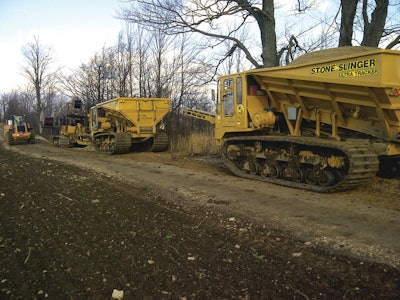
In Jack Kottelenberg’s mind, the last hurdle would be to deliver more sand into the cut quickly, without wasting material. With that piece in place, he would have what he was looking for – a faster, more cost-effective solution for laying down power and ground cables on his customers’ wind farms.
Kottelenberg's family run firm, AVERTEX Utility Solutions Inc., was already established as one of Canada’s top specialists in underground cable contracting for electrical and communications utilities. It is known as an innovator in horizontal drilling technology, and its team has a knack for making new ideas work. Conventional wisdom said they should use open cut trench methods for laying distribution lines into these wind farm grids, but Kottelenberg was convinced that significant cost savings were achievable with the right plow and back-up equipment in place.
The plow system he devised was doing the job, but he still needed a way to deliver a bed of sand in tandem with the plow so he could cushion the cable against any possible backfill damage. For AVERTEX customers, any compromise on the integrity of the installed cable was a deal breaker.
An Unusual Request
The first plan for the plow system relied on a bucket line of backhoes to move sand to the trench. However, they were unable to keep up with the rapid pace set by the plow. Even in open cut trench applications, they poured out too much material.
“It’s hard to dump the sand with any control; you tip the bucket and a bunch more comes out," Kottelenberg notes. "By the time the job’s done, you’ve gone through twice as much material as you needed or estimated for.”
By the time he contacted W.K. Dahms Mfg., maker of the Stone Slinger truck conveyor system, time was becoming critical.
The original Stone Slinger system places various types of aggregates with a high-speed conveyor that can project stone accurately into foundations and trenches at distances up to 100 ft. away. This application called for a new version that could move higher volumes of material, but with equal precision.
“I took the idea to Scott [Nelson, manager of W.K. Dahms] and he looked at me a little crooked," says Kottelenberg. "Then he said, ‘Yeah, I think we can do this.’ And we just started to draft something up.”
More Volume, Speed and Control
The right power unit was needed to carry the conveyor system. The search led to the Morooka 3300 carrier, a 19-ton tracked hauler with a standard dump capacity of up to 7.4 yds.
“We tried a smaller truck,” says Kottelenberg, “but we had issues with parts and the plow was still outrunning the sand. For the wind farm projects, we need something that will float anywhere, on mud and swamps, and that can run on roads, as well. The ground pressure on the Morooka carrier is minimal, even when it’s fully loaded, and the rubber tracks will go wherever we need it.”
To fit the carrier platform, Nelson had to completely reconfigure the standard Stone Slinger assembly. “The carrier follows the plow and discharges out the front of the vehicle from a range of about 15 ft. Any other Stone Slinger truck unloads from the back or the side," Nelson explains. "Our initial version for AVERTEX worked better than the backhoes, but Jack told us he still needed more, faster. We fitted the next version of the system with a larger discharge. It can now unload 30 tons of sand in five or six minutes.”
With four of the customized Morooka units now in the field, Kottelenberg and Nelson have continued to refine the Stone Slinger system. The latest design adds a rear conveyor gate that will discharge a full load in as little as two minutes. The center of balance has been moved forward to improve traction as the load comes off the front of the dump box.
Kottelenberg identified improvements to the operator controls needed for greater accuracy, plus added backup safety cameras for improved visibility behind and to the sides. Nelson also upgraded a CANbus panel to control all hydraulic and operating functions.
To simplify service access to the powertrain, Nelson mounted the entire conveyor and box assembly so technicians can raise it up as a single unit on a rear pivot.
One-of-a-kind Solution
Since the prototype unit first rolled out, AVERTEX has completed several wind farm projects. Kottelenberg estimates he has put a total of 1.5 million meters of cable in the ground. The company has deployed the Morooka Stone Slinger to other projects, as well, including installing gas lines for a landfill site and placing granular into trenches along railroad beds.
The Stone Slinger system has provided AVERTEX with a one-of-a-kind solution in a challenging niche market. Kottelenberg is pleased with his company’s investment.
“This is how all things get developed, right?” he remarks. “You have a need out in the field, you want to save manpower, save sand, save costs… Sometimes spending money on new equipment is the way to do it. Now our customers have seen what we can do, and that’s what they can now expect.”