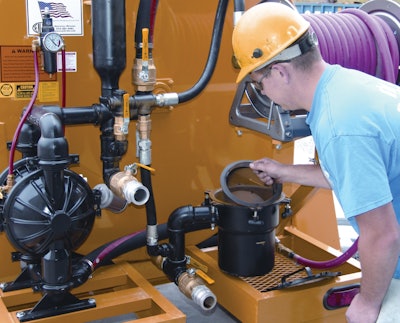
As the weather gets colder and the days get shorter, sealcoating season is quickly approaching its end. While contractors are finishing up their last jobs, the time to winterize their sealcoating equipment is near.
To avoid stress and costly repairs at the beginning of next season it is vital contractors properly clean their equipment before storing it for the winter.
Ending the season
When contractors purchase new equipment the manufacturer will often give them paperwork detailing how to clean and maintain equipment. Brent Loutzenhiser, owner and president of Seal-Rite, encourages contractors to follow those steps in order to ensure proper maintenance is completed.
With 12 years experience in the pavement maintenance industry Sal Scacciaferro, owner of Pre Mix Seal Coatings in Toms River, NJ, offers services such as crack filling, pavement repair, and sealcoating. Operating with three Seal-Rite tanks and one 6,000-gal. storage tank, Scacciaferro, who typically ends his sealcoating season in November, has several tips contractors can use when winterizing their sealcoating equipment.
Jordan Ford, owner of Applied Asphalt Coatings, Salt Lake City, Utah, has been in the industry for 10 years offering services including sealcoating, cracksealing, patching and striping. When it hits mid-October or the temperature no longer reaches 60 F Ford calls it a season and prepares his equipment for the winter.
A few hours and a little bit of water
First, Scacciaferro suggests contractors make sure all of the sealer is gone before the season ends. "We try to keep everything just about where we have to be, and if necessary we will take left over sealer and transfer it to another tank," he says. "Anything left over we will put in a 55 gallon drum and store it in the garage."
After the excess sealer is stored, Loutzenhiser suggests contractors power wash the inside and outside of the equipment. Pressure washing the paddles and agitator shaft through the manway will loosen any buildup on the surfaces that are not reached by the rubber wipers inside a tank.
Next, Ford fills the tank up half way with water, lets it agitate, and flushes out the residual sealer.
Letting the machine circulate water throughout both the tank and the plumbing will clean most the buildup that would be present from a typical season’s work. "Keep in mind that there are a few spots in the plumbing where abrasives can settle and really restrict your flow," Loutzenhiser says. "A lot of times when you circulate the water, it will flush out any those abrasives that have settled."
Once Scacciaferro runs water through the equipment, he opens up all of the valves to make sure water is drained from the tank and nothing is left in the piping. Next, he removes the hose and rather than rolling it up he stretches it out so that water will not gather and freeze.
Once completing these steps, Scacciaferro lets his equipment sit until January or February. "Any cleaning after that is easier to complete when this stuff freezes up," Scacciaferro says. "It's just a matter of vibrating it off with an air gun and sweeping it up. If you try to clean it when the temperatures are around 40 or 50 F the heat from the air gun and the sun will make the sealer mush. It smears, so we wait until the dead of winter to clean the tanks."
Once the equipment has been thoroughly cleaned, contractors should also pay special attention to the pump. Loutzenhiser suggests contractors first use an 80/50 tip and expel water through the spray tip while maintaining pressure of 100 psi. Then, apply a solution of soap and water on the outside of the material pump. This solution will allow contractors to visibly inspect their pump for any air leaks because there will be bubbles created anywhere that air might be leaking. He suggests that contractors check for air leaks at both the end and beginning of the season, before sealer is put in the machine.
During the winterization process some contractors will fill the plumbing with antifreeze; however, after cleaning the machine thoroughly, Loutzenhiser suggests contractors run windshield wiper fluid through the plumbing instead of antifreeze. He says washer fluid serves the same purpose (prevents freezing inside the pump), it’s less harsh and more cost effective than antifreeze. Once the windshield wiper fluid has been run through the plumbing, dry fire the pump to remove the excess and leave ball valves ¾ open.
Ford's unit has a water tank, so he flushes the water out filling it with a mix of windshield wiper fluid and water. "We run the mix through the pump system, and it acts as antifreeze," Ford says.
Completing standard maintenance
Along with properly cleaning the tank of the sealcoating equipment, it is also essential to complete standard maintenance on other parts of the unit. "You have to check your tires, grease the bearings on your axles, check your brakes for wear, and check the spray wand hose," Loutzenhiser says.
Ford completes maintenance on the engine and carburetor. "It is important to drain the fuel from the unit," he says. "You also need to change the oil so that the engine won't spend the winter sitting in dirty oil. When the engine is running, we spray Fogging Oil into the carburetor intake where the air filter is. The spray provides a film that coats the inside of the engine to protect it from moisture that can create rust."
Another part of the unit contractors must check is the filter pot. "If the filter pot is neglected, on the first job of the season you will have a bunch of sand that has collected inside the strainer or filter and it won't pump," Ford says. To prevent this, Ford suggests contractors drain out the filter, clean it, and store the filter pot dry.
Contractors must also remember to drain the water from the air tanks. "If there is any water left in the air tanks it will create condensation, and it will damage the air tanks," Scacciaferro says.
Why winterize?
It is important for contractors to follow the steps to properly winterize their equipment because if they don't follow all the steps many problems will occur. "A lot of times they let their material freeze inside the tank and inside the plumbing," Loutzenhiser says. "When sealer freezes it crystallizes and contractors have a substance in their tanks that is now a solid – they will have to chisel and shovel it out." These issues can lead to costly repairs.
Seal-Rite has about four cases a year of contractors who don't properly clean their equipment at the end of the season. "You'll only make the mistake of letting sealer freeze inside your system one time," Loutzenhiser says. "You're talking about thousands of dollars of damage. You could have to buy everything on the rear of the system — a new pump, all new plumbing, and a new filter pot."
Another benefit to checking the equipment thoroughly is finding what repairs need to be made before the spring rush. "A lot of times we see contractors who want their parts shipped over night in the spring," Loutzenhiser says. "At the end of the season you can put your machine through its paces and find any issues that need maintenance."
It can also be beneficial to contractors to complete these repairs before the start of the season due to more cash flow in the fall.
By completing proper maintenance, contractors can preserve their equipment and save money. "In the industry we are always telling our potential customers that maintenance will save money in the long run," Ford says. "If a little bit of time is spent in the fall winterizing a good amount of money can be saved in the spring."
How to Clean Bulk Storage Tanks
Along with winterizing sealcoating equipment, it is also essential for contractors to winterize their storage tanks. Brent Loutzenhiser, owner and president of Seal-Rite, recommends that contractors use similar strategies for cleaning out bulk storage tanks that they would use for cleaning and winterization of their smaller sealcoating equipment. These simple steps are a slight variation due to the stationary nature of bulk storage tanks:
- Cleaning. First, power wash both the inside and outside of the bulk tank. Using the manway and/or manhole on a bulk storage tank, contractors can remove the majority of the sealer from the agitator shaft and paddles.
- Agitate. Secondly, to remove any buildup on the tank walls, let the bulk tank agitate with water. Move the paddles in both directions to eliminate the maximum amount of product from the walls of the tank.
- Let the material drain. Next, let whatever water and sealcoating materials remain drain to toward the ball valve for removal by tipping the bulk tank slightly.
- Clean the inside. Moving forward, once the majority of product has been removed through power washing and agitating, contractors should go inside their bulk tank to inspect and clean any remaining product or debris from the cleaning process.
- Winterize. Finally, use the same process of winterizing with windshield washer fluid that Loutzenhiser recommended for a smaller sealcoating rigs. This will protect your pump and plumbing components from freezing during the winter months.