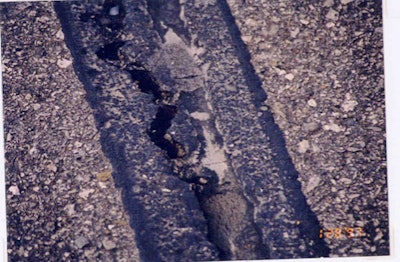
Preparation of pavement cracks is important in successful sealant application. Routing cracks prior to installation provides clean surfaces for sealant application and a 40% greater chance of sealant success.
Cutting the pavement along the crack path provides a reservoir for sealant in smaller cracks and an intact sidewall for adhesion. Some industry professionals skip this step and move on to the cleaning process, a method known as "blow and go." However, routing cracks before sealant installation is recommended and may be a job specification requirement so contractors should know these best practices for crack routing.
Determining When to Rout
Crack density is a factor to help identify a pavement’s condition and determine whether or not routing is appropriate when designing your crack treatment. Crack density is calculated by assessing the linear footage of cracks that are present per square feet of the pavement area. The percentage of crack density helps indicate potential movement of the cracks that are present; which in turn impacts the sealant selection in order to accommodate the expected movement. Typically, the higher the crack density, the more cracks that are present in the pavement and therefore less movement is anticipated. The lower the crack density, the less cracks that are present in the pavement and therefore higher movement is anticipated.
Keep in mind there are two fundamental reasons you rout the pavement prior to crack sealing. The first reason to rout is to prepare and clean the edges of the pavement so that you have better adhesion and therefore a better seal that will last longer. When you rout you need to remove 1/8-in. from each side of the crack to remove deteriorated asphalt and enable good bonding of the sealant to the asphalt that is still in good working condition. The second reason you rout is to create a defined reservoir that holds an amount of sealant to accommodate the anticipated annual thermal movement. The defined reservoir has specific dimensions on width and depth in the pavement depending on climate and other factors.
When pavements have a lower crack density (less than 20%), the pavement condition is typically appropriate to rout the cracks and then seal to accommodate the anticipated movement. In this case you are routing to prepare the edges for sealing, and also you may be developing a defined reservoir.
When pavements have a higher crack density (greater than 20%), the pavement condition is typically not able to sustain a defined reservoir. In this case, if the pavement can accept the routing without additional spalling you would rout to prepare the edges for sealing and long life. *Note that routing is always recommended when possible in order to provide the best performance of the sealant. Crack density should be used as a general guideline to help guide appropriate routing. The unique circumstances of each project may determine that routing is or is not appropriate outside of these guidelines.
For pavements with fatigue cracking and other severe distresses, it is never recommend to rout through such distresses. For pavements with high crack density where future surface treatments are planned, crack sealing is recommend for larger cracks in order to maintain the integrity of the pavement condition and reduce further deterioration until the surface treatment may be conducted.
In summary, routing is recommended prior to crack sealing in order to provide the best performance and is used to (1) clean and prepare the crack to bond to the sealant and (2) to create a defined reservoir to accept thermal movement. You should immediately discontinue routing if you see excessive spalling because the pavement it too deteriorated to gain benefit.
Routing Recommendations
Crack treatments are recommended as soon as the pavement begins cracking and it may be necessary to reseal older, previously sealed and additional cracks. The entire purpose of routing is to remove deteriorated asphalt, remove debris that is wedged within the crack and provide a clean, intact asphalt face for the sealant to adhere to. This also allows for the sealant level to remain below the surface of the pavement in recessed and flush fill applications, thus protecting it from traffic and snow plow contact.
It’s recommended that all cracks between ⅛-in. wide to 1-¼-in. wide should be routed and sealed when the pavement condition is appropriate (crack density ≤ 20%). When you rout, it’s recommended that ⅛-in. of material be removed from each side of the crack to remove deteriorated asphalt and enable good bonding of the sealant to the asphalt that is still in good working condition.
Most crack sealing operations can be conducted year-round; however, they often take place during the spring and fall months when temperatures are cool or moderately cool. At these temperatures, cracks are in a ‘neutral’ position, not completely open and not completely closed, allowing for sealant to be placed into the crack and accommodate movement during the summer and winter months. When routing, keep the router centered over the crack. If you don’t center the crack, or miss the crack, you may experience premature failure on the side walls of the channel.
Parking lot pavement moves less than highway pavement and typically requires cutting 1-¾-in. to 1-in wide by ¾-in. deep. As a rule of thumb, a routed crack should never be more than 1-in. deep. When routing is completed, the widened cracks should have a square cut with no rough edges.
Because asphalt pavements endure more movement, they require different routing depths depending on crack spacing. Generally, cracks should be cut to a depth half the length of the width.
Stop the routing process if excessive spalling occurs from routing, for example, if the spalling is twice as large as the cut you are making or if the spalling is greater than 1-½-in. If that occurs, the cutters need to be replaced or the pavement condition is not strong enough to continue routing. The router should follow cracks without difficulty and spalling and cracking should be minimal.