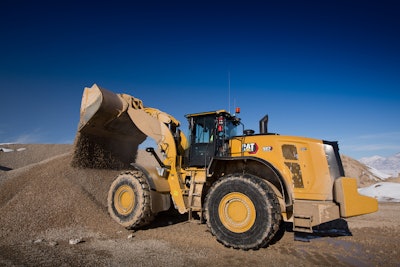
Caterpillar is rolling out four models in its Next Gen wheel loader line – the 980, 980 XE, 982 and 982 XE. These 9- to 11-tonne (10- to 12-ton) wheel loader class machines include an expanded technology platform to increase machine performance and improve operating efficiency. The XE models will feature a parallel path continuous variable transmission (CVT) that will increase fuel efficiencies up to 35% compared to the previous 980M and 982M powershift models when comparing tons of material moved per gallon of fuel burned.
The 980 and the 982 are the first of the Next Gen wheel loaders to launch. Additional Next Gen models will soon follow.
“The 980 and 982 are going to redefine the definition of fully loaded. With more technology standard, these machines will produce more and cost less to operate than any wheel loader in Caterpillar’s history of designing and manufacturing medium wheel loaders,” says Bryan Cherry, global product marketing consultant, medium wheel loaders, Caterpillar. “The 980 and 982 are going to deliver up to 20% lower maintenance costs.” This is partially due to extended fluid and filter change intervals. All maintenance intervals are now scheduled in 1,000-hour intervals. The XE variants promise to reduce maintenance costs by up to 25%. In addition, productivity will increase. “We are delivering 10% more productivity vs. the first series M [loaders].”Caterpillar
Two distinct machines
While they may look similar, the 980 and 982 are very different machines, says Scott Schmidtgall, product application specialist – medium wheel loaders, Caterpillar. The 980 is suited as a three-pass loader in a quarry when you are loading 20- to 24-ton trucks. “If you have heavy stockpiling work, you can load out 24 trucks an hour from a production standpoint," he states. "You may be getting into two passing with some of your heavier materials.
“If you have higher production demands than 24 or 25 trucks per hour -- if you want to get above that into the 30 to 35 trucks an hour -- that’s where the 982 can really pay off for you,” he continues. “It’s a two-pass loader in many material types. This 982 has a 12.5-ton rated payload, up to 14 tons with Caterpillar’s payload policy. Instead of just being in that 24- to 25-ton range, where several models are, and two passing, Caterpillar can get beyond that into that 27 or 28 tons two passing and keep that production up.”
Trucks and trailers have become a little lighter to add more hauling capacity, and road permits have increased over time. Keeping up with these industry changes, the 982 still provides two-pass loading. “We refer to it as a true two-pass loader. It has a completely different design than the 980. We have a different frame, a different transmission, there are different rims on that machine," says Schmidtgall. There is a different linkage, as well, which provides a little more dump clearance vs. the 980.
New technology drives efficiency
Where the two machines share commonality is with the technology platform. Perhaps one of the most noteworthy features on these loaders is the Cat Autodig with Auto Set Tires. It promotes proper loading technique to significantly reduce tire slip and loading time. It can automate the complete bucket loading cycle to deliver consistently high bucket fill factors for up to 10% more productivity.Caterpillar
Typically, as the loader enters the pile when loading the bucket, the operator gives a slight lift command to set the tires. “It puts weight on the front axle so the operator has the traction that he needs to get that bucket loaded very efficiently,” notes Schmidtgall. If the operator doesn’t do that and performs a rack-only load, it’s not going to be as efficient.
With Auto Set Tires, if the machine does not see the operator give a lift command, the machine will override that and give a slight lift command to keep a very efficient load. This also eliminates a great deal of tire slippage, which is a large driver of operating cost, including fuel burn.
“Auto Set Tires can be turned on or off through the machine display,” says Schmidtgall. “It will run in the background and only come on when needed.” This helps both novice and expert operators. “These guys know what they are doing, but they get fatigued. They are working long shifts. They can get distracted. This tool will not get in their way. But if they do get distracted or fatigued, it will take over and make sure the operator is being efficient with the cycles.”
Operator ID lets an operator set up preferences. At the end of a shift, another operator may hop in the machine and change the settings. When the original operator comes back, he or she can log in and all the controls will revert back to the preferred settings. This gives the operator confidence that the machine will perform as expected.
The new models also introduce Application-Profiles. The press of one button sets multiple machine parameters to optimize settings for the application at hand. Customized profiles can be created to fit customer-specific cases.
Standard Cat Payload with Assist on all 980 and 982 series loaders provides accurate weighing of bucket payloads so operators can load to target the first time, every time. This technology includes low-lift-weigh and manual tip-off functions.
An optional Cat Advanced Payload expands the system’s functionality with Lists-Management, Multitask- & Manual- Add Modes and Tip-off assist. Compatible with third-party scale house software, it can wirelessly integrate the machine in the scale house process with Dispatch-for-Loading.
Multitask Mode allows the operator to put one task on pause and go to another task. For instance, if you were loading a rail car and then had to pause to load a couple of trucks, you can easily go back to the original task without disruption.
A brand new electronic architecture allows introduction of features such as Remote Flash and Remote Troubleshoot. These remote service technologies can save service trips to the jobsite and ensure the machine operates at peak performance. Remote Troubleshoot connects the machine to the dealer service department over-the-air to quickly diagnose fault codes without on-machine cable connection. “Now, when we dispatch a technician, we will have the right parts, the right tools,” says Cherry.
Remote Flash ensures the wheel loaders are operating with the most up-to-date software. “We are able to update the ECM software on this machine remotely from the dealer with a push of a button,” notes Cherry. “No longer do you have to schedule a technician to come out with a laptop and schedule two or three hours of downtime to update software.”
Update files are pushed to the machine in the background and installation can be initiated by the customer from the Cat Remote Services Portal in a safe manner, reducing impact on production schedules.
Cut fuel use with CVT
On the XE models, a high-efficiency continuously parallel path drive system combines a direct mechanical path from the engine to the wheels with a Hystat variator. Deep systems integration of the Cat CVT, engine, hydraulic and cooling systems significantly improves fuel efficiency up to 35% through lowering the rated engine speed with high rimpull.
The new models feature fine rimpull modulation capability and virtual gears to allow operators a seamless switch from powershift machines. Operating noise levels are also reduced.
“This is the best technology for the application that these medium loaders are running in,” Schmidtgall asserts. “We have upsized the 966 CVT that has been running for over a decade; there are over 3,000 units of that in the field."
Because they run at lower rpm, it means lower fuel burn. To maintain implement speed at low rpm, the implement pump has been upsized.
“You are going to see the biggest benefits in truck loading, but the XE is good across all applications,” says Cherry.
The CVT will simplify operation. “The operator gets in this machine, sets his virtual gear to the max speed he wants to travel and as he approaches the pile, he doesn’t even need to downshift,” says Schmidtgall. “The machine does it. The operator can now focus on implement control, speed and direction. It is simple two-pedal operation inside the cab. It is very easy for a new person to learn and get up to speed.”
He adds, “Because we married the hydraulic and mechanical power path, you get the benefits of both. You have creep control, hill hold, some retarding capability as well as rimpull adjustment. If you are working in soft underfoot conditions, you can dial back that dig effort and still be very efficient with this XE platform.”