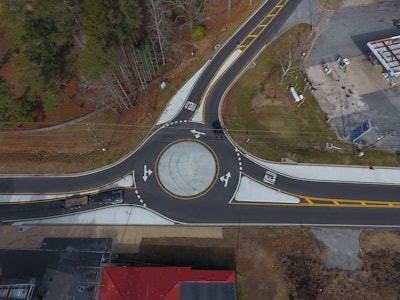
Constructing a roundabout amidst an operating roadway can be one of the more challenging efforts a paving contractor can face. Piedmont Paving, Newnan, GA, faced not only one but two roundabout challenges about 600 feet apart at two three-way T intersections.
Through extensive research prior to bidding and thorough planning and efficient execution once they had the job, Piedmont Paving’s crews were able to complete both miniature roundabouts quickly and with minimal disruption to traffic.
Started in 2006, Piedmont Paving has grown substantially in the last six years and now employs up to 90 people in peak season. The company is a full-site contractor offering paving, grading, storm drain installation, water and sewer installation, milling, and full-depth reclamation. Piedmont is primarily a commercial work contractor, but Andrew Trammell, estimator, says the last couple of years the company has pursued more small DOT jobs, especially those involving milling and resurfacing anywhere from $100,000-$3 million.
Roundabouts to Reduce Traffic Speed
Outside of Newnan, GA, State Route 29 runs north-south, intersecting with Green Top Road and Hall Jones Road roughly 600 feet apart. Traffic on Route 29 is known to travel at excessive speeds and the Georgia DOT (GDOT) determined the most cost-effective way to control traffic and improve driver safety at the intersections was by transforming both intersections into small roundabouts. Piedmont was awarded both jobs, and because the roundabouts were so close together Piedmont treated them as if they were one job, which essentially required only one staging.
“You need to think about how you build it when you price it and that was part of our planning when we bid them,” Trammell says. “Turning a normal intersection into a roundabout is kind of tricky, and it saved us money to go out and both roundabouts at the same time.”
Tim Cato, Piedmont project supervisor, says that while construction of the two roundabouts was not technically a design-build project, it was very similar to design-build. “We had the blueprints, but the blueprints basically just showed us the footprint of the road as it now stands and the footprint they wanted when everything was done. We had to figure out how to get there,” Cato says.
He says that even if the state or a general contractor or customer gives them detailed blueprints, they always go to the site and measure everything themselves.
“It is of utmost importance you double check the plans. You can’t rely on the information given in the plans – such as utility location, utility depth, road width, or lane width. Basically any information relevant to the work you need to double check on your own,” Cato says. “You don’t want to be told the utilities are 6 feet off the edge and then you get out there and find out there only 4 ½ feet off the edge and the utility company can‘t get out there to move them for two weeks. You need to have first-hand knowledge before you start planning.”
Planning and Traffic Control
In addition to taking their own measurements, Piedmont monitored the traffic at each site to determine what type of traffic control they needed. They then planned how best to introduce drivers to the new roundabout traffic pattern.
“State Route 29 is very busy, so you try to look at traffic and get a feel for what’s going on out there. That’s going to tell you how to plan for the work and how to handle the traffic,” Trammell says. “On Route 29 the traffic never stops, so we realized we always had to keep at least one lane open with flaggers and stop-and-go traffic control. We knew we would be putting two lanes worth of traffic into one lane.”
Piedmont Paving often handles its own traffic control but because of the complexity of this job they included enough cost in the bid so they could subcontract out traffic control.
Once they had a plan in place and a definite schedule, Piedmont notified the state’s traffic interruption services and sent them the traffic plan, letting the state know what lanes will be interrupted or closed when and what time of day so the state could notify school buses, police, ambulances, and the fire department. “If there’s any change in the schedule at any point during construction we revise the schedule and resubmit it,” Cato says.
Piedmont also hired police to be on site during the job, a standard Piedmont practice.
“Traffic never wants to conform to a new traffic pattern, it’s frustrating for them,” Cato says. “So we always hire local police or state police if we’re working on a state road. They are making a visual presence. That way we have an authority there who has the ability to slow traffic down, making it safer for us to work.”
Widening and Signage
Once they’d taken their own measurements, developed a traffic control plan and determined a schedule, Piedmont was ready to tackle the work. The first step was widening the pavement in several locations.
“One of the main hurdles to overcome is how to route the traffic between the initiation phase and completion,” Cato says. “Some intersections are not large enough to accept the roundabout traffic pattern without adding width so in those cases you need to widen the pavement before you can do anything else.”
That was the case on both these roundabouts, so Piedmont’s excavators dug down 10 inches in several locations, then poured concrete into the hole they’d dug. Normally they use aggregate to fill but because these widening efforts were small they decided concrete was easier. The concrete was placed 1 ½ inches below grade of the existing pavement so it would be level with that pavement after it was milled.
“It’s important to get all full width of the footprint of the new roadway in place before you do any milling,” he says. “Proper drainage and traffic flow are the two main things you have to get right at the start because if you don’t get them right at the start it can be very difficult and very costly to fix them later,” Cato says.
At the same time the roads were being widened, Piedmont posted construction-related signage as well as new signage in both roundabout locations.
“We wanted to make sure to let traffic know that a roundabout traffic pattern will be implemented in 14 days, so they have an expectation of what’s going to happen. The message signs were up and ready, letting drivers know 14 days in advance that the route is going to change,” Cato says. “All of the permanent signs go up at the start, too, and we cover them. Then on the last day we change it all over and uncover the signs. The drivers have been aware for 14 days that a new traffic pattern is coming and when we open it to the new pattern we uncover the signs and they’re all ready.”
Milling to Proper Drainage
Cato says Piedmont crews milled the original pavement to grade, removing the crown and profiling the road to reach its proper elevation minus the 1 ½ inches of hot mix asphalt that would be put in place. Milling depth ranged from more than 3 inches at the crown to just ¼ inch. “You’re profiling the road to get the proper elevation minus the topping elevation of 1 ½ inches,” he says.
“We always do an ‘as built’ of the road and I look over all the numbers and come up with what the drainage should be,” Cato says. “Generally 1.3 percent is a minimum of what we shoot for.”
Piedmont used a 3-point level to check the grade at the left edge of the pavement, the center of the lane and the right edge of the pavement. “You can’t have ponding water in a roadway,” Cato says. “That’s the time you have to make sure the pavement will properly drain because it’s easier to resolve it then than to try to fix it later.”
Milling took two days, and at the end of each day, before crews left the jobsite, they put down temporary striping and uncovered the signs.
“People on 29 are not used to slowing down so we had to train them to slow down and use the roundabout,” Trammell says. “So when we put down the temporary striping we striped it as a roundabout right from the start. We striped this job three times and each time we striped it as a roundabout so drivers would only have to adjust their driving patterns once.”
“The drivers only knew the original pattern and the roundabout pattern, there was no intermediate traffic pattern,” Cato says. “We try to eliminate any intermediate traffic patterns as much as possible.”
Straightforward Paving
The roundabouts required one lift of hot mix asphalt, 1-1/2 inches thick. Piedmont crews knocked out the mainline paving first. Cato says that the paver is responsive enough and the concrete islands are large enough (40 feet in diameter), that crews could pave around them. So most paving was done by machine, though he says that some tight areas required paving by hand with a skid steer dumping mix. “So you do have to get a little creative in how you do it.”
“When paving roundabouts you pave by priority of the lanes,” Cato says. “If 80 percent of the traffic comes south to north and exits north, then you pull that same lane from the south to the north, up and around the roundabout and you exit north in the same direction the traffic would travel. Then you look at the secondary route and you pave it the same way.”
Cato says compaction is the bigger challenge when paving roundabouts as rollers trying to make too tight a turn will end up tearing the new mat. So Piedmont’s roller operators were especially cautious and followed a planned rolling pattern that did not require tight turns.
Paving on both roundabouts was completed in three days. The entire project took less than eight working days. Piedmont hired Roberson Striping to install temporary striping after paving, then after a GDOT-required a 14-day waiting period installed thermoplastic markings.