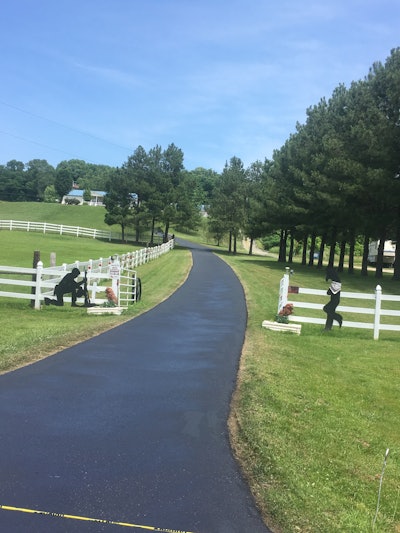
Almost all pavement maintenance jobs have their idiosyncracies – the aspects that make them challenging, problematic and that can impact job quality or profitability.
Warren Johnson, owner of the two-person, part-time ClearChoice Sealing & Striping, recently tackled a 10,000-sq.-ft. driveway job on a hill – and he learned there are ways to improve how work on hill can be done.
“The big challenge with a hill is, it’s a hill!” says Johnson who works the business with his father, Floyd. “There’s a lot of walking with a hill.”
Johnson says sealcoating a hill generally takes more time, which then affects the bid. But the hill also affects the logistics and operations to get the job done. He says he and his father had sealcoated this 575-foot-long driveway (with a 175-ft. hill) once before, walking up and down the hill nine times. This time they were able to reduce that to five trips – but he still logged more than 7 miles walking getting the job finished.
“We did this job once before so that was helpful, so we knew what we did before. We knew what we did and didn’t like about that and what we could do to change the time on the job and save steps,” he says. “We looked at any way we could minimize our walking.
“The biggest improvement we made over the last time was to pull straight up to the top of the hill and do everything from the top down each time,” Johnson says. “Instead of trying to complete each step before moving on to the next part of the process, we completed areas of the driveway before moving on to the next area. This time we made five trips up and down the driveway and we saved three hours.”
Starting a Part-time Business
Started in 2015, ClearChoice Sealing & Striping is based in La Center, KY, a rural area where the nearest big town has a population of only 25,000. ClearChoice does commercial and residential pavement maintenance including sealcoating, cracksealing, patching and striping.
Johnson has a fulltime job as fire chief at Barkley Regional Airport, a job he’s held for three years. He was a firefighter at the airport for four years before that and a volunteer firefighter for 21 years before that.
As fire chief at the airport Johnson works a rotating schedule of four days on and three off, three on and three off and four on and two off and then the schedule repeats. He says that rotation works well for a part-time business.
As part of the job at the airport the firefighting crew is involved in airport operations and does the striping for the airport. Because of his experience striping at the airport, Johnson decided to start a striping company to work on his off days. To learn more he attended his first National Pavement Expo in Nashville in 2015.
“I was taking striping classes and I figured that as long as I’m here I might as well take some other classes,” he says.
He attended sessions by Nick Howell, T & N Asphalt Services, and Wayne Jones, Asphalt Institute, and spent time on the exhibit floor looking at equipment and talking with exhibitors. “I pretty much decided after a day or so at NPE that we should do it all,” he says. “I called my father and I said ‘Dad, I think we should be doing all of this and not just striping’.”
Reducing Trips: Surface Preparation
Reducing the number of trips up and down the driveway was the obvious way of reducing walking and improving their efficiency. Johnson says the way this particular property is laid out enabled them to work from the house down toward the road – but the road was the curve of a busy highway that they wanted to avoid.
The last time ClearChoice sealcoated this driveway they completed each part of their process from top to bottom before moving on to the next step. So, for example, they used a weed eater to cut back grass on one side from top to bottom, then walked to the top and dis the same thing on the other side of the driveway. Then they took the same approach to using a wire broom to loosen caked-on debris. Those processes required four trips down the driveway before they made a fifth trip using a leaf blower to blow the cut grass and debris into a pile at the bottom of the driveway where they picked it up.
But this time, Johnson and his father worked in sections starting at the top, trimming grass, brushing loose debris and blowing the section clean onto the next section which had not yet been prepped.
They repeated this process all the way down the driveway until it was clean and ready for sealcoating – and they had made only one trip down the driveway.
A Cracksealing Challenge
Johnson says one of the biggest challenges on the hill was the 800 linear feet of cracksealing – “just enough to make it a challenge as you go down the hill,” he says.
They use an MA-10 crack sealing unit to apply hot pour material in the cracks, which on the flat surfaces ran horizontally across the pavement while on the hill the cracks ran down the hill toward the bottom of the driveway.
“But the problem on a hill with that kind of unit is you don’t handle the equipment, it handles you,” he says.
Johnson says that typically when cracksealing Warren fills the cracks with the MA-10 while Floyd follows behind with a squeegee as necessary. That worked fine on the flat surfaces at the top and very bottom of the driveway.
“But once you hit the break at the top of the hill the machine pushes you,” Johnson says. “You have zero control trying to handle it, and that’s while you’re trying to put the right amount of material in a crack and squeegee it.”
So to avoid wrestling with the unit they cracksealed the top flat area of the driveway first, working their way into the hill. “Once we had cracksealed to the hill, we couldn’t continue because we couldn’t pull the unit downhill. It would just take off on us,” he says.
So they pushed the applicator trailer to the bottom of the hill and then worked their way back up. Johnson says that while the toughest challenge with cracksealing was handling the equipment, putting the right amount of material in the crack without having it run down the hill was another issue.
“Because you’re on a hill the material wants to run downhill after it comes out the machine so you really have to control the amount of material you put in the crack,” Johnson says.
Reducing Trips: Sealcoating
Once the pavement was cleaned and cracksealed, Warren and Floyd started sealcoating at the top of the driveway on a flat surface in front of a four-car garage. Warren used a 9-in. brush to apply sealer on the driveway edges then sprayed sealer while Floyd drove the 300-gal., custom-built sealcoating truck and rode the brake.
As with surface prep and cracksealing, they worked in sections down the driveway until the got to the bottom of the hill, sealcoating it to the point where a 1,000-ft. gravel road picks up near the bottom off to the side.
They then returned to the road end of the driveway working their way back toward the base of the hill. Once they reached the gravel road they sealed the remainder of the driveway. Using this approach allowed them to stay clear of the busy highway and moving traffic for a safer approach to completing the job.