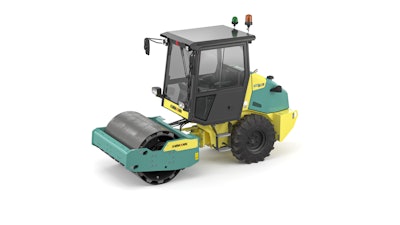
The ARS 50 single drum roller is capable of compacting a wide range of materials. Due to its compaction power and maneuverability, the machine can be used in small landscaping projects, forest roads, municipal roads and walking or bicycle paths.
The ARS 50 is equipped with Kubota V2403-CR-T diesel engines with EGR+DOC+DPF (without SCR) after-treatment technology. Engine power output is 43.2 kW (58 hp). The engines meet the latest emissions standards (U.S. EPA Tier 4f and EU Stage V).
A combination of a well-balanced engine, fully hydrostatic drive system and control enables the rollers to consume fuel at a rate of 5 liters (1.32 gallons) per hour. With a large fuel tank of 98 liters (25.8 gallons), the roller only needs to be fueled once every three working shifts.
Compaction Features
The working width of the ARS 50 is 1,400 mm (55.1-in.) with a boosted single-stage vibratory system with two frequencies. It provides compaction power of 53 kN and 85 kN.
The ARS 50 drum is 18 mm (0.7-in.) thick. The roller is available with a padfoot (PD) drum (with a smooth shell kit) and a dozer blade.
ECOdrop
The ECOdrop on the ARS 50 offers:
- Fuel economy and low fuel consumption due to EcoMode
- A maintenance-free vibratory system with lifetime grease bath instead of oil bath
- A lifetime maintenance-free steering joint with bearings placed in cage storage
- No drive gearboxes – no gear oil needed
No Rear-axle
Elimination of the rear axle makes the rollers more compact and enables a lower engine location that improves the center of gravity – which provides stability, even on slopes.
ACEforce System
Also available for installation is the ACEforce system, which enables operators to easily monitor compaction progress. The Intelligent Compaction system shows the actual kB value on the display, reducing the time required to achieve maximum compaction.
An optional telematics system can help monitor the machine’s position, assist with control and provide jobsite information. All the data can be monitored via the web.
Other Features
Standard Twin-lock drive improves traction and reduces slipping of axles. The fully automatic traction control system is activated without electronic controls. The system adjusts the drive performance depending on actual jobsite conditions. Torque is uniformly distributed into axles for ground contact and to prevent slipping of the front drum and rear wheels, which promotes the quality of the final compacted surface.
A new articulated joint boost drives performance and stability. The central steering joint with integrated oscillation connects components and facilitates balanced weight distribution and consistent ground contact. The hydrostatic power train and articulation joint are maintenance-free.
An operator station with a wide-opening entrance provides unrestricted access to the cab. All control switches are accessible and visible. A multi-functional control display is located on the main dashboard for operators to monitor. The machine design keeps all objects visible to the operator.
An engine compartment that is accessible with a heavy-duty design protects all major components during operation. All maintenance and servicing points can be reached from the ground. The compactor is equipped with external draining points for operating fluids, such as engine oil or cooling liquids.