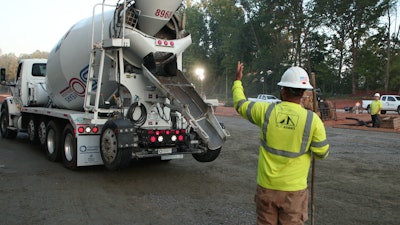
Even though I'm the editor for Asphalt Contractor and Pavement Maintenance & Reconstruction, which largely focuses on the blacktop side of the industry, concrete obviously plays a big role. I know many asphalt companies that also offer curb or sidewalk services along with their milling, paving, sealcoat, and various other products.
Recently, I spent a few days on a jobsite with Ace Avant in High Point, NC, getting some hands on training and experience with some of the large scale concrete work they do. There was way more than I could learn in just two days, but it was still a good overview into the business. Comparing it to the asphalt and blacktop work I've seen, it made me consider some thing that you might want to stop and think about before adding a concrete division to your company's offerings.
1.) It's Your Own Asphalt [What To Check At The Door]
One thing that surprised me the most when I literally, and figuratively, dipped my toe into the world of concrete, was how all my expectations about it were mostly wrong. For the past two years I've been jumping feet first into the world of asphalt and pavement maintenance, and somewhere along the line I got some notions about what working with concrete would be like. So, you've got to get your expectations under control first and foremost.
The material was heavier than I expected it to be, it dried faster, the work from top to bottom is much quicker paced, and about a dozen other things jumped out to me. For one, just comparing the bottom of the ladder job is much, much more physically demanding than it is on asphalt. Don't get me wrong, both are very hard, but I would rather shovel hot asphalt over shoveling cement any day of the week.
Pat Brown
2.) What Kind of Concrete Work?
This was another expectation thing that far exceeded what I imagined concrete work to be, and just how far reaching it is. For you, potentially adding some services to your offerings, it's crucial to specifically figure out what areas of work you want to work in, how they compliment the other services you're already doing, and then create your implementation plan from there.
For instance, there's a world of difference between outdoor pours versus indoor. What type of finishing work are you going to offer? Curbs? Sidewalks? Stamped or decorative? Floors, Parking and truck loading zones? Ace Avant, the company I was shadowing even offers building construction with their tilt-pour walls. They are able to pour you a new building. Each one of these different services requires its own expertise and proper machinery. It's also important for your customers to know exactly what you're offering. There's a lot of difference between tilt-pouring a three story factory wall and fixing a catch-basin in a parking lot.
Pat Brown
3.) What Crosses Over (and What Doesn't)
The good news is that there are some basic skill crossovers between the two types of work. Perhaps, the most important being the understanding of earth work, grading, and drainage. Concrete and asphalt customers both want nice flat, smooth surfaces to drive, walk, or park on. The engineering that goes into water runoff and proper drainage is pretty much the same in a lot of ways. Getting the base-grade done correctly make everyone's jobs easier. So, if you already employ that type of work in your current jobs, this is something that can readily cross over.
What doesn't crossover is the material science. Asphalt people talk about density, compaction, aggregate size, multiple layers, binder, and AC. Concrete people talk about slump, water content, finish texture, fly-ash, and Portland cement. Again, there's some crossover here, but in most cases my asphalt knowledge wasn't that helpful to me in understanding what all these things meant. Knowing how the material moves, reacts to the environment, and how to control it is going to take the same amount of time as when you starting learning asphalt. Just be prepared for the investment.
Pat Brown
4.) New Equipment
Put this under the category "doesn't cross over" because there aren't a lot of specialized tools that you'll already have as a blacktop company, which are crucially needed for concrete work. For one, did you know you'll need a decent carpenter? That's right! The quality of your pours are at least somewhat of a function of the person who builds your framework. Pavers, asphalt rollers, lutes and tampers wont be seen on a concrete job, but they have counterparts.
However, the list of what tools and machinery you'll need to invest in comes down to the type of work you want to get into. Some of the best basic work can be done feasibly well with a good two-by-four, a trowel and a brush. On the large pour I visited, they used a large 3D laser screed with built in Trimble controls. While we hand shoveled for the first few feet, the speed and accuracy at which the laser screed operates was incredible. There are ride-on and push-behind finishing tools with giant spinning fan blades, "bull-floats" that have forty-foot pole arms, concrete saws, telehandlers, and all manner of excavators.
Pat Brown
5.) Jobsite Hours and Pace
Another thing that I had no earthly clue about before working on a concrete jobsite, was this quote from the project manager, "You don't do the concrete, the concrete does you." This was in regards to the time from the second the first truck starts pouring mix down. If it's cold and raining, you have to stay with your product until it's set up. Sometimes that can mean an early morning pour, and then sitting around watching the job for hours late into the evening. If you or your crews are used to the predictable hours that come from asphalt work, this could be a problem.
The jobsite pace also works very differently. Once the first cement truck came and stared pouring, everyone kicked into high gear. Everyone had a concrete rake, shovel, or hand-float, and was quickly pushing the material where it was needed. Immediately the crew was leveling and smoothing the mix around the frame's edge, and patting the surface in order to sink larger aggregates and bring the "cream" to the top. Then, as the crew moves further down the pour, things space out, and, depending on the how quickly it's drying, the finishers come in behind everyone.
That process felt very similar to how asphalt crews start all together, staying with the paver, and then as the runs fill in a given area, the finish rollers are behind the paving team getting final compaction and getting out any errant roller marks.
Pat Brown
6.) Training
This might seem obvious, but it would be a smart move to find a way for either yourself or your chosen manager to spend some time with another cement crew. Go out and ask questions, get your hands dirty, and then, allow for your workers to do the same. With the job market for experienced concrete crew members already being pretty challenging, it will be much more likely that you'll be building the crew from the ground up. Any training seminars or trade show educational events would be helpful too.
Whatever you do for yourself and/or your management, try your best to extend that to your new concrete crew. Especially, if they're coming from an asphalt team, this is going to be a new adjustment. The amount of training you put into it, the quality of training you give to your employees, will go a long way in determining how successful your new concrete division will be for your business.
Pat Brown