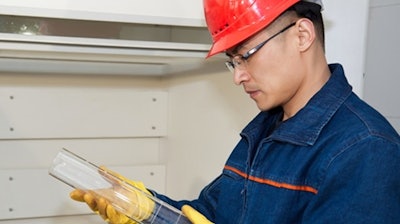
Originally published on Chevron Lube Matters blog
In our previous articles, we explained how to “start clean” with certified clean lubricants and proper handling, and then how to monitor lubricants for contamination on an ongoing basis. Now we will explore how to stay clean — specifically the corrective action you can take on in-service lubricants when contamination levels exceed targets.
Once you have set your corrective action limits it is important to work with your lubricant supplier to setup corrective action plans at the very beginning so the processes and procedures are in-place and ready to be implemented to minimize any potential downtime due to failure. When selecting a third party filtration services company, it is very important to understand how they perform the work as well how the data is reported back to your company.
Particle contamination
When the oil analysis particle count uncovers higher than acceptable particle contamination in equipment oil reservoir, it’s advisable to clean the in-service oil using a kidney loop filtration system. The system takes oil from the reservoir, runs it through the filtration system, then flows it back into the tank in a loop. Typically over multiple passes, the particle level will be lowered below the target level. In many cases this can typically be done while the equipment is in operation. While this may seem like an easy concept, many times these systems are improperly setup and results are not achieved as all the product does not get filtered or additives are removed from the lubricant creating bigger issues. For customers choosing to purchase their own kidney loop systems and manage the project, it is important to procure equipment engineered specifically for their application, in addition to consulting their lubricant supplier who can ensure the proper filter media is used to minimize any damage to the lubricant. For larger system, it is typically more cost-effective to bring in a third party filtration services company to perform the work.
Water
Depending on the system, typically when the water level reaches 50 or 100 ppm it is recommended to perform a corrective action to remove and lower below the target. If there is a high level of water contamination in a larger system, it’s advisable to call in a third party filtration services company to perform the work. While there are different methods for water removal, a typical system used to perform this operation is a Vacuum Dehydration Oil Purification (VDOP) system. For smaller systems with smaller amounts of moisture, customers can possibly use their own in-house kidney loop systems- provided they are equipped with water removal filters. Once again it is always recommended to ensure these systems are setup properly and consult with your lubricants supplier.
Varnish
If oil analysis test results turns up varnish contamination that is above target levels, it is critical to implement a varnish mitigation action plan. Depending on the system and criticality, it is highly recommended to work directly with your lubricant supplier and third party filtration services company since varnish mitigation can be very complex and can be performed by a couple different methods. One method, is to chemically treat the system and then remove the varnish through a flushing and filtration process with a possible reservoir cleaning. It is also possible to utilize an electrostatic filtration system or special filter media to remove varnish during operation. Typically, the lubricant is fully analyzed and the system operation is observed via a site assessment before the appropriate method is recommended.
A systematic lubrication management program, following the three phases we’ve outlined in this series, will help prevent equipment damage from contamination in lubricants, resulting in better equipment reliability, less unplanned downtime and longer component life. It is always recommended to consult your lubricant supplier when setting up a proactive maintenance program to minimize contamination.
Jason Gerig is currently the Americas ISOCLEAN Business Manager for Chevron Lubricants where he is implementing an industry leading business model for certified clean lubricants. He has 23 years of experience in the lubricants and fuel industry holding various positions in operations management, marketing, and sales with his primary passion focused on equipment reliability utilizing certified clean lubricants. He holds a B.S. degree in Business Marketing from the University of Wyoming and has been recognized by the Society of Tribologists and Lubricant Engineers as a Certified Lubricant Specialist and Oil Monitoring Analyst.