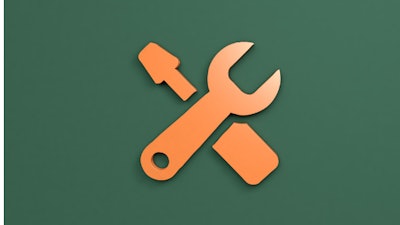
I think it’s safe to say that all pavement contractors own equipment of some kind. Equipment enables us to be more productive, it does a better job than doing work by hand and it saves on labor costs. Yet too often the equipment that enables us to be profitable companies gets taken for granted, overlooked or ignored.
That is until there’s a field breakdown in the middle of an important job or that causes a disruption in our schedule and calls to clients to delay work. For many contractors it’s only then that they think about equipment maintenance.
The Cost of Maintenance
Some of the lack of maintenance I have seen over the years would make most contractors sick. There are obvious consequences: It will cost you money and it will cost you money.
Equipment maintenance costs money when handled properly, but avoiding maintenance is even more costly. I would encourage every owner to make a simple maintenance plan. Not only will it keep the iron that’s making you money producing for you, but it will ensure you don’t have a breakdown when you might be in a time-critical situation.
Maintain Like the Airlines
Equipment maintenance can encompass a huge swath from minimal oil changes all the way to major parts replacements and paint jobs.To each his own, but I will say that going the extra mile on equipment maintenance never hurts in the long run.
We have a program that I like to call Aircraft Maintenance. Anyone that knows me knows of my passion for airliners, so naturally I have adopted a maintenance approach similar to that of airlines. We not only have regularly scheduled basic maintenance—think oil and filter changes, greasing etc.—but we also conduct the “aircraft” portion where we monitor and preventively replace hoses and other wear parts before they fail. We proactively replace them on cycles.
Our crack seal machines are a good example. They have heated hoses, and we know they can fail from time to time. So, on a regular schedule based on hours of use we send them to be rebuilt in the offseason.
Yes, preventive maintenance costs up front, but we haven't had a wand or hose fail in service or any other time-consuming breakdown in quite a while. We haven’t had to stop in the middle of a job, pull a piece of equipment out of service, or disappoint clients by rescheduling their work.
Managing employees can be difficult enough; You can’t let equipment be another cause of those problems.
Maintaining Your Image
Another aspect of equipment maintenance is the image part. We are a highly respected, professional contractor selling our services to other professionals—and we want to be seen that way.
At the end of each season, we will thoroughly clean everything, and we take it a bit further and will paint one or two pieces a year. This simple program has created such a nice image for our company, as it can yours. I personally believe that we are able to get higher margins and more work by having more of a professional image.
I would encourage every contractor who operates equipment to develop a preventative maintenance plan, no matter the size of your fleet. Break it down into regularly scheduled must-have maintenance such as lube, oil, and filter changes, then add in preventative items to include hoses, belts, cords, and other wear parts. Finish it off by image maintenance. Don’t just clean your equipment, but paint it every few years.
The old saying that we tell our pavement maintenance customers holds true for all of us: An ounce of prevention is worth a pound of cure.