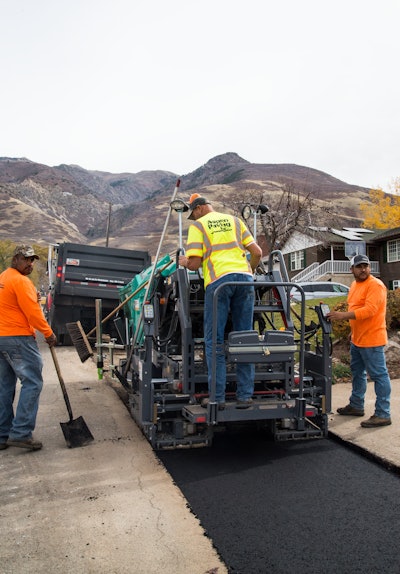
From the East Coast to the far West, commercial contractors are learning that a single paver can give them the means to tackle paving projects from bike paths, to shoulders, to utility cuts, to parking lots, and even residential streets and country roads.
In late October 2017 in South Ogden, UT, Aspen Paving Inc. used its new paver to place a 6-ft.-wide walking/biking path 3-in. deep in a subdivision under construction. Aspen then trailered the paver to south Ogden where it paved a 6-ft.-wide secondary water line cut faster, and with more precision and smoothness, than the toss-and-roll method the firm previously used.
On the other side of the country, Rivers Construction Group Ltd., a utility contractor based in Jessup, MD, used its new cold mill and the same model small paver to finish underground pipe work in Bethesda.
The message? The versatility of today’s commercial paving equipment can help make contractors a more reliable problem-solver for their customers – while at the same time providing improved performance and greater productivity.
Aspen Paving
Started in 1999, Aspen Paving, Ogden, UT, relies on a small crew to pave everything from driveways to paths, parking lots and repairs. So its acquisition of a paver that could pave a variety of jobs was essential.
Bart LaRose, vice president at Aspen Paving, says Aspen bought its paver – a Vögele Super 700-3i – “primarily for paving 8 ft. wide and down," but it was just as effective paving the 6-ft.-wide path. Aspen’s crews used a ½-in. NMAS hot asphalt mix containing 15 percent RAP, placing the mix on a graded berm.
On the 480-ft. long patch for Pineview Water Systems, Aspen’s crews filled a cut which had been backfilled by Pineview following a water line replacement.
"The Super 700-3i will go down narrow enough to go in the cut with its tracks," says Mike LaRose, Aspen project manager. "Anything bigger than 3 ft. is perfect, and anything smaller than 3 ft. is perfect. Three feet itself is tough because you have one track in the trench and one out. That's where the versatility of this paver comes in. We can do a lot of small stuff, but also go up to a 7-ft.-wide trench."
Mike LaRose adds that the paver, acquired in spring 2017, also relieves Aspen of having its crews do extensive work by hand. He says that at first – even with the new paver -- crews leveled placements by hand. But soon Aspen installed an automated grade and slope control system to better refine placements. He says the system is fully integrated into the paver’s ErgoBasic control system and features a separate remote control unit for each side of the screed.
"We did our leveling manually, but with the automated system we now don't have to have two guys on the machine, freeing one up for other work," Bart LaRose said. "We use it on our smaller jobs, as it saves us hand work and gives us a smoother product. It speeds our jobs up quite a bit and improves the quality."
"Anything you do with a paver, versus by hand, will give you a better end result," Mike LaRose says. "That's why we purchased this machine. The system is easier on the guys because they can't crank the screed fast enough, while the automatic system does it for them. Our end result is smoother and our quality is better."
For the Pineview utility cut, Aspen placed a ¾-in. NMAS standard hot asphalt mix containing 5 percent liquid asphalt and 30 percent RAP 6 in. deep in two 3-in. lifts, for a total of 110 tons. The larger aggregate used in the utility patch -- compared to the trail path -- is used to stand up better to vehicular traffic that would not be present on the path.
"That's where this little paver comes in handy," says Mike LaRose. "Because of the grade of the backfill, if we were doing it by hand, the patch surface would stay rough. But the paver will take the roughness out, because the screed blows through the inconsistencies in the grade."
"On the utility patch we are shooting for 95 to 96 percent density," Mike LaRose says. "That's where this little paver helps too; when you place patches with skid steer loaders or hand shovels, you're not getting any initial compaction. But when it's coming out of that vibratory screed, it's getting compaction early on."
Rivers Construction Group
Founded in 2006 by the current president Luis Rivera, his brother Romero (now vice president) with a single helper, Rivers Construction Group now employs 135 people. The contractor specializes in underground utility construction including water mains, water meter vaults, sewers, storm drainage, and concrete flatwork like sidewalks, aprons, curbs, gutters and driveways.
"We concentrate on sewer and water utility construction, roadways and concrete," Rivera said. "In many cases now, instead removing pavement with an excavator, we bring our cold mill in to dig the asphalt out, and then follow with the backhoe to remove fill."
Which is exactly what Rivers did using its new 5-ft. Wirtgen W 150 CFi cold mill to remove a temporary utility patch in advance of final patch placement by the Super 700-3i.
Rivera says the combination of the "compact" cold mill and the paver leveraged time and enhanced profitability for Rivers Construction, in addition providing a better end product.
"They save time and make money for us," Rivera said. "We can do the work faster, and we work to our own schedules, rather than a subcontractor's. They allow us to do three times as much work than before."
When cutting pavement for a utility repair, Rivers relies on the compact mill to cut 10 in. deep. "All we do is reveal the fill surrounding the pipes, and a backhoe finishes the job in advance of the hand work around the pipe," Rivera says.
For placement of the hot mix, Rivers Construction likes to situate its paver with both tracks in the trench. If there's enough room in the road they feed the paver by truck; otherwise, as in the case of Bethesda, they feed the paver by skid steer loader. The mix is compacted to at least 95 percent density with help from the AB 220-3 V vibrating screed.
Typically, if the trench is 8-in. deep, Rivers places 6-in. of asphalt in the trench by loader, compacts it, then follows by placing the final 2-in. driving surface using the paver.
"We can't keep up without the paver," Rivera says. "We will pave about 1,000 linear feet of water main today. There is no way we can do it with excavator and by hand, unless we double or triple the number of people, and we still won't have the quality driving surface we want. With the Super 700-3i we've gone from an average 150 linear feet to 750 feet per day. Everything is better."
And there is a tangential benefit to Rivers Construction upgrading its equipment with the mill and paver. "It also creates respect for us when our customers see the milling machine and paver on the job site. It's completely different from laying asphalt with excavator or shovels. When they see our new equipment their faces change immediately. For us, it's a big, big change and a great benefit."
Tom Kuennen is principal of Expresswaysonline.com, Saukville, WI, and has been writing about the construction and paving industries since 1978. He can be reached at [email protected].