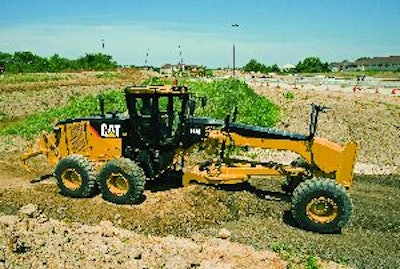
Motor graders require a little more care than other pieces of heavy iron to ensure they can maintain precise grades. "Considering that finish grade is typically from 1/8 to 1/4 in., turntable and moldboard slide tolerances must be maintained as close as possible," says Phil Newberry, market development engineer, motor grader marketing, Caterpillar. "Once wear reaches or exceeds these tolerances, it makes it extremely difficult to achieve grade in a productive fashion."
Regular maintenance helps prevent excessive wear on critical moving interfaces. "Grease points are by far one of the most important maintenance items on a motor grader," says Woody Ferrell, vice president of sales and marketing, Champion Motor Graders. "Motor graders have more moving joints and implements than most any other type of construction equipment. "
This requires vigilant record keeping of the service intervals. "Stay within the recommended service intervals stated by the manufacturer for all serviceable items, not just engine oil changes," says Ferrell. "There are other wear items that get overlooked, because the service technicians get used to performing a standard type service or the customer cannot have any extended downtime. Therefore, the customer will only allow the minimal service so he can keep working the motor grader."
Yet, there are areas that require more attention. "The most common wear points are the blade slide guides, circle guide shoes on the turntable and blade lift cylinder connections," says Keith Lee, research and development, LeeBoy. "Any play in these areas allows the blade to move " 1/16th in. in two, three or four places can add up quickly." This is known as tolerance stack. You start adding play in all of the critical joints together and pretty soon the whole system is loose.
Maintain tolerances
The tighter you can keep the components, the better. "Tightness in the moldboard slides, circle supports, drawbar ball stud and even the operator"s seat are all important factors to consider when determining if the grader can produce a finish grade to the tolerance specified," says Brian Lowe, product and communications manager - motor graders, Volvo Construction Equipment. "As the accuracy of most machine control systems are checked at least daily, if not more frequently, so too should the critical areas of the circle and moldboard slide be inspected."
Lowe adds, "Where ever there is a sliding surface, there is the potential to have wear and subsequent loss of blading tolerance. By default, the circle support shoes and moldboard slides get the most attention. But the operator must also consider the connection between the lift and sideshift cylinders and the drawbar."
Tight tolerances allow the machine to react quickly to operator input. "Clamp and guide shoes in the circle turn system can restrict the circle"s rotation when worn or out of adjustment, therefore, not allowing quick and accurate adjustments while grading," says Ferrell. "The ball stud connected to the drawbar can affect this, but not as much, and it is quickly adjusted if there are shims that can be removed once wear has been detected."
You also need to watch the trunnions. "The trunnions hold the blade lift cylinders and receive the majority of the shock loads during grading," says Ferrell. "You can properly adjust your circle and slide, but if your grader has excessive wear in the trunnions, then you lose the ability to hold tighter tolerances."
In addition, out-of-tolerance components can create excessive wear. "By not keeping your circle and slide maintained to within 1/16 to 3/16 in., you subject yourself to premature wear," says Ferrell. "A lot of play in your components allows lubricants to get out and more dirt [to get] in."
Monitor the cutting edge
The type of material you commonly work with has a major impact on how often you need to examine your cutting edges. "The type of material greatly affects cutting edge life," says Newberry. "Very abrasive material can wear out a set of cutting edges in an eight-hour shift. And in softer, non-abrasive material, the cutting edge may last a month."
Because the cutting edge actually performs the work, a worn blade can make it nearly impossible to achieve a close tolerance grade, and/or will extend the time to complete the operation, which in turn affects operating cost, Newberry points out.
You need to make sure the blade is capable of cutting a flat surface. "If you look at a cutting edge on a typical municipal grader, you see that the wear pattern has crowned the edge wearing the center faster than the outer ends," says Lowe. "While this still may be serviceable for dressing a seldom used country road, it is not acceptable for a finish grade job. The contact face of the edges must be straight. It will be cheaper to change cutting edges than the cost of re-grading the surface to compensate for the worn edge."
A couple of indicators alert you when the cutting edge must be replaced. "Two basic measures are when the cutting edge wears to be even with the moldboard, or if you can visually see uneven wear across the width of the cutting edge," says Lee.
"The cutting edge should always be replaced prior to wearing into the moldboard " hopefully, prior to wearing out the bolts and nuts that bolt the two together," says Ferrell. "Replacement should occur at least 1/2 in. before the cutting edge wears into the moldboard."
When it is time to replace the cutting edge, the quality of the blade can also make a difference. "There are differences in steel hardness that can affect the life of aftermarket edges," notes Newberry.
Not every cutting edge is created equal. "Cutting edges from OEMs and aftermarket suppliers vary in metallurgical properties " hardness, break resistance, etc.," says Lowe. "Some are better in one type of material; others in another application. This is another area where the experience of the grader operator is important, as he often has a feel for the "right edge" for the conditions " something a new operator hasn"t learned yet."
There are steps you can take to improve accuracy when replacing cutting edges. "The single biggest tip is to change all of the edges across the length of the moldboard at one time. Otherwise, there will be a step in the finish grade," Lowe explains. "Save the partially used edges for site prep work where the tolerances are not as critical."
Lowe adds, "The other tip is to ensure that the mating faces of the edge and moldboard are free of dirt and grit. The bolts stay tighter and there is less chance of breakage if a hidden object is hit when doing rough work. Use a full set of new bolts, nuts and lock washers and tighten from the center out to each end, and do so with the proper torque."
Newberry suggests that replacement of the cutting edges is a two-person job. "Use a punch to align the holes and hold the cutting edge in place to start the bolts. Use air impacts, if available," he advises. "Make sure the edge of the moldboard is clean to ensure a good, even fit."
You also need to make sure the motor grader is well suited to the application. "The wear will increase if the grader is not sized right for the application," says Ferrell.
Stock all wear items
You need to keep a supply of wear items to keep your motor grader running at optimum. "All wear items " from the ball stud to the drawbar, along with the clamp and guide shoes and a stock of cutting edges " are critical to the grader"s daily performance," says Ferrell.
"Contractors should keep the unit properly greased, and keep on hand a cutting edge and shim stock for slide components," Lee recommends.
Frequent inspections are a must if you want to maintain productivity and tolerances simultaneously. "From top to bottom, checking the cylinder connections, turntable, blade slide and cutting edge will give the contractor a good idea of how tight the tolerances will be when grading begins," says Lee.
Newberry advises a visual and/or stringline check of the cutting edge to make sure it is even. Then check for excessive play in all critical components, i.e., moldboard slide rail, circle and lift cylinder joints.
Excessive play is the enemy of accuracy and productivity. "The tighter the system, the faster grade can be achieved," says Newberry.