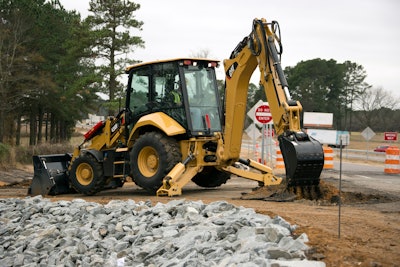
With the ability to dig, load and lift, as well as utilize a variety of attachments front and rear, backhoe-loaders serve as multi-functional tools in many construction fleets. Their value on the jobsite is further enhanced as manufacturers offer an ever broader range of configurations, features and options to better meet customer demands and applications.
Sorting through the multitude of choices now available in backhoe-loaders can be daunting. As such, manufacturers advise you to begin by defining the application, then evaluating basic machine capabilities, features, options and serviceability to determine the best fit.
This process is helpful even if you’re replacing an existing model, as needs can change over time. “The first thing to consider is how, if at all, the application changed, or does it remain the same?” suggests Norm Blair, product consultant, backhoes and tractor loaders, John Deere Construction & Forestry. “For example, is the backhoe required to do more on the job than previously? Is it digging deeper, lifting more, loading trucks, roading on the jobsite or to and from the jobsite, or carrying more attachments?”
Basic Machine Specs
When spec’ing a backhoe-loader, maximum dig depth is typically the starting point. “Other factors play a role, but initially it’s really about how deep a machine can dig,” says Jon Hundley, construction marketing manager, New Holland North America.
Today’s full-size backhoe-loaders are typically split into 14-, 15- and 17-ft. dig depths, while compacts can dig down to about 10 ft.
“It is important to determine the most common depths that the machine will be used for,” says Jeff Jacobsmeyer, product manager, tractor loader backhoes (TLBs), Kubota. “If an operator rarely has to dig over 10 ft., for example, the extra costs for machines that dig deeper can be saved.”
For those requiring greater digging capabilities and reach, a number of manufacturers offer configurations with extendable dippers. For example, JCB’s extra dig configuration adds 2 ft. of dig depth on the compact 3CX and 4 ft. on full-size models, says Rafael Nunez, JCB backhoe-loader product manager.
An extendable dipper can offer a number of advantages. “Extra dig depth and reach allow more flexibility on the jobsite,” says Blair. “This additional reach also minimizes how often the operator has to move the machine when using the backhoe to trench or for other applications, potentially increasing productivity.”
This added ability comes within the same machine footprint. Hundley notes that a hydraulic extendable dipper (HED) on a New Holland B95C provides an extra 3 ft. of extension to the backhoe all while maintaining the machine’s compact size. Consequently, he says, “The HED take-up rate from our customers is very high.”
Lifting capability is another key consideration for both the front and rear of the machine. “If a customer is using the loader bucket to lift heavier items, such as steel plates or pallets of pipe, look at the loader end specifications to determine if a machine is the right size,” Blair advises. “As for the backhoe end, an operator may also require the machine to lift heavier items such as pipe or manholes, so a customer has to consider the lift specifications of the backhoe end.”
Before selecting a backhoe-loader, determine the types of loads it is likely to lift or carry. “If the machine will be used to lower materials into a trench, it is wise to know the weights of those items to not only lift and boom with the backhoe, but also to move loads that will be required with the front-end loader,” Jacobsmeyer advises.
When sizing buckets, Blair recommends matching the loader bucket size to the amount of material to be carried, while ensuring the machine is capable of lifting the weight of the load to full height.
Because a variety of attachments are commonly used with backhoe-loaders, also take into account the hydraulic flow capabilities of the machine. “Contractors must do some homework to determine flow rate requirements of attachments that will be installed in the future,” says Jacobsmeyer.
It’s easier and less costly to spec the machine now to ensure it has the capabilities you may need later. “Auxiliary flow outlets can be added to the rear of the machine for backhoe work with breaker and thumb attachments, and auxiliaries to the front loader to run accessories like grapple buckets and sweepers, for example,” says Jacobsmeyer.
Consider Power and Size
Engine and hydraulic horsepower are important considerations — especially hydraulic horsepower. “It’s what gives you breakout force and digging depth for both the backhoe and the loader,” says Hundley. “It’s really gpm that is the force behind what you are doing.”
Engine horsepower becomes a bigger consideration with models in the mid-70-hp range. “Diesel exhaust fluid (DEF) is required on engines above [74 hp] to meet Tier 4 Final emissions,” says Jacobsmeyer. “Rental customers and entry-level operators appreciate the fact that DEF is not needed in machines under 75 hp, where a diesel oxidation catalyst and diesel particulate filter will meet current emissions standards. Purchase costs are also usually lower on these 74-hp machines because there are no expensive DEF exhaust aftertreatment systems.”
“If a contractor is looking for an entry-level machine, our 415 is less than 75 hp, while our 416 has nearly identical specs but higher engine horsepower that requires DEF,” says Dustin Adams, product application specialist, Caterpillar. “Smaller owner/operators may be attracted to the lower hp machines, while larger companies will probably have a service truck with dedicated people who can routinely maintain machines that require DEF.”
Generally, the higher the horsepower, the larger the machine. Machine size and weight can affect both the ability to work in confined conditions and transportation requirements to and from the jobsite.
“Compact machines can work in areas that other machines just can’t fit, causing less collateral damage such as breaking sidewalks,” says Jacobsmeyer. “The weight of the machine also determines the ability to safely transport the unit in many cases. Kubota compact TLBs range from a B26 with a weight of 4,000 lbs. to the M62 that weighs in at just under 9,000 lbs. The DOT requires a CDL and larger trucks to transport machines considered ‘full size.’”
Payback Potential of Advanced Features
Once general machine capabilities are addressed, it’s time to look at features and options that can enhance performance, flexibility and ease of operation.
The choice between a basic backhoe-loader vs. one with advanced features can come down to the hours of operation per day. “If it will be a machine that someone will hop in and out of a couple times a day for utility type work, a more basic machine can be a good choice,” says Adams. “But if an operator will sit in the cab for six to 10 hours a day, or use it for transportation between jobsites, choosing a machine with advanced features can create a more comfortable environment for working long hours.”
Advanced features can include ECO mode for fuel savings; flow sharing valves for improved operator control and multi-functional performance on the back end; load-sensing hydraulics for power on demand; pilot controls with pattern changers; and integrated tool carrier configurations that are designed specifically for tool attachment flexibility.
“Features and options can add value to the customer, the application and the business,” says Blair. He cites such features as cab comforts, ride control, autoshift transmissions, extendable dippersticks, auxiliary hydraulics and quick couplers. “Although adding options ultimately affects the purchase price, I see customers trying to make these machines as versatile as they can for their jobsites and their businesses.”
Such add-ons can also boost the resale value. “Make sure the machine you are buying fits your needs. But if you think you will ever resell the machine, make sure it is marketable,” says Nunez. “Features such as four-wheel drive, extending dippers, one-way and bidirectional flow pipe work options, etc., make the machine more versatile and add to its value. Operators are always looking for performance, as well, such as high-horsepower machines that offer better roading and loading capabilities.
“Comfort is also important,” he adds, “so look for options such as air ride seats, heated seats, etc., to make the operator comfortable.”
Optimize Loader Operation
Pay particular attention to available transmission options. “Powershift transmissions and autoshift transmissions tend to give the operator more flexibility, as well as potentially enhancing productivity when pushing material with the loader, loading trucks or transporting the machine across the jobsite, or from one jobsite to another,” Blair points out.
Kubota’s line of TLBs provides a hydrostatic transmission with selectable speed range. “This gives the operator more precise control when doing loader work,” says Jacobsmeyer.
Hydrostatic transmissions are also available in some JCB models. “They provide a 25-mph road speed to enhance performance for operators when moving around the jobsite, or from jobsite to jobsite,” says Nunez in reference to the 3CX Compact.
Another popular feature among John Deere customers is mechanical front-wheel drive. “It allows the backhoe more versatility depending on ground conditions,” Blair states. “It can also enhance productivity and operator machine control.” Plus, it can have a positive effect on resale or trade-in value.
Control and Automation Options
Machine controls can have a dramatic effect on performance and ease of operation. Pilot and electrohydraulic (EH) controls can offer greater control and improved ergonomics for the operator compared to mechanical valves.
JCB offers manual controls and two types of pilot controls — EasyControl and Advanced EasyControl. “EasyControl is designed to feel like manual controls,” says Nunez. This can be a good choice for operators who may be less comfortable with full excavator-style pilot controls. “The excavator end is controlled by seat-mounted pilot controls while the loader end is controlled by a manual lever. Our Advanced EasyControl is full pilot controls where everything is seat mounted for both loader and backhoe functions.”
Caterpillar offers pilot controls with pattern changer as an upgrade option for entry-level machines, and standard on higher-spec models. “The pattern changer offers the ability to change between backhoe and excavator patterns,” says Adams. “Because so many operators are used to running excavators, they can switch to the excavator pattern and run that same style in our backhoes. They can easily jump into the machine and be familiar with its operation because the functions of the joystick will be the same.”
Other available features are designed to automate certain functions — for example, those related to ride, such as New Holland’s Glide Ride and JCB’s Smooth Ride System.
“Glide Ride is essentially a shock-absorbing system for the loader. If a contractor is doing loader work and transporting a full bucket, it will keep the bucket level,” says Hundley. “In our machines, it is an automatic system with a speed sensor. Contractors don’t have to remember to turn it off. When a certain speed is achieved, the system will turn on... to cushion the load during transport. When the machine slows down to dump the load, it will automatically turn off.”
JCB offers a full suite of automatic features — AutoTHROTTLE, AutoDRIVE, AutoBOOMLOCK, AutoSTABILIZERS and AutoIDLE — designed to make it easier for the operator to perform repetitive tasks. “There are so many tasks that are done repetitively 10, 20, even 30 times a day… such as setting engine rpm,” says Nunez. “With these automatic features, we have made it simpler to operate the machine by automating many tasks.”
Alternative Configurations
Caterpillar integrated tool carrier (IT) models can simplify attachment work and make the machine more productive. “If a contractor will do a lot of lifting/loading and carrying, an IT backhoe features a quick coupler that allows the ability to switch tools quickly,” says Adams. “The loader arms are also designed to provide better breakout forces, and a true parallel lift provides better dump/loading clearances.”
JCB offers parallel lift on its machines, as well. This makes it easier to use attachments such as forks. “It also works great for the loader bucket,” says Nunez. “As you lift the load, you won’t lose material.”
Additional configuration options for JCB machines include a side shifting carriage that provides the ability to dig a square trench without repositioning the machine; and a line of 4CX Super models that have equal size tires on the front and back for wheel loader performance in a backhoe.
Consider Serviceability
“Serviceability is important in backhoe-loaders because when they are purchased, they are typically kept for a long time,” says Hundley.
“We see more and more customers interested in talking about serviceability today,” agrees Blair. He stresses the importance of viewing service from the operator’s standpoint, as well as the technician who will be servicing the machine.
Because operators should perform a daily check before starting the machine, a simplified process and easy access to serviceable parts can help ensure those tasks are actually completed. “The key to a long life cycle is ease of serviceability and daily maintenance to encourage operators to take better care of the machines,” says Adams.
The positioning of everything from grease zerks to replacement filters is important, says Jacobsmeyer. “If a component is ‘out of sight,’ then the possibility of being ‘out of mind’ can allow it to be easily overlooked,” he points out.
“[The ability to] check oil levels from one side of the machine without having to climb up on it, and having grease points that are easy to access, make the job easier and more likely to be done,” says Blair, “thereby having a positive effect on maximizing component life.”
Features found on today’s backhoe-loaders provide the ability to monitor the machine from a serviceability standpoint and manage it from an operational side, both onboard and remotely. “Onboard monitors alert operators to any potential issues with the machine on the display with a diagnostic trouble code, as well as with full text. This system monitor also includes component fluid levels,” Blair explains.
Remote capability comes in the form of telematics that can send alerts to the customer and/or dealer via cell phone or computer, as well as provide diagnostic capability. “These components have proven to be very helpful to customers and have a positive effect on maximizing machine component life,” says Blair. “Telematics also allow a customer to manage their machines by looking at data such as idle time, fuel usage and more to help maximize productivity, potentially reducing costs and creating a positive impact on the business.”
JCB’s AutoCHECK is a similar system for simplifying service and maintenance. “As soon as an operator keys on the machine, it runs through all of the daily fluid and engine checks, letting the operator know if it’s safe to crank the engine,” says Nunez. “It’s a great way to ensure daily checks are being done.”
Contractors can then remotely monitor JCB machines via the LiveLink telematics solution. The system collects data about the health of the machine and alerts the contractor of potential problems before they become serious, making it easier to schedule service.