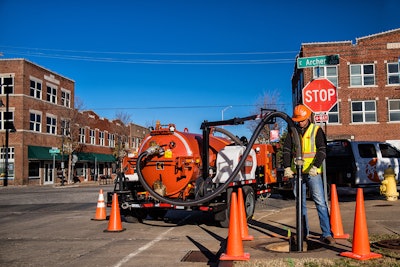
When selecting utility equipment, locating systems continue to evolve to help contractors identify interference & accurately locate underground utilities amid it
Every few minutes, an underground utility line is damaged by excavation activity, putting public safety at risk, disconnecting communities and businesses from vital services, according to “Buried Risks: Protecting Underground Utilities During Construction” from Common Ground Alliance.
With different state regulations and dig laws lacking strong enforcement, some professional excavators opt to dig without following their state’s 811 law. They do this to avoid slowdowns and hit production goals.
Utility strikes have potentially significant consequences, including utility service disruptions, costly fines and repairs, severe injury — even death. Recently, excavation activity has increased because of funding from states and the Infrastructure Investment and Jobs Act, with more than $1 trillion in new infrastructure breaking ground across the U.S., according to the U.S. Department of Transportation.
Increase in Underground Infrastructure Damage Rates
According to the latest Damage Information Reporting Tool (DIRT) Report (2022) from the Common Ground Alliance (a trade association of nearly 4,200 excavation professionals and damage prevention professionals), 213,792 unique damages to underground infrastructure were reported. The DIRT Report collects data from all stakeholders — including facility owners, operators, excavators and locators — and compiles that damage information into an annual report that tracks the number of damages and near misses that happen in the country every year, noted Sarah Magruder Lyle, Common Ground Alliance president and CEO.
Lyle said the results of the report make it clear that “damages have been stubbornly stagnant or slightly increasing over the past decade. When the Common Ground Alliance was founded in 2020, a lot of the big issues were addressed immediately, so the low-hanging fruit is gone. Now we’re getting into the more difficult issues.”
Case in point: When 811 was designated as the national one-call number, damages dropped by a significant 50%. “Now we’re getting into more complicated things — in addition, the industry is evolving,” Lyle said. “There is a significant amount of build-out happening in telecom right now because of the influx of money from the bipartisan infrastructure [law].” The juxtaposition of those factors is coming together to cause what Lyle calls a stubborn, consistent number of damages and slight increase. One driving factor is that excavation contractors don’t always call 811. She said that is not an awareness issue. Excavator operators know that they are supposed to call, but they don’t, but why?
Another factor: Not taking care of the jobsite when contractors are on it. “These issues make up 76% of the challenges we see that lead to damages,” Lyle said. “We’ve been looking at why … these challenges [are] consistently happening and causing up to $30 billion annually in cost to communities around the country. That’s a conservative number.”
Addressing the primary challenges contractors face regarding utility work, Lyle noted “we’re still using a system that was created a long time ago and that hasn’t really changed with the industry. The underground world is getting increasingly more congested. There are a lot more companies out there doing work because of this inflow of money.”
Determining why damages are occurring is important. According to Lyle, many of the drivers of damages involves understanding what the initial contract looks like with the operator.
“Are they incentivizing good behavior on the jobsite? Are they incentivizing a ‘stop work’? If something doesn’t seem right, you absolutely [must] wait until everything is located,” Lyle said. “Once the process starts, then you can see where the choke points are and what needs to be addressed.”
Utility Challenges
Utility and general contractors encounter many challenges before digging begins. Identifying safe zones for digging and where trees, shrubs and other brush needs to fall or be placed are among top concerns. “The correct [identification] of hazardous utilities prior to work, what we consider safe zones for the falling of standing trees as well as [the] direction of grinding material are among primary challenges,” said FAE product and application manager Lee Smith.
Accurately detecting and mapping underground utilities, a task complicated by varying soil conditions and the presence of multiple, often undocumented utility lines, is vital, according to Rodolfo Cabello, Subsite product marketing manager, utility locating. “Interference, both passive and active, further complicates this process,” he added.
Passive interference from metal structures — such as chain-link fencing, pipes, rebar, guard rails and underground steel drains or utility vaults — distorting the signal and magnetic field, affecting location and depth estimates, Cabello noted.
“Active interference is generated by objects or infrastructure with live currents, such as power lines, fiber-optic lines, cellular lines, traffic loops and diesel generators,” he said. “These sources can reduce the communication range of locating systems or distort their magnetic fields.” To address these challenges, contractors must follow the established processes for identifying interference and selecting the optimal operating frequency, said Cabello.
“Locate technicians should start with the lowest possible frequency and only increase it if the utility cannot be found,” he added. “Although higher frequencies are easier to detect, they are more susceptible to interference, leading to inaccurate locates.”
Increasingly smaller jobsites are another major challenge, said Chris Thompson, product manager, Ditch Witch. The congestion of underground environments is another.
“As urban areas expand, available space for construction and maintenance shrinks, making it difficult to maneuver equipment and personnel efficiently,” he added.
“With the proliferation of utilities like water, gas, electricity and fiber installation, the underground landscape has become a tangled web,” Thompson said. “This complexity increases the risk of damaging existing utilities during excavation and installation.” The rising demand for horizontal directional drilling (HDD) projects adds another layer of difficulty, he added. “As infrastructure and fiber optic networks expand, HDD becomes more prevalent due to its minimal surface disruption,” Thompson said. “However, this method requires precise planning and execution to avoid complications and ensure successful installations.”
Vacuum excavators are becoming increasingly popular for exposing underground utilities on congested urban projects, said Thompson, adding that their soft excavation technique and versatility allow operators to adapt to different soil conditions, work effectively on compact jobsites and mitigate damage.
Smith noted that “if you are working above or below ground, you need to know your surroundings and the location of all power, water and other utilities — not to mention, in our industry, we often work around homes and roads, so the direction of material is very important as well as always watching out for curious bystanders.”
According to Cabello, to ensure safe and efficient utility work and address many of the challenges, contractors must follow several key steps, including:
- Notify 811 before any excavation begins.
- Once a jobsite has been outlined and utilities marked, contractors should verify the markings with locating technology to fully understand the underground infrastructure.
- Accurately locating and marking utilities before underground work begins is crucial for a successful project, said Cabello, adding that locate technicians must connect their equipment to the utility and select the correct frequency to trace the signal, effectively managing any jobsite interference.
- Proper training is essential to ensure that all operators are proficient with the equipment and understand safety protocols.
- Thorough documentation of all locating activities is necessary for future reference and compliance.
- Regular maintenance and calibration of the locating equipment ensures accuracy and reliability.
- Have an emergency response plan in place in case of accidental utility strikes or other incidents.
“By adhering to these steps, contractors can avoid costly and dangerous utility strikes, maintain project efficiency, and comply with industry standards,” Cabello said.
Utility Technology Options
Several technologies are available to assist with safely excavating around utilities and locating the lines to avoid them.
Vacuum Excavators
Thompson says that once utilities are accurately located, vacuum excavators can be used to safely expose them, starting with a small excavation and expanding as needed, he said. This equipment offers a more controlled and precise approach when compared to traditional shovels, excavators or backhoes.
“These machines are essential for damage prevention, particularly in congested underground environments,” he said. “By using a process known as potholing, vacuum excavators [use] a soft excavation method to create holes and remove debris to visually expose existing utilities, minimizing the risk of damaging them.”
Thompson recommended keeping the nozzle moving and maintaining a distance of 6 inches to 8 inches from the utility to prevent damage.
“Using an oscillating nozzle for hydro excavation ensures even water distribution, which can cause costly downtime,” he said. “Never use the nozzle as a shovel to dig, as this increases the risk of damage and inefficiency.”
Adapting to soil conditions is also essential. “Choose between hydro or air excavation based on the specific soil conditions of the jobsite,” Thompson noted. “Hydro excavation is highly versatile and suitable for a range of soil conditions, including tightly compacted and hard soil, cobble and clay. “This method requires water for operation and the disposal of liquid spoils, making water conservation practices essential. Despite these requirements, its ability to handle [different] soil types quickly makes it a preferred choice for many contractors.”
On the other hand, air excavation uses compressed air to break up soil and vacuum dry spoils, which can be reused as backfill in most cases, Thompson added. “It is most effective in softer soils like topsoil and sand,” he said. “Air excavation eliminates … water, keeping machines operational onsite without the need for water replenishment or liquid spoil disposal.
“This method is increasingly popular as disposal restrictions for liquid spoils tighten, and certified disposal sites become scarce.”
Manufacturers design vacuum excavators with both air- and hydro-excavation capabilities, offering dual functionality, according to Thompson. That allows operators to start with air excavation for softer soils and switch to hydro-excavation for harder soil formations.
“Such adaptability ensures continuous productivity across
varying ground conditions, making these machines versatile and efficient,” he said.
GIS Mapping
Geographic information system (GIS) mapping is being used in some places but not to its full potential, Lyle said.
Cabello noted an increase in digitized mapping and asset inventory, enabling the integration of this data with GIS platforms for streamlined future projects.
“Today’s utility location devices can share data with stakeholders, logging attributes — such as location, depth and utility type — and transmitting this information wirelessly in non-proprietary formats like KMZ and CSV,” he said.
“Their precision locating capabilities, high storage capacity and integration with third-party mapping and GIS technologies make it easy to generate highly accurate maps. These maps can be another data point to help contractors combat interference. They also meet the requirements of a growing number of municipalities that want to create and maintain digital records of their underground utilities.”
Depending on the project’s needs, locators can use equipment with survey-grade accuracy, said Cabello.
“By applying a signal directly to conductive utilities or using beacons for non-conductive ones, locators can verify utility paths with handheld receivers,” he said.
Subsite’s Utiliguard 2 RTK receiver uses survey-grade technology. It features dual-band antennas designed to provide operators with accurate and reliable positioning data with centimeter-grade accuracy.
“Its high level of accuracy and precision make it an ideal solution for locating abandoned and untracked utilities that are often difficult to pinpoint,” said Cabello. “By quickly verifying the utilities installed, operators can efficiently tailor their bids to match jobsite needs as well as gain insight into the underground infrastructure to avoid cross bores during future projects.”
FAE offers a hydraulic-driven mulching door that allows the operator to better control the direction of the material being mulched, sending it to the ground and away from homes, roads or other possible hazards, Smith said.
Selecting Utility Equipment
The factors to consider when choosing the right equipment and utility technology from among the many options differ from contractor to contractor. Some of the considerations include what they’re putting in the ground and what regulations permit, Lyle noted.
“There are some interesting technologies where the equipment can detect if you’re getting too close to an asset and the actual bucket will stop,” she said. “There are a lot of advancements in technology where the equipment [can] be fail-safe. There’s also the ability in a lot of this equipment to program it with the GIS mapping so it does the work for you.”
According to Lyle, the challenge in some cases is that objects are underground that no one knows the exact location because of historical reasons.
“At some point, we have to decide that, as we find it, we’ll map it,” she said. “But as we’re putting things in the ground now, we are going to make sure that they can be GIS mapped.”
Regional considerations are in place as well. A lot of places are starting to install underground powerlines to reduce the risk of natural disasters, hurricanes, flooding and fires. Placing them underground also increases their resilience and reliability, Lyle said.
The challenge with this is companies are spending money to put the lines underground and make them more reliable and resilient. However, little is being done to protect them from those who are digging around them. “It doesn’t really make a lot of sense to do that,” Lyle added.
“It’s a lot easier to replace an overhead line than an underground line. But the underground line is actually more protected unless we don’t adhere to the damage prevention process.”
Severed lines may become an emergency requiring first responders, evacuations and the closing of schools and businesses, Lyle noted.
“If you hit a fiber line and knock service out to half a city block, all of those businesses are done for the day,” she said. “The emissions piece is a challenge even if you don’t hit a gas line. As we push the move toward cleaner energy resources … those [energy sources, like hydrogen,] can be very dangerous if those lines are ruptured. If we really want to pursue the clean energy opportunity, we [must] double down on keeping them safe.”
Lyle said that more than half the time, an excavator cannot legally start work because an area hasn’t been located within the required time. The contractor endeavors to decide whether to put the shovel in the ground or sit idle and may reason that underground objects may not be located at all and would have to take a risk to get the job done.
In examining the jobsite factors to consider when choosing the ideal equipment and technology, Smith noted three major considerations:
- Consider the size of the area in which a contractor will be working to choose the correct unit that can work in that space safely and efficiently.
- Consider the size of the material that the contractor will be working with to be able to use the proper attachment — whether it is mulching or subsoil work. “You want a machine that can handle the capacity of the material efficiently, but you do not want to bring in a machine that is oversized due to space and cost,” Smith said.
- Ensure that the machines being chosen have the proper tooling and safety systems needed, such as the proper teeth and blades to handle the material, hydraulic hood and a guide frame for controlling the materials and the standing material as it is felled. “The hydraulic hood also helps [during] subsoil work to stop material from shooting out as you grind [and ensuring] an even, smooth finished product,” Smith said.
When selecting utility equipment, locating systems continue to evolve to help contractors identify interference and accurately locate underground utilities amid it, according to Cabello.
“Today’s locating systems are designed to help contractors accurately identify underground utilities and manage interference,” he noted. “[They] offer multiple frequencies for various jobsites and achieve centimeter-grade accuracy for pinpointing difficult lines, such as abandoned or untracked utilities.
“Ambient interference measurement technology scans the jobsite for noise and recommends the best frequency to use. Direction-enabled capabilities allow operators to set a reference on targeted utility lines, alerting them if they stray onto adjacent lines, which is useful in complex sites with multiple utilities.”
The complexity of the underground environment should guide selecting utility equipment, Thompson noted.
“Congested areas with multiple utilities demand equipment that can navigate and excavate with minimal risk of damage,” he said.
“Selecting the right equipment and utility technology hinges on a comprehensive understanding of the jobsite and its unique challenges,” Thompson said.
“By considering factors like ground conditions and the density of underground utilities, contractors can make informed decisions that enhance safety, efficiency and overall project success.”