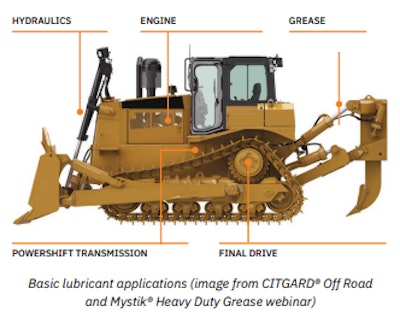
As equipment costs continue to rise — now more than 30% higher than pre-COVID levels, according to the Associated Builders and Contractors — construction companies are reevaluating how to protect and maintain their investments. One key area gaining renewed attention: lubrication. Often seen as a routine maintenance task, proper lubrication is increasingly viewed as a critical strategy to reduce downtime, extend machinery lifespan and control operating expenses.
Why Lubrication Matters
Effective lubrication helps shield machinery from damaging contaminants like dust, dirt and moisture. It plays a direct role in minimizing wear, preventing breakdowns and improving operational efficiency. Rather than waiting for equipment failures, companies can take a proactive approach to lubrication that helps avoid costly repairs and supports consistent productivity.
Key Elements of a Proactive Lubrication Program
1. Choosing the Right Lubricant
Matching lubricants to equipment specifications and operating conditions is essential. Recommendations from OEM manuals should always guide lubricant selection, and environmental conditions — such as extreme heat or cold — should be factored in. Understanding grease classifications (e.g., NLGI grades) and choosing multi-purpose lubricants can also reduce inventory complexity and risk of misapplication.
2. Applying Grease Properly
Grease can be applied using manual grease guns or automated lubrication systems. Each method has advantages, but both require clear understanding of lubrication points, application frequency and the right amount of grease. Too little increases wear; too much can damage seals and create unnecessary resistance in moving parts.
Automated systems, while requiring more setup, can deliver consistent lubrication with less labor — but they require careful grease selection to ensure smooth flow through narrow lines.
3. Establishing Good Lubrication Practices
Lubrication schedules help ensure regular, balanced maintenance. Over-greasing and under-greasing are common — and costly — issues. Accurate documentation of lubrication points, types and intervals can help avoid both extremes and keep machines running smoothly.
4. Preventing Contamination
Contaminants are a leading cause of lubricant failure. To prevent this:
• Store and handle lubricants properly in sealed, clean containers.
• Use clean tools and grease fittings.
• Label products clearly and avoid mixing incompatible greases or oils.
Routine checks and maintenance of seals also help prevent contaminants from entering systems during operation.
Common Mistakes That Increase Costs
• Using the wrong type of grease or oil for specific applications
• Infrequent lubrication or skipped maintenance intervals
• Introducing contaminants through dirty tools or poor storage
• Over-greasing, which can damage components and reduce efficiency
Case in Point: Frattalone Companies
A construction company managing over 300 machines, Frattalone Companies, saw measurable improvements after optimizing their lubrication strategy. With updated grease and engine oil selections, they experienced reduced wear, longer oil drain intervals and better fuel efficiency. The result: lower maintenance costs, improved uptime and longer equipment life.
Final Thoughts
Lubrication is more than a box to check — it's a key part of maintaining uptime and protecting valuable machinery. By selecting the right lubricants, applying them correctly, and preventing contamination, construction companies can significantly cut maintenance costs and extend equipment life.
A strategic lubrication program isn’t just smart maintenance — it’s a smart business move.