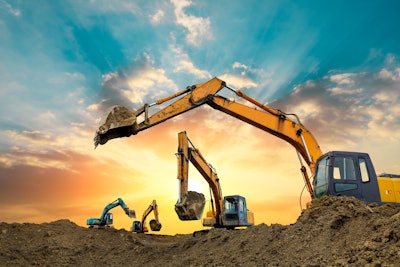
Operational costs keep rising; the costs of fuel, transportation and of course maintenance. Many finance departments have been looking at ways to reduce overall costs and usually, the operational department of most companies are the ones taking the hit. This can affect the availability of emergency repair parts or reduced maintenance schedules. What if we found a way to keep the costs down while increasing revenue? Sounds like every finance department’s dream!
Who Is The Biggest Culprit?
If we looked at a typical budget for a fleet of trucks or mobile equipment within the construction industry, we would see a trend of which products/services are the largest consumers of budget. We evaluated several sources to determine the largest budget consumer and in most cases, Fuel (marked as Energy in Figure 1) was a very high consumable (as also seen in Figure 2).
Figure 1: Comparison of the TCO for an Agricultural telehandler vs a skid steer loader for construction ((MANITOU GROUP, Reduce TCO: What is the TCO? 2018).Strategic Reliability Solutions Ltd.
Figure 2: TCO for Heavy Duty Vehicles (Çakmak, Tolga & Oter, Z & Surmen, O. (2021).)Strategic Reliability Solutions Ltd.
Interestingly enough, lubricants are not listed on these charts yet this is one of the areas lots of maintenance managers are asked to reduce the overall cost. Usually, this means using a cheaper lubricant which may not protect the engines or equipment for the extended time that a premium lubricant would have done. In the long term, this ends up costing the finance team quite a bit of headache as they now have to order more replacements parts, trucks have to be pulled off jobs to be serviced and there are a lot of unexpected breakdowns. Which in turn leads to poor reliability for the fleet owner and this can result in delays on projects and creating a bad reputation. Nobody wants that to happen.
When we look closer at the figures above, we can see that fuel accounts for more than 30% of the budgets, hence if we can reduce this sector, we can help to save some costs. But how can we reduce the amount of fuel being used if each piece of equipment has specific volumes of fuel which need to be used? This is where selecting the right lubricant for your fleet can make an impact.
Selecting The Right Lubricant: Mineral vs. Synthetic
One of the biggest debates, especially for mixed fleets, is whether one type of oil should be used throughout or not. The second biggest debate is whether this should be mineral or synthetic. Let’s take a closer look at these two debates and what either of them can mean for the fleet.
Can One Oil Be Used For The Entire Fleet?
If you are like most fleet owners in the construction industry, then you will have a very mixed fleet of equipment. These can include excavators which were bought five years ago to trucks which started off your business 20 years ago. Purchasing consumable items in bulk often helps to reduce some costs but is it a wise decision when trying to efficiently manage your mixed fleet?
The first factor that you should consider before jumping to any conclusions is the health of your engines and their requirements. Diesel engines have not evolved as much or as rapidly as gasoline engines over the past 50 years. So, the chances are that most of your fleet may be able to use the same lubricant.
One of the good things about diesel engine lubricants is that they all must adhere to the American Petroleum Institute (API) specifications. These specs allow all oils to be backward compatible, which means that a CI oil can be compatible with a CJ oil and vice versa.
Another noteworthy observation is that diesel engine oils have stayed within the 15w40 range for quite a few years. Only recently in the last decade or so have we started to see a move towards lighter oils such as the 5w30s or even 0w20s. Let’s be clear, those straight 50s have not been used for decades!
When trying to decide if you can use one type of diesel engine oil for your fleet, you should ideally develop a register of your equipment. Next, list out the types of engines (Manufacturer and model number) for each. Afterwards, identify the OEM recommended oil (usually, they will list a number of brands, but they also list the specifications).
Afterwards, group the engines which require the same specifications. This helps you to easily determine the requirements of each group. Now, we’ve got some data to work with!
A higher spec oil such as a CJ oil may meet (and exceed) the requirements for a lower spec oil. As such, the CJ oil can be used across various pieces of equipment, once they all have similar specifications. It is a good idea to liaise with your OEM before attempting to convert the entire fleet. This way, one oil can possibly be sued across your mixed fleet.
Mineral or Synthetic?
This age oil question has troubled many operators and caused them to get into heated arguments with the finance department. It’s no secret that synthetic oils are more expensive than mineral oils….for the initial purchase. When the benefits of synthetic oil are weighed against that of a mineral oil over the course of its lifespan, the synthetic oils usually are less expensive.
Imagine walking along a road with uneven stones, all shaped differently with varying textures. This may be a bit difficult to walk on compared to walking over a tiled surface. We can think about mineral oils as that uneven surface as mineral oils are refined from the earth and all of their molecules are varying sizes. On the other hand, synthetic oils all have a uniform structure (similar to the tiled floor) which allow easier walking.
If we correlate this to the insides of the engine, ideally it will be better for a synthetic lubricant to be used instead of a mineral as the synthetic lubricant will provide a more protection on the inside of the engine. Additionally, synthetic oils have been designed to withstand higher temperatures than mineral oils. We know that diesel engines run hot, and these synthetic oils can help to regulate these temperatures.
Some synthetic oils can provide longer oil drain intervals (which should be confirmed with the OEM). These longer oil drain intervals can help to save costs in various areas of the maintenance budget mentioned earlier. Let’s explore this a bit further.
What Does a Longer Oil Drain Interval Really Mean?
The industry seems torn on whether a longer oil drain interval for mixed fleets can positively impact their availability and the bottom line of revenue. If we follow the money trail, these longer intervals can indeed increase the amount of time that the equipment is available to work and thus increase revenue but at what expense?
Creating a Pilot Project
When determining the ideal drain interval for a mixed fleet, one should consider performing a pilot project where at least 10% of the fleet is tested before applying this change to the entire fleet. In selecting the test equipment, one should identify pieces of equipment which have the most strenuous tasks (if we’re talking about trucks, these would be the units which run the most rugged terrains or transport the heaviest loads) and some equipment which carry out average tasks within the fleet.
It would be wise to test the range of ages of equipment (not only the new equipment, but some of the older machines as well). This is where the grouping of the categories which we spoke about earlier would be very useful.
Next, we need to identify what the new targeted range should be, either an increase in the interval by twice the current value or less. We also need to establish if this increase in interval makes an impact to the operations.
One rule of thumb to follow would be to increase the intervals slowly. For example, if the regular oil drain interval for a truck is three months (or 5,000 km), then if we are increasing the interval, we will need to check the health of the oil at every quarter interval. In this case it would mean monitoring the lubricant through oil analysis every three weeks (or 1250km).
With oil analysis, the idea is to develop a trend and monitor that trend. Now, not all pieces of equipment will create the same results (hence it is important to select your test pieces of equipment carefully as they need to represent the fleet). It is also important to be aware of the turn-around times for oil analysis with your lab. If they take longer than the estimated interval, then you may want to consider using a different lab for this project.
Ideally, the parameters to consider when trending the health of the oil for diesel engine oils can be seen below. The warning levels for each of these parameters can differ depending on the type of engine being monitored. However, a general guideline which can be used for these parameters can be seen in table 1 below.
Table 1: Parameters to monitor for diesel engines.Strategic Reliability Solutions Ltd.
Finding the Money
Now that we have been able to establish a pilot program to extend the oil drain intervals, we need to assess the impact costs involved by implementing this program. If we were to use hypothetical values then the simple calculation can be done as shown below.
Assume oil drain interval increased two times the original value (assume new value 6 months) =>
This translates that for one truck, over the period of one year, two oil changes would have been saved.
Assume one oil change includes a new oil filter, new oil, one hour of the mechanic’s time => estimated at $70
Then for one truck, for one year, the savings would be $70 x 2 = $140
Now, apply this to the fleet of 20 trucks = $140 x 20 = $2,800
While this may not seem very significant, we can also include the cost of removing the truck from the roster to perform these oil changes. Each hour that a truck is working can be calculated by estimating it’s average revenue.
For this example, we will use $100 as the cost per hour of pulling a truck off the road.
Therefore, by saving two oil changes per year, per truck, $200 can be saved.
For the entire fleet of 20 trucks this would amount to $4,000.
Therefore, by extending the oil drain intervals for a fleet of 20 trucks, one can potentially save $6,800 per year!
Fuel Efficiency – Synthetic Oils
Another example of following the money can be the switch from mineral to synthetic oils. Synthetic diesel engine oils typically boast of 3% to 5% fuel efficiency. Is this even significant?
Well, based on our figures above where fuel represented an average of 30% of the budget, it can be very significant. If we assume that the budget total was $100,000, then 30% of the budget = $30,000.
If a synthetic oil can give 3% fuel efficiency, then it can save $30,000 x 3% = $9,000.
This is even more than the oil drain intervals above.
Can It Be Done?
The final question is whether this can be applied to your fleet. The short answer is a resounding yes. It is important to seek approvals from the OEM and work directly with your lab to monitor the health of your oil during the trial period. You can save some dollars for your company through small changes which make big impacts.
References
- Çakmak, Tolga & Oter, Z & Surmen, O. (2021). Lightweight innovative composite dry clutch pressure plate. IOP Conference Series: Materials Science and Engineering. 1070. 012117. 10.1088/1757-899X/1070/1/012117. (Accessed November 10, 2023)
- Reduce TCO: What is the TCO? (2018) MANITOU. Available at: https://www.reduce-program.com/en/tco/about (Accessed November 10 2023).