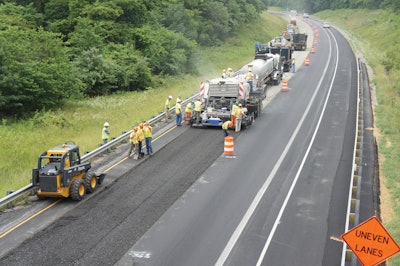
Virginia's Interstate 81 runs for 325 miles along the state's northwest spine from West Virginia to Tennessee. The Virginia Department of Transportation (VDOT) is rehabilitating a 3.7-mile, two-lane section of southbound Interstate 81 in Augusta County between exits 217 and 213. It's using a specific combination of three reconstruction processes to recycle and reuse existing pavement material for the first time on this type of a project in the United States.
The processes are cold in-place recycling, cold central-plant recycling and full-depth reclamation. "This project will save VDOT millions of dollars by reusing the resources at hand, rather than buying and transporting tons of new material to the site and disposing of the old," says Dr. Brian Diefenderfer, a Virginia Center for Transportation Innovation and Research (VCTIR) pavement researcher.
The contract for the in-place pavement recycling project was $7.64 million and was awarded to Lanford Brothers Co., a specialty contractor located in Roanoke, VA.
The project was awarded in December 2010 and is expected to be finished by November 2011. The in-place pavement recycling portion of the project took two months to complete.
The problem
This part of I-81 was built in the late 1960s. VDOT has routinely maintained the surface asphalt by periodically patching and replacing it. The original foundation of compacted stone aggregate and soil had weakened to the point it no longer provided a stable base for the overlying asphalt layers.
Fatigue cracking, caused by years of heavy traffic loads, had deteriorated the pavement structure from bottom to top. Symptoms of this deterioration could be addressed by milling the existing surface and repaving it, but the underlying condition would remain. The cause of this extensive wear could only be remedied by reworking all the material down to the subgrade.
Unless the foundation was repaired, simply repaving the road surface was only going to be a temporary improvement. If VDOT were to do nothing to this section of road, the pavement would crack more. Pieces up to the size of a golf ball could come out of the road.
The fatigue cracks were also allowing a direct path for water to seep down to the pavement foundation. The water saturated the subgrade, further reducing its load-carrying capacity. This condition could lead to deep rutting (surface depressions) within the wheel paths that can affect skid resistance and even steering ability.
The fix
The repairs were slightly different for the right and left lanes. Since most heavy traffic loads use the right (travel) lane, it has more underlying damage than the left (passing) lane.
Right lane: The asphalt layers were milled down to the top of aggregate layer (about 10 inches from the surface) by Lanford Brothers. This material was stockpiled on-site for reuse in the new pavement structure. The next 12 inches of material (aggregate and soil) were strengthened with a stabilizing agent (cement and lime) by subcontractor Slurry Pavers Inc. This material was recompacted to form a platform for the next step.
The stockpiled milled material from the asphalt layers was processed in an on-site mobile plant where a foamed asphalt binding agent was added. The resulting material was repaved at ambient temperatures to a depth of 6 inches and compacted. Four inches of traditional hot mix asphalt material was placed, followed by an additional 2-inch stone matrix asphalt (SMA) overlay used as the riding surface.
The challenge with the right lane was following the sequence exactly, says Landford Brothers Co. President Ken Lanford. "We were constantly adjusting so we could control the schedule and sequence," he explains. "This project was definitely a partnering project. We had a great, dependable team of subcontractors. We were also equal partners with the highway department - we recognized each other's goals and worked with each other to achieve them."
Left lane: The top 2 inches of the asphalt layers were milled. The next 5 inches of asphalt were recycled in-place using a machine to pulverize the material in-place and add an asphalt binding agent. This material was recompacted. Two inches of traditional hot mix asphalt material was placed, followed by an additional 2-inch SMA overlay as the rising surface.
Cold in-place recycling and cold central-plant recycling was used to repair the asphalt layers of the left and right lanes respectively. Both are performed at ambient, rather than hot, temperatures. In the right lane, the stone aggregate base and subgrade were mixed in place with a stabilizing agent to reconstruct the road’s foundation as a full-depth reclamation.
The challenges
Diefenderfer said the project had several challenges, the first of which was familiarity with the in-place recycling techniques. VDOT’s research facility, the Virginia Center for Transportation Innovation and Research (VCTIR) in Charlottesville, had studied a number of pavement rehabilitation techniques and recommended these innovative recycling processes on the I-81 project. Additional efforts are on-going within VDOT to develop guidelines to use these processes throughout the commonwealth.
Other states are separately using cold in-place recycling, cold central-plant recycling and full-depth reclamation, which are gaining acceptance nationwide, says Diefenderfer. VDOT recently conducted three two-year demonstration projects in Goochland, Powhatan and Franklin counties to study and develop recommendations for full-depth reclamation.
The equipment - all manufactured by Wirtgen - used on the job included:
- A reclaimer which stabilized the 12-inch sub-base underneath the 10 inches of asphalt which was milled off the right lane and trucked to the mobile cold-recycling plant located nearby for reprocessing.
- A mobile cold-recycling plant reprocessed the milled material at a site away from the road. A stabilizing agent was added, then the asphalt was reapplied to the roadway.
- A cold recycler milled the top 5 inches of the left lane, reprocessed the material, added a stabilizing agent and reapplied the newly recycled material to the roadway.
Diefenderfer says VDOT relied heavily on the expertise of the local contracting community as well members of the Asphalt Recycling & Reclaiming Association (ARRA), other DOTs and equipment manufacturers to help understand the best practices for the in-place recycling techniques and equipment before the project even began.
Another challenge was traffic control. According to Lanford, the reconstruction portion of the project was completed during four separate, 5-1/2-day-long single-lane closures over a two-month period. The lanes had to be open Friday night and were closed through Thursday morning. "The penalties were really high if we weren't ready to bring that traffic back at 7 a.m. on Thursday," says Lanford. "We had to plan our work accordingly and keep one eye on the sky and the other on our laptops for weather updates."
VDOT tried to help with traffic congestion on its end. "We had a media campaign – both radio and Internet – from Roanoke, VA to Harrisburg, PA to warn the public about traffic issues," says Diefenderfer. The web page included a downloadable two-page map showing the lane closure dates, detour routes, peak travel times and estimated travel times through the work zone. "We just wanted to let people know what was going on," he says. "Traffic backups weren't as bad as they could have been."
The benefits
"This unique project has the potential to revolutionize the way we rehabilitate our aging road system," says Diefenderfer.
Lanford agrees."This project will save VDOT and taxpayers millions of dollars by reusing existing resources rather than buying and transporting tons of new raw material to the site and having to dispose of old materials offsite,” says Lanford. "To our knowledge, this is the first time these processes have been utilized together on the same project and in the same location, and we’re proud to have VDOT as our partner as we develop new, environmentally friendly, cost-effective construction trends for asphalt repair."
Recycling the existing road material not only eliminates the need for numerous truck trips to haul stone and paving materials to and from the site, but also allows the causes of the deterioration to be addressed rather than just the symptoms.
"We wanted to address the cause of the problem, not just the symptoms," says Diefenderfer.
In-place pavement recycling is much more cost effective and should greatly increase the pavement service-life. "The process is more environmentally friendly in that fewer loads of material will be trucked to the site. less new material will be required, and the operation is conducted a ambient temperatures - thereby reducing greenhouse gas emissions," he says. "The process has quicker completion times, which reduces the traveling public disruptions."
VDOT estimated that conventional pavement construction and traffic-management concerns would have required building another lane throughout this section of interstate – estimated at approximately $40 million – as well as widening bridges, lengthening overpasses and excavating and replacing fill material.
The traditional method also would have required extensive natural resources to build the additional lane and reconstruct the failing pavement. In addition to the financial costs, the project would have taken years to complete and would have limited VDOT’s ability to maintain other pavements and drained maintenance resources. The I-81 In-Place Pavement Recycling Project will accomplish this work in eight months for around $7.6 million.
"Conventional pavement construction on this project would have required building another travel lane, extensive natural resources, and one to two years to complete," Lanford estimates. "But by using in-place recycling, the project time is cut to three to four months, resulting in significant cost savings to Virginia taxpayers."
Less time and less money to complete a quality project – something all of us can agree on.