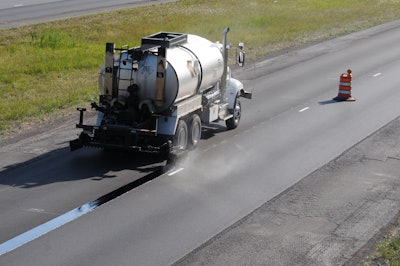
Longitudinal joints are recognized as one of the most difficult aspects of paving to construct. As a result, these joints often fail prematurely and rarely last the life of the asphalt mat itself. Not only that, but their failure triggers additional maintenance events and failure beyond the joint, pavement-wide.
The Asphalt Institute notes that the problem is that the joint edge is difficult to compact – partly because it’s a cold joint by the time the adjacent lane of mix is placed. The result is the joint area has a higher percentage of air voids than does the rest of the mat. In fact, Asphalt Institute research, which is supported by other studies, has found that 10% or higher air voids at the joint are not uncommon.
The higher the percentage of air voids, the greater the permeability of the asphalt mat and the greater the likelihood the asphalt – or longitudinal joint – will fail (see Figure 1).
Research and a variety of techniques and recommendations have been made to increase the life of the longitudinal joint, and one of the most-recent efforts that is generating increased interest is a Longitudinal Joint Sealant (LJS), also termed a Void-Reducing Asphalt Membrane (VRAM). VRAMs are a highly polymer modified asphalt cement that go down hot, in the area of 300°F. Unlike a typical crack sealant or crack filler that is applied after the asphalt mat is placed and compacted, the VRAM is a liquid that is sprayed onto a milled surface or onto old asphalt accepting an overlay – directly beneath where the longitudinal joint will be – prior to paving as a part of the paving process.
“The reality is, if you have 10% voids, the odds are that the joint is likely to only last 10 years instead of 15,” says Dave Henderson, vice president of specialty products at Asphalt Materials Inc. (A Heritage Group Company), which produces a VRAM called J-Band. “Our goal was to find a way, using traditional construction methods, where the joint would last as long as the rest of the roadway.”
He says VRAMs are being tested or used in 13 states and three states – Illinois, Ohio and Indiana – are specifying a VRAM on select state paving jobs. The research lab at Heritage began working alongside IDOT towards a solution in early 2000s. Henderson says the hypothesis was that if you could eliminate premature failure at the longitudinal joint, you could significantly extend the life of pavement, eliminate the need for additional maintenance triggers, create significant savings for agencies, and decrease downtime to the traveling public.
He says that because of the heat of the hot mix asphalt overlay and the compactive effort of the roller, the VRAM sealer wicks up into the asphalt mat, filling air voids. “The hot asphalt mix liquefies the sealant material and the roller forces the mat and rock down into the sealant, and the sealant wicks up into the mix filling the air voids.”
Because the material is hot, a specialized piece of equipment that can handle hot material must be used (though some trucks can be retrofitted). A spray bar extends perpendicular to the spray tank and puts down a fan of material 12-18 in. wide, with equal material on both sides of where the joint will be. Henderson says that J-Band, for example, is applied at an average application rate of 1.5 lb. per foot. “But the rate depends on a variety of factors such as the mix design volumetrics, and mat thickness,” he says.
Henderson says that when combined with proper paving techniques, a VRAM can help extend the life of a longitudinal pavement joint to 15 years or more. He says studies comparing VRAM with traditional joint repair practices over past years have found that for every $1 invested in a VRAM, $2 are saved on pavement maintenance costs.
He says VRAM holds up well under traffic, adding that the sealant can stay on the pavement as long as the public agency is comfortable allowing it to be open to traffic. “We’ve had the material down as long as a week on roads with low traffic volume and it’s performed well,” he says. “But most use is on high-volume roads and most agencies don’t want to leave it on the road in those circumstances. It’s ready in under 30 minutes to accept the HMA, so in most cases the paver follows soon after the J-Band is sprayed.”
He says VRAMs are being tested or used in 13 states and three states – Illinois, Ohio and Indiana – are specifying a VRAM on select state paving jobs. The research lab at Heritage began working alongside IDOT towards a solution in early 2000s, with a single goal: to solve a pavement owner’s largest problem: the longitudinal joint. Henderson says the hypothesis was that if you could eliminate premature failure at the longitudinal joint, you could significantly extend the life of pavement, eliminate the need for additional maintenance triggers, create significant savings for agencies, and decrease downtime to the traveling public.
“In 2016 Illinois implemented it on two projects in each DOT district,” Henderson says. “It was included on 50% of state projects in 2017, and in 2018 it was required on all state paving jobs, though I don’t know if the state actually reached that 100% level.”
In Ohio, the recently passed House Bill 51 requires ODOT to install centerline rumble strips for all two-lane state highways with a speed limit of more than 45 mph. He says many believe this preventative approach to safety is likely to gain ground nationwide. However, it’s important for pavement managers to recognize that rumble strips further compromise the already-vulnerable longitudinal joint, and take proactive measures to protect the joint. “VRAM is one of the options the state is requiring contractors to use in order to protect the joint after the installation of centerline rumble strips,” he says.
Henderson says that tests have shown VRAM’s effectiveness when used alone, but some agencies spec it beneath that overlay and also spec using a joint sealant from the top. “I’ve seen it done with and without joint sealant,” Henderson says. “I’d never discourage anyone putting sealant on top. It probably depends on the agency’s preference.”
While Henderson says the company recently used its product on its own newly constructed parking lot, it is usually used on roads. “You may sometimes come across a highly engineered parking lot and it certainly could be used on that,” he says. “Over time we’ll probably see more and more low-volume roads and parking lots specifying the material, but today it’s mainly used on high-volume roads or expensive-to-maintain roadways like runways, racetracks, and interstates.”
While Henderson says the company recently used its product on its own newly constructed parking lot, it is usually used on roads. “You may sometimes come across a highly engineered parking lot and it certainly could be used on that,” he says. “Over time we’ll probably see more and more low-volume roads and parking lots specifying the material, but today it’s mainly used on high-volume roads or expensive to maintain roadways like runways, racetracks, and interstates.”