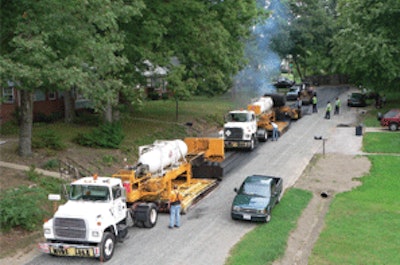
While the heat scarification process of preserving asphalt pavements has been part of Henrico County’s (located east and northeast of Richmond) road maintenance approach for over 20 years, it’s only been the past three to four years that the preservation approach has been used on urban and rural roads covered with multiple layers of chip seal.
Tom Cocker, road construction and maintenance superintendent for Henrico County’s Department of Public Works, is in charge of maintaining approximately 1,100 road miles and he’s finding the heat scarification process a cost-effective way to preserve structurally sound paved roads.
“We’re one of two counties in Virginia that maintains its own road system, and in our case those roads can be 16-foot-wide rural roads, (residential) subdivision roads, or (24-foot-wide) secondary state highways in urban areas,” Cocker says. “This year we completed 800,000 square yards of heat scarified chip-sealed road surface, which was then slurry sealed.”
Henrico County started using heat scarification (also referred to as hot-in-place) back in the early 1980s on asphalt paved roads. The scarification process addresses surface deformations, like oxidation and alligator cracking, as well as leveling and reshaping the road profile for proper drainage prior to application of either a hot mix asphalt (HMA) overlay or a surface treatment, like chip seal or slurry seal. Many of the roads in Cocker’s jurisdiction were treated with multiple chip seal applications over the years and the county’s governing body decided to discontinue using the chip seal process several years ago.
The heat scarification process proved a viable alternative for maintaining chip sealed roads by heating an inch to an inch and half deep to soften the asphalt binder used to hold the aggregate chips in place, re-blending and screeding the existing material (correcting the crown and surface imperfections in the process) and then compacting the new mat in preparation for a slurry seal surface coat.
One of the advantages of scarifying chip sealed roads is that you don’t have to use a rejuvenating agent, like an emulsion additive that’s typically used in a hot-in-place asphalt process.
“There’s plenty of asphalt (binder) in place from the previous chip seal applications and the heat scarification process warms up the asphalt, enabling us to rework the surface material,” Cocker says. “Sometimes we’ll add a #8 chip seal stone in front of the scarification equipment to provide a little more structure to the surface when it’s blended and screeded, but we never have to worry about adding a rejuvenator.”
Following the scarification process, the new surface is generally covered with a slurry seal coat within a week or two, but some roads have gone without surface treatment for up to six months.
“We like to get the roads sealed and protected from the elements as soon as possible, but there have been situations that have prevented us from completing the project in a timely manner,” Cocker says. “It’s not ideal, but it hasn’t been a problem because the roads have been reshaped for correct drainage and then compacted by a four- to six-ton roller.”
Preservation partnership
Henrico County has developed a strong preservation partnership with American Asphalt Surface Recycling to maintain the county’s road system with the heat scarification maintenance approach. Cocker, who’s been a county employee since 1964 and division head of the road maintenance department since 1978, has used the Chicago-based road recycling contractor for over 20 years..
“When I took over the department, the county had approximately 700 road miles to maintain and now we have over 1,100 miles to maintain,” Cocker says. “We initially began using American to scarify roads we wanted to apply an HMA overlay to or roads that were good chip seal candidates. They (American) would spend several weeks each summer here working on those types of projects, but as our road system grew and preservation became a more important solution to how we would maintain the road system, their time here grew as well.”
American’s role in Henrico County’s preservation approach grew even further when county officials decided to discontinue its chip seal maintenance process in 2000 and looked for another viable alternative to preserving roads which had been maintained with layers of chip seal.
“We’ve done a lot of work on chip-sealed roads, and the heat scarification equipment we use allows us to warm up the surface without burning the heavy asphalt liquid used in a chip seal application,” notes Joe White, vice president of American. “We use a propane-fired refractory system (flames heat a brick bed that then radiates heat down to the road surface), which allows for slow, deep heating of the material we want to rework without burning the material.”
American has modified and improved the original AEI Asphalt Recyclers that it uses in its heat scarification process to adapt to the type of preservation work Henrico County and other road agencies are requesting. In the case of Henrico County, American’s heat scarification system provides an economical approach in correcting minor surface deformations and profile issues of roads that are structurally sound.
“We’re averaging approximately 50 lane miles a year with our current scarification and slurry seal approach to preserving and maintaining chip sealed roads,” Cocker says. “In 2003 we processed between 500,000 and 600,000 square yards of chip sealed road material. In 2004 we processed 700,000 square yards. This year (2005) we’ll process 800,000 square yards.”
In addition to the chip seal road preservation work, Cocker says his department slurry seals 50 road miles of asphalt paved roads each year as part of its preservation initiative.
“We have our own (HMA) plant and our own paving crews to handle the paving required on our road system and each year we do some type of maintenance and/or preservation work on approximately 10 percent of the roads that make up the county’s system,” he says.
The county is divided into five political districts and part of Cocker’s responsibility is to make sure each district is maintained fairly as he slots annual maintenance/preservation projects. Generally, one of his scarification/slurry projects will include an entire residential subdivision or the entire length of a rural road.
With a total annual road construction/maintenance budget of $16 to $17 million to cover everything from new bridge construction to drainage work to pothole repair, Cocker has only $3 to $4 million to maintain existing paved roads.
“We have roads that have to handle 5,000 to 10,000 cars per day and we have roads that have to handle 30,000 cars per day. So it’s important for us to utilize the most cost-effective solution in preserving the quality of our road system in order to have the funding required for major new construction,” he says. “The heat scarification process followed by a slurry seal application has been the answer for us. It’s a very economical investment in preserving the system we have in place. It allows us to extend the dollars we’re budgeted for road maintenance.”