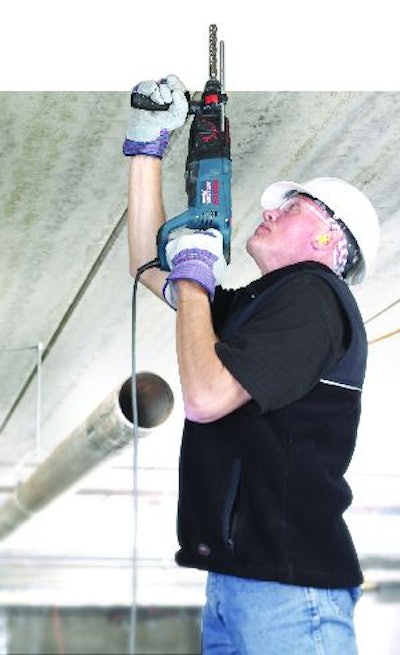
Rotary hammers are a staple of many a building project. While typically found drilling holes of varying sizes and at all angles, larger combination models may also be used to hammer or chip away at concrete and other materials on site.
Because these hammers can be called upon to drill dozens of holes a day, five or more days a week, through concrete, brick, masonry, wood or even steel, suppliers have been driven to produce models that are not only compact and lightweight, but ergonomically friendly and highly durable. As a result, today's models are packing a lot more power, performance and longevity into smaller, more user-friendly packages.
Leaner and meaner
The lighter weight and compact size of today's rotary hammers are attributed in part to changes in the materials used in their construction. "The components we're using to generate the power and performance we're getting today are oftentimes lighter than they were previously," says Jon Goebel, associate product manager - hammers, DEWALT.
For example, in the SDS max size class (1 1/2- to 1 9/16-in. category), alternative materials, such as magnesium gear cases, are contributing to reduced overall weight.
Even in the SDS size (roughly 1 1/8-in. and below), weight has been reduced. "The hammers have gotten [lighter] - under 8 lbs. - but it's a hammer that's still capable of drilling up to a 1-in. hole," says Eric Fernandes, group product manager - concrete, Milwaukee Electric. "You're seeing power-to-weight ratios improve dramatically through the use of alternative materials."
Advances in design have also enabled the use of smaller motors. "We're able to pack more powerful motors in a compact tool than we have in the past," Goebel notes. "We're able to pack more copper into the actual design of the motor, which certainly contributes to the fact that compact hammers can perform at a higher level than they did previously."
Further enhancing performance is improved control of drilling speed. According to Mitch Burdick, product manager - concrete products, Bosch Power Tools, the ability to drill faster has always been a priority for end users. But drilling faster means more than just translating the rpms of the motor into rpms at the bit. "What's changed over the years is tools are a little bit faster - not necessarily in rpms, but they remove the material faster," he explains. "It's the balance of hitting harder and drilling speed."
Some larger models offer more control over impact energy and blows per minute (bpm). This can be important in certain applications.
Fernandes cites drilling a through-hole in an 8-in. wall, as an example. "When you come near the end of that hole, it's important to be able to dial down the impact energy with the speed control, so that as you go through, it doesn't blow out the wall," he says. "From a productivity standpoint, if you can minimize that blowout, there's less repair and patch work you have to do at the end of the job."
Speed control can also help to maintain constant rpm and torque throughout the drilling process. "Essentially, the deeper you drill the hole, you're not drilling at 75% of your speed vs. what you started," Fernandes explains. "So it's being able to complete the hole quickly."
Mechanics of the hammer
A rotary hammer mechanism essentially consists of a piston that moves back and forth to compress air in the hammer tube, creating sufficient pressure to drive a metal cylinder, or ram. The ram, in turn, impacts a striker pin, which then impacts the bit, driving it into the material.
The primary focus when designing these mechanisms is to generate the maximum amount of energy from a small system. "[Manufacturers are] trying to minimize the size and mass... but at the same time, maximize the efficiency of the whole process. So that as you make the tools a little bit smaller, you don't sacrifice performance," states Burdick, "and in some cases, you actually improve performance."
Getting optimum performance out of a smaller package requires a careful balancing act. "How the motor spins; how the connecting rod and piston interface with the striker pin and the tool holder; the machining tolerances of all these pieces; where the holes are in the tubes, which allow air pressure in and out - all this has been balanced over time to produce a mechanism that provides the power with minimal loss of energy," Burdick states. "All these different parts are working in unison to minimize the energy loss and maximize that impact energy."
In some cases, this may actually mean increasing the size/volume of certain components, while reducing the size/volume of others. For example, DEWALT and Milwaukee Electric both incorporate larger rams in their hammer mechanism.
"We incorporate large rams so that as they move forward, they translate a lot of that energy to the striker and into the bit," Fernandes explains. "If you make the ram another gram heavier, or increase the velocity with which the piston moves, it can also affect the impact energy. So we can optimize the way the system is working together."
The result of such optimized system interaction is more efficient delivery of power to the bit. "The hammer mechanisms are much more efficient than they used to be in the past five or 10 years," Goebel asserts. "In other words, if a tool is rated at 2.5 ft.-lbs. of impact energy... they're actually able to generate 2.5 ft.-lbs. every time the hammer mechanism works, or every beat that a hammer generates."
Built to last
Durability is a major concern with rotary hammers. "On a commercial jobsite, the tools can, unfortunately, get abused, either on the job or when they're stored and moved around," says Fernandes. "So durability is key."
The use of lighter weight, yet stronger materials is facilitating added uptime. "Through the use of glass-filled nylon [and other] materials like that, you can make them lighter and more efficient," says Burdick, "but you still maintain the best durability possible."
Internal components of the hammer are perhaps the most prone to damage. "Rotary hammers are, by their very nature, very destructive tools internally," says Fernandes.
By boosting the size/volume of select components, manufacturers are adding toughness internally, as well. For example, DEWALT incorporates both a larger piston and ram in its hammer mechanisms. "Not only are they larger, but the components are more durable," Goebel states.
Seals to keep out dust also reduce component wear and tear. "All of these hammers are used in environments where they're very susceptible to dust and debris getting into the internal components of the tool - specifically, the hammer mechanism - and wreaking havoc," says Goebel. "We use three major dust seals to keep all of that dust and contamination out."
Even features intended to optimize drilling performance can serve a dual purpose by reducing wear and tear. For example, improved speed control can reduce the risk of the hammer beating itself apart.
"If you have a compact hammer that beats at, say, 7,000 bpm, it's beating very fast in rapid succession. That really compromises the durability of the hammer mechanism," says Goebel. "Our approach has been to slow down those bpms, because we know the wear that it puts on the ram and the piston of the hammer mechanism."
Rather than beating more often, the hammer puts more force behind every blow. "That's how we've been able to achieve optimum drilling performance," says Goebel.
Comfort's role in productivity
Productivity isn't limited to hammer performance. It also depends on how comfortable the user is running the tool over the course of the day.
"Users are looking for a lightweight tool that hits hard and is easy to control," says Fernandes. "What I mean by that is they can hold the tool comfortably in multiple different orientations."
This is largely dependent on balance between the weight, size and shape of the hammer. "If you can get it a little bit smaller, a little bit lighter... it all translates into better user comfort over time," says Burdick. "The key is to make them as compact as possible so that the weight of the tool is more evenly distributed, and is more comfortable to the user when he's working all day."
Handle design has a big influence on user comfort. Many handles found on today's rotary hammers incorporate comfort features such as soft grips, ergonomic shapes and adjustable placement. Consequently, the design emphasis is now shifting to vibration control.
Manufacturers have already incorporated anti-vibration technology into many larger rotary hammer models. "The larger hammers have impact energies starting around
8 ft.-lbs. going all the way up to 20 ft.-lbs.," Fernandes notes. "And at the same point, they impact anywhere from 1,000 to 3,400 times per minute. That's a lot of impacts for your body to feel."
With these tools, vibration control tends to be centered in the handles, although the technology is quickly evolving.
For example, Milwaukee Electric incorporates a series of dampeners, springs and shock absorbers in its handle design. "Our handle actually pivots as you're drilling, so that impact energy is directed down through the bit and not up into the operator's hand, wrist, elbow and shoulder," Fernandes explains. "Over the course of an 8-hour day and, more importantly, over a five-day work week, those impact energies are not subjecting the user to a lot of deteriorating energy that could hurt them over a period of time."
DEWALT's SHOCKS Active Vibration Control includes shock-mounted rubber-coated handles to reduce vibration. "Basically, the hammer has multiple springs that absorb the majority of the vibration that someone would experience if they are using a large hammer with a fixed handle," Goebel points out.
Bosch utilizes isolation of the main handle to reduce vibration on most of its models. However, it recently introduced a new concept in vibration control with its 38-lb. Jack mid-size breaker/hammer.
"Rather than add components to counter balance vibration, our engineering group looked at the hammer mechanism itself, and optimized the length of the mechanism and the length of the stroke of the piston," says Burdick. "Through that design, we were able to achieve half the vibration of other tools."
Anti-vibration technology found on the larger rotary hammers is just now starting to trickle down into smaller models. Consider the 5363 from Milwaukee Electric. "It's unique in the industry in that it's the only SDS hammer with an anti-vibration system built into it," claims Fernandes. "The 5363 has a handle with a shock absorber built into it that minimizes the vibration felt by the user, and actually makes the hammer more efficient."
Goebel foresees such vibration control becoming more prevalent in smaller rotary hammer designs in the near future. "It kind of naturally started with the larger hammers," he notes, "and it's moving its way to the smaller hammers."