schottler. “These recurring costs make it much more expensive to make special hardware for a customer, as compared to providing customized software or a different parametric setup.
“As end users demand better performance and custom solutions, machine builders will continue to build on the unique capabilities that electronic controls will bring to differentiate their machine,” he continues. “Safety fencing (limiting the operating footprint), return to dig and other features make these machines more productive and lower overall operating costs for a job to justify adding more capabilities.”
Easing operator loads and automating certain functions will also make the machines more productive, even in the hands of a novice, says Schottler.
“EH systems allow Caterpillar to offer premium control features on our skid-steer loader, multi-terrain loader and compact track loader models,” says Kevin Coleman, senior marketing engineer, Caterpillar. “[Such features include] adjustable implement response modes, adjustable drive response modes, Speed Sensitive Ride Control, Creeper mode, Dual Self Leveling, work tool positioner and Return-to-Dig.
Another feature is power management. “With EH controls, the engine power output can be set to match the power being requested by the operator,” says Schottler. “For under-sized engines, the power request can also be manipulated so that the engine does not stall. Additional functions include bucket shake and selectable flow priority, in which key functions continue to get the flow if there is not enough to meet all functions.”
Attachments and Application Determine Best Strategy
“As performance expectations continue to rise, these machines will have to be tailored to get the most out of each attachment,” says Zumbusch.
EH systems provide this ability. “EH controls allow machines to be dynamically configured for certain attachments,” says Schottler. “When a new attachment is placed on the machine, the controls can be reconfigured to match the implement’s requirements (scale the flow gains, maximum flow limitations, etc.).”
The joystick control system offered by Bobcat clearly illustrates how EH-enabled features such as Speed Management and drift compensation directly enhance attachment productivity. “With Speed Management, you can set the specific speed on the machine, move the joystick to its full stroke and have full hydraulic flow so your attachment isn’t overloaded or being pushed too hard,” says Fitzgerald. You can also optimize the speed to the job. “That really works well with cold planers, trenchers or a grader.”
Drift Compensation further enhances attachment utilization. “If you are operating a planer or a trencher that is offset to one side, you can adjust drift compensation to give more power to one side than the other, which helps the operator maintain a straight direction,” says Fitzgerald. The operator doesn’t have to keep making manual corrections.
Automated features can also simplify attachment operation. An example is Bobcat’s tree spade attachment. “You can set it in automatic mode where it will automatically activate each spade individually,” says Fitzgerald. “The operator presses a button and it automatically forces the spades into the ground in an efficient manner.”
But EH controls are not the correct choice for every application. To meet diverse customer demands, a few manufacturers offer several control options.
Bobcat offers three different control systems. “Joystick controls tend to be more popular on the compact track loader line than in the skid-steer line,” says Fitzgerald. “The track loaders are heavier and push more material. Operators feel more force on manual steering levers when compared to joysticks. From a long-term operational standpoint, joystick controls offer low effort, low fatigue operation. When looking at our product lineup, we see joystick controls used more on the larger, heavier, higher horsepower machines than we do on smaller machines.”
This is partially due to cost. “On a lower priced skid-steer loader, adding that option has a larger effect on the overall purchase price than it does on a larger horsepower track loader,” Fitzgerald explains. “Overall, the joystick control option on Bobcat loaders increases every year. Once the operator has been trained and learns what features are available, their productivity and profitability increase.”
“The skid-steer loader and compact track loader market offer both high- and low-end machines,” says Powell. “Similar to your car, you can either get all the bells and whistles or a simple car with the basics. Pilot hydraulics are offered on the lower end/inexpensive machine for basic work. Any platform that relies on precise control or complex functions will always see a benefit with EH functionality.”
For instance, the advanced controls on Caterpillar machines provide the ability to adjust a number of machine settings. “The operator can easily select one of three Implement Response levels,” says Coleman. “This allows the operator to choose the responsiveness of lift and tilt functions to match the requirements of the implement functions to specific work tool attachments or tasks. This means improved productivity by giving greater work tool control (lowest setting) for precision jobs like material handling where precise work tool control is desired. It also provides quicker movements for production work (highest setting).”
EH systems provide significant advantages when operating complex implements, such as cold planers, trenchers, brooms, etc.
“The EH mode enables Caterpillar to offer a creeper control mode, which allows the operator the ability to fully move the drive joystick in the direction of travel,” Coleman explains. “Adjustments can then be made via the main cabin display, while driving to limit the machine ground speed and provide a performance match between the machine speed and the optimum work tool attachment speed. This provides greater comfort to the operator when using these types of hydromechanical tools for long periods of time. It also results in a more consistent cut/trench/sweeping pass to deliver a better finished product with one pass, minimizing or eliminating any required rework.”
By allowing the operator to tailor the hydraulic system’s response rates to fit the application, jobs can be completed more confidently and quickly. For instance, Case Alpha skid-steer loaders offer nine preset control settings — combinations of three for speed and three for control. Case claims these settings meet the needs of 85% of operators. For those that need even more fine-tuning capability, the company offers a custom option with the potential for 1,225 different combinations of speed and control settings.
“One of the examples regarding how EH controls give the operator more flexibility revolves around contractors regularly moving between wide open areas and smaller, more confined areas, and operators who regularly work with different attachments,” says McElroy.
For example, an operator using a skid steer with forks in a wide-open supply yard will operate the machine at high speed/high control. “As that operator moves indoors where there are new obstacles, workers and more confined operating spaces, they can easily switch to a low/low setting,” says McElroy. “In other applications where attachments are being used that require some level of precision or there is a heavy load being put on the attachment — planers, milling machines, soil rakes, a broom or a snowblower — a low/low setting may be most appropriate.”
Such flexibility means work can be done in the most efficient manner for the given task. “We are always looking for new, innovative ways to help customers solve problems and make their jobs easier,” says Caterpillar’s Coleman. “EH controls and software solutions are part of that evolution. The EH control platform has already played a part in the state-of-the-art features we deliver to customers to help them solve problems, make their jobs easier and, ultimately, help them make more money with our equipment.”