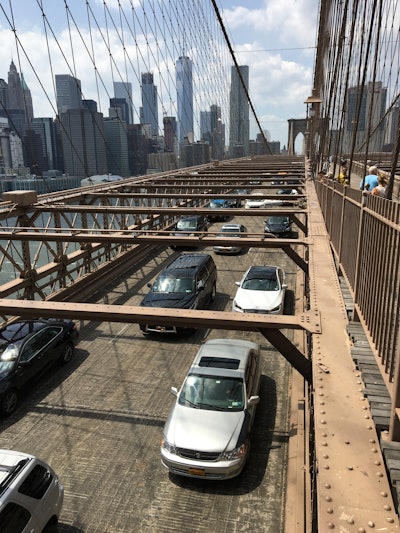
So, here’s the challenge: A micro-surfacing contractor and emulsion producer was tasked with repaving the high-profile, heavily trafficked Brooklyn Bridge deck over the course of six nights during cool weather conditions, with limited paving hours and a heavy application required.
The project presented the following unique challenges:
Limited Paving Hours
Work could not begin until 10:00 p.m. with approximately two hours of prep work (to cover expansion joints and drain inlets) required each night before resurfacing could begin. All covers had to be removed and traffic markings installed before re-opening to traffic by 5:30 a.m.
Nighttime and Cool Paving Conditions
Micro-surfacing had to be done at night in high humidity and cool temperatures. Ambient temperatures were in the low to mid 60s °F with a relative humidity of greater than 80%. Bridge deck surface temperatures were cool, in the upper 50s to low 60s.
Cooler, more humid conditions are typically more challenging because it generally takes longer after micro-surfacing before the road can be re-opened to traffic. This is because at night and in cool conditions, the micro-surfacing needs more time to set, cure and develop sufficient strength before traffic can return to the road.
As a result, the contractor must stop paving much sooner than normal, sometimes up to a few hours in advance of opening the road to traffic, further limiting available micro-surfacing hours. This leads to slower production rates and reduced operational efficiency.
Double Application
The Brooklyn Bridge application was a double lift, with each lift consisting of 28 lbs. of mix per square yard for a total of 56 lbs. per square yard. A tack coat was applied to the concrete bridge deck substrate that had exposed rebar prior to the micro-surfacing paving.
Use of tack coat and a heavy micro-surfacing application traditionally requires more time after paving before the road can be opened to traffic. A thicker application takes longer to set, cure and develop strength, slowing production and operational efficiency.
Traffic Volume
The Brooklyn Bridge is 3,500 feet long and 30 feet wide, with three lanes of travel in each direction and an Annual Average Daily Traffic (AADT) count of approximately 150,000 cars.
Micro-surfacing done at night and in cool conditions can sometimes be more susceptible to early traffic damage and loss of stone. An AADT of 150,000 cars is very high, so the micro-surfacing must cure and develop significant strength before traffic return otherwise excess damage could occur, in which case the contractor would have to remove the application and re-do the paving at their own expense.
The Solution
After reviewing the project goals and challenges, the contractor and emulsion producer turned to Road Science, which simulated expected field paving conditions in its laboratory and measured key performance characteristics of the micro-surfacing using different emulsifier chemistries.
Road Science determined that a specific emulsifier (ArrTekk® 1295) would enable the contractor to meet the job challenges and complete it on time under the restrictive time and weather conditions. The emulsifier is designed to lengthen the micro-surfacing life cycle by up to 30% and improve mix consistency and lay-down characteristics, enabling better workmanship and aesthetics. It also would enable the contractor to open the bridge to traffic quicker, allowing the contractor to pave faster and increase production rates. After reviewing options, the contractor chose ArrTekk 1295 to formulate the emulsion and complete the micro-surfacing mix design.
Did it Work?
In a word, yes. The micro-surfacing mix design, relying on the special emulsifier chemistry, enabled the contractor to meet the tight project schedule because it provided:
· A quicker set time – less than 7 minutes for a 40%+ faster rate
· A 50% reduction in additional water added to the mix to achieve proper mix consistency
· Stronger cohesive strength build allowing for earlier pneumatic rolling of material under cool ambient and surface temperatures – 20 minutes after placement until pneumatic rolling vs. 45-60 minutes typically required
· The contractor exceeding the anticipated project schedule by allowing for more paving time within the short lane-closure timeframes, and sufficient curing to facilitate placement of pavement markings and on-time traffic return
· Project completion within 4½ nights vs. the 6 nights allotted.
ArrTekk 1295 can also be used in micro-surfacing applications including those over asphalt pavements and in crack relief interlayer applications.
Information for this article was provided by ArrMaz’s Road Science division, which develops higher-performing asphalt chemicals, binders, and preventive maintenance and recycling technologies; www.roadscience.net.