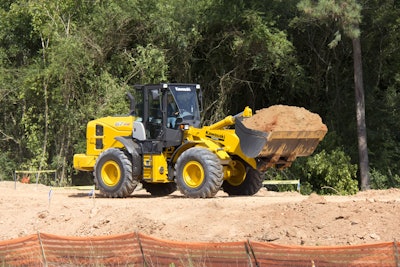
When selecting the most efficient wheel loader, the key is to hit your desired production goals for the lowest total cost of ownership.
“The best measure of a wheel loader’s efficiency is production vs. fuel consumed,” says Brian Pleinis, manager, engineering section, KCMA Corp. “A wheel loader manufacturer can claim lowest fuel consumption, but if the production suffers as a result, then the cost per ton moved has not improved.”
“You can have a very fuel-efficient wheel loader, but if it sits 50% of the time, you are really not efficient,” adds Mike Stark, wheel loader product specialist, Doosan.
Not sizing the machine to meet production targets is a common mistake. The number of loads moved on a daily basis and the material density help determine the ideal size. “You know how much material you want to move in a day and how many trucks you have,” says Stark. The wheel loader size, bucket size and bucket type all play a role.
While it’s possible to oversize a wheel loader, that’s not where most complaints originate. “Customers undersize rather than oversize,” notes Stark. “They try to save money by buying the smaller wheel loader. Then they put on a larger bucket than they should. As a result, they don’t get the lifting capacity or the productivity they really need.”
But bigger isn’t always better. Engine downsizing or down-speeding offers opportunities for fuel savings. “This is the goal of several OEMs. It is the trend we will see in the near future for everyone,” says Wayne Powell, senior manager, product support, KCMA Corp. “Kawasaki went to a four-cylinder engine several years ago — when most competitors had six cylinders — with a significant fuel savings, yet our breakout and lifting capacities remained unaffected.”
Kawasaki proved smaller displacement engines could be more efficient. “We are using a 9-liter engine in a machine that previously used a 13-liter engine,” says Pleinis. “Smaller engines have lighter reciprocating assemblies, which consume less fuel to make the same power. Furthermore, we are seeing notable efficiency gains by reducing overall driveline friction.”
Choose the Driveline Carefully
“Probably the greatest gains in fuel efficiency come from the driveline,” says Powell. “Adding more speeds and lock-up torque converters can result in 3% to 5% better fuel efficiency in certain applications where there is a lot of travel, like load and carry.
“A standard torque converter is a wonderful device allowing tremendous torque multiplication when digging, but it loses efficiency as the travel speed increases,” he explains. “A lock-up clutch can virtually eliminate torque converter inefficiency at higher travel speeds and help in some hill climbing applications, depending upon the slope. It essentially becomes a direct drive.”
Both five-speed transmissions and lock-up torque converters are becoming more popular. “More of our machines are moving from four-speed to five-speed transmissions and we are adding lock-up torque converters to more models,” says Kawasaki’s Powell. “Having more speeds available allows the onboard computer to match machine speed more efficiently.”
Doosan offers a five-speed transmission option that can boost efficiency when traversing slopes. “Maximum travel speed would be the same, except you have different shift points between the gears which would benefit you when climbing a hill with a load,” says Stark. “If you do a lot of hill carrying, it is recommended to go with the five-speed transmission, especially with larger loaders.”
“On load-and-carry applications, a lock-up clutch torque converter will impact fuel to a 20% or more magnitude,” says Lucas Sardenberg, marketing consultant, Caterpillar. “Similarly, traction devices such as differential locks or limited-slip axles can avoid tire spin and allow less time digging or travelling, which also improves efficiency.”
Every manufacturer has its own approach. Doosan uses a fully automatic torque converter transmission with an electronic power optimizing system. The engine computer and transmission controller constantly communicate to provide optimum power and efficiency.
Hyundai incorporated a new system called the ICCO, or Intelligent Clutch Cut Off. “It gives infinitely variable clutch cut-off control so you can apply more engine power to your hydraulics when you are raising your boom to dump a load,” says Corey Rogers, Hyundai. “That is going to contribute to the overall 5% increase in productivity that we gain from the HL900 Series.”
Hydrostatic transmissions have also benefited from technology advancements. For instance, a hydrostatic drive system in the Doosan DL200-5 and DL200TC-5 wheel loaders replaces a torque converter transmission. It promises improved fuel efficiency because of higher performance at lower engine rpms. The electronics allow power management of the hydrostatic system. This includes speed management, which adjusts the maximum travel speed independently from the engine speed. The speed management feature allows operators of the DL200-5 and DL200TC-5 to obtain full engine rpm for optimal lift arm or hydraulic attachment performance, yet fine tune the maximum machine travel speed via seven preset levels within first speed range, up to 8 mph.
Other transmission technologies are also emerging. “New technology is already being tested and evaluated for the next generation of loaders,” says Powell. “Whether it is a type of continuously variable transmission (CVT) or electric hybrid drives, they have to be more efficient, but also affordable and maintainable. Certain technology might be very efficient but too expensive to buy, or require on-staff high-voltage technicians which many customers simply can’t afford.”
Bucket Selection is Critical
Bucket fill factors have a major impact on overall efficiency. “The bucket needs to load effortlessly to ensure the least amount of time/fuel is consumed during the process,” says Pleinis.
“A better bucket design contributes to equipment spending less time digging and, therefore, improves efficiency,” says Sardenberg. “In reality, it is one of the most important parts for a wheel loader. A ‘bad’ bucket design causes operators to spend more time than necessary digging.” This leads to increased fuel burn, poor visibility and poor material capability and retention — in other words, more work to achieve the desired production.
Caterpillar considered all of the factors noted above, adding typical material flow mechanics and matching bucket design with machine capability, when designing the Caterpillar Performance Series Buckets. “Some of the design criteria include a longer floor, which allows better material flow, curved edges for better material retention and integrated spill guard to avoid materials dropping into the linkage,” says Sardenberg.
During evaluations using the Cat 972H and 980H wheel loaders with conventional buckets vs. Performance Series models, the Performance Series Buckets averaged 5% to 7% better fuel efficiency, a 3- to 5-second reduction in per-cycle loading time and a 0.5- to 1.5-ton increase in per-pass payload.
Bucket sizing has a similar impact on productivity. “You want to use the full capability of the machine whenever possible,” says Doosan’s Stark. The correct size depends on the density of the material being lifted. Consider a wheel loader with a theoretical 2-cu.-meter bucket size. “You could go up to a 4-cu.-meter bucket if it is light material being moved. If you have multiple densities of material, we offer quick couplers so you can switch the bucket without getting out of the cab. ”
Manufacturers invest a lot in finding the optimal match. Consider the recently introduced Hyundai HL940TM Tool Master. “The bucket is a patented new design by Hyundai,” says Rogers. “We have curved side plates. We have an enhanced size spill guard. We have a deeper throat in the bucket. It is a totally different profile. The key features of the different shape, the curved side plates and the larger spill guard give us about a 5% better fill factor on the bucket, which overall contributes to 5% increased productivity.”
Electronic Features Optimize Efficiency
“We could not achieve the extremely accurate fuel delivery, engine/driveline control and system intelligence without the advanced electronic technology we have today,” notes Pleinis.
Of all the electronic capabilities, auto-shutdown promises one of the greatest efficiency benefits. “With onboard monitoring of actual idle time and the use of telematics, we can see that some customers have 45% to 65% idle time,” says Powell. “The machine can automatically shut down after four or five minutes of continuous idling and save fuel.”
Often, you may not realize the true potential of auto-shutdown due to the operating environment. “The operators prevent it from happening because the cab temperature will soar in the summer or plummet in the winter, affecting their comfort,” Powell comments. “Coming up with a practical way to keep the cab comfortable even if the engine shuts off to save fuel is the key to stopping unnecessary idling. Kits that do that now are expensive, take a lot of space and are aimed at on-highway sleeper cabs.”
You also need to understand how reduced idle time actually impacts the measured fuel efficiency. “It is good to remember that reducing idle time will result in a higher fuel rate than before just because the loader will be working hard most of the time,” says Sardenberg. “But in absolute consumption, fuel will come down.
Another common feature on today’s wheel loaders that is made possible by electronics is selectable power modes. They can match machine performance to the application and thereby increase fuel efficiency. “Doosan offers three power modes on its engine,” says Stark. These include Power, Standard and Economy. “In simple terms, they reduce the machine’s maximum rpms. There are other things going on at the same time through the control unit, but we are reducing maximum rpms. For example, Economy mode may be best suited to load-and-carry applications, while Power mode delivers the highest performance for the most demanding applications and Standard mode would be optimized for general work.”
Electronics can also enhance the efficiency of the hydraulic systems. “Now the pumps are controlled and can be tuned instantly ‘on-the-fly’ by the machine’s computers,” says Powell. “So we have been able to bring precision and efficiency to wheel loaders, resulting in another 3% to 4% overall efficiency. We have added hydraulically controlled fans that actually shut off when cooling is not needed, and under hard acceleration. A medium-sized fan can, at full speed, consume 30 hp. So using that power to run the fan only when absolutely necessary can be a big savings — another 1% to 3%.”
“One caveat of many systems is that if the on-demand fan is running at full speed, there is less power available to hydraulics, etc.,” says Sardenberg. “At Caterpillar, however, we provide customers with a constant net horsepower, which means if the on-demand fan is running at full speed, the same amount of power will still be available to perform work in the most efficient manner.”
Payload Systems Ensure Maximum Loads
“There is no better way to ensure the wheel loader is delivering the necessary production efficiency than with an onboard load scale,” says Pleinis. “By measuring your daily production against daily fuel consumed, you instantly know how much fuel was consumed for every ton of material moved. Also, the use of an onboard scale allows the operator to know that he is moving the optimum load with every pass to ensure he delivers the best production.”
An onboard weighing system is one of Hyundai wheel loaders’ most important standard features. “Our onboard weighing system allows you to measure multiple truck loads,” says Rogers, “and you can also do total load-out per day. It is +/- 1% accuracy, so it is on par with many third-party, very expensive weighing systems. It is a great guide for an operator who wants to keep track of his production throughout the day and stay on target.”
Caterpillar offers a tip-off feature, as well. “It allows operators to dump extra material not needed that is in the bucket back to the pile or the truck,” says Sardenberg. “This avoids having operators guess or follow a truck to the scale house to top off their load. Overall, the benefits of a scale system will far outweigh its cost.”
Gain Critical Insight
You cannot manage what you cannot see. Color touch screen monitors now provide the operator with real-time usage data, including fuel economy.
“The information can be displayed in the cab, downloaded to a laptop and transmitted through the telematics system,” says Powell. “The operator can call up the machine’s fuel consumption and determine the average for various jobs or work sites. On machines that have telematics, the information is updated and transmitted daily to the KCMA Global e-Service Owner’s Site. Using the data effectively, the equipment management team can focus on reducing machine idle time and optimizing operator performance.”
Most manufacturers offer telematics solutions that provide information that was not previously readily available. Caterpillar allows data collected through its telematics system to be accessed via VisionLink. “It is possible to use reports and the information to increase efficiency, such as checking payload and fuel consumption per day or even by operator, idle time and many others,” notes Sardenberg.
“You can see how many hours a machine is idling,” notes Stark. “If there is excessive idle time, you can then investigate if you need to get more trucks on the jobsite or if there is something else happening.”
Doosan telematics will also give you a picture of how the machine is being operated. “It tells you how many hours that wheel loader has actually operated in Power Mode,” says Stark. “It tells you the time frame it has been operating in Economy Mode.” That allows the contractor to analyze machine operation.
“A fleet manager can easily recognize a machine that is under- or over-utilized by monitoring the telematics data,” says Pleinis. “Additionally, a fleet manager can monitor telematics data to understand which operators tend to allow excessive idle times and train them for more efficient operation of the machine.”