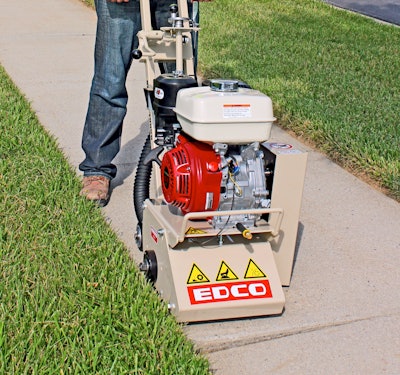
Contractors in the pavement maintenance space wear many hats. They can diagnose pavement defects, address curb and gutter issues, sweep parking lots and even let their customers know if their lot needs new striping work done. For this reason, many contractors are considered a one-stop-shop for their customers, completing many different types of work so their client doesn’t have to call different service providers to take care of their property.
This service range also includes diagnosing potentially dangerous areas in need of repair around a parking lot or property - from potholes to trip hazards.
According to the Americans with Disabilities Act (ADA) a trip hazard is any vertical change on a surface over ¼-inch. We see this all the time on uneven concrete surfaces due to freeze-thaw cycles or surfaces that have been disrupted from tree roots. These large cracks, breaks, or buckled areas of pavement can lead to serious injury and possibly make property owners liable in a personal injury or premises liability lawsuit.
Knowing how to talk to your customers about these repairs can not only help you gain their trust, but also lead to another stream of business.
How to Remove Trip Hazards
Fortunately for contractors, repairing and smoothing these hazards is less time-consuming and difficult than you may think.
A concrete scarifier (a.k.a. planer) is used to grind down the high side of a trip hazard until it is level with the opposing sidewalk or surface area again. The machine has a depth crank that can be adjusted up and down. The operator will continue to make multiple passes until the desired levelness is achieved. The resulting surface from the scarifier is also textured and slip-resistant.
For most pavement maintenance contractors starting with this service, you may consider renting a concrete scarifier trip hazard repair package. This includes a scarifier, vacuum and generator for around $400 for one day. You will want to ensure your grinding application includes a vacuum to keep your workers and the public from exposure to harmful airborne concrete dust.
Each 4-ft. sidewalk repair section only takes about fifteen to twenty minutes to complete and depending on the area you live in, you could complete between 15 - 20 trip hazard repairs in a day to make renting this package very-cost effective and profitable for your business.
Adding this piece of equipment to your fleet can also be a great way to ensure you’re able to service your customers as there will inevitably always be trip hazards to address. Grinding them to ensure ADA compliance is a much more economical way to repair the concrete than a complete removal of the hazard which can cost upwards of $10,000. Save your customers time and money while also adding value to your business.
If you need help getting started, the experts at EDCO have over 60 years of experience in adding value to their customers’ businesses. Contact them today at [email protected]