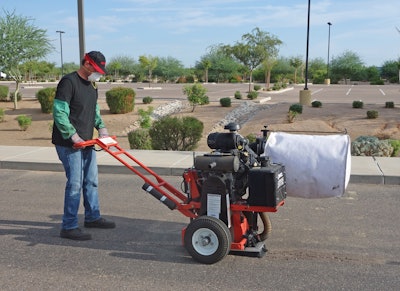
Contractors that do not offer crack routing services prior to cracks ealing have indicated that lack of time and not wanting to add another piece of equipment to their fleet are the main reasons they do not offer this service.
However, routers today are lightweight and can actually help you easily add another service to your business arsenal. And since it’s an additional service that creates longer-lasting crack repairs, contractors who offer crack routing can generate more revenue by charging more money from each crack sealing job.
Because more than 80% of costs associated with crack sealing are labor related, choosing machines that are easy to use and complete crack routing fast and efficiently makes equipment selection all the more important.
The types of machines that are available to cut asphalt cement pavement include rotary-impact routers and saws. An important factor that is involved in selecting the best equipment to create the reservoir include: productivity, meaning how many linear feet can be routed in a period of time, operating costs for the machinery, including the number of people needed to carry out the routing or sawing functions, maneuverability in order to follow the meandering crack and choosing the mechanism that has a limited potential to create damage to the pavement.
The rotary-impact router is said to be the most recommended and commonly used machine to rout reservoirs because it has the highest production-rate, the lowest cost of operation, good maneuverability and has less potential to damage the pavement especially when using carbide-tipped router bits.
Router Features to Consider
Selecting the right router can increase productivity, generate additional revenue and save your customers money by extending pavement life. In order to select the best router for the job, be sure to set aside time to figure out how the router will be used. This chart can help to determine what router will best suite you and your customer’s needs.
Sit down with your team and customers to decide what the router will be used for to help determine which router will work best for your company.
While a self-propelled router will add to the productivity of your crew, there are other router features that can help improve crack routing efficiency and operator performance.
A lightweight mobile router design can provide a smoother, safer operation. Crack-following is also important to the success of crack-routing so be sure the router you choose has a good center of balance, cutter head alignment and crack tracking guide.
These routers cut using multiple star shaped free spinning cutter bits positioned around the perimeter of a high speed rotating flywheel. These routers have a high productivity rate and can follow meandering cracks well. Reservoir cutting rates have been documented to average 720lf (linear feet) of crack per hour, and at this rate have proven not to slow the crack sealing process. In real practice and experienced operator can route 1,000 to 2,000lf and have reinforced that routing does not slow the crack sealing process.
Knowing the cutter depth is essential to crack routing. Therefore, a router with an easy-to-read depth indicator plate that shows the depth of the routed cut can be very beneficial to the operator.
An electric-operated clutch feature stops and starts the cutter-head on demand, which also supports worker safety. And an ergonomic handle that’s adjustable to the height of the operator ensures better control and handling, meaning less physical stress on the worker.
Finally, the configuration of the cutter teeth can also lead to improved productivity and performance of the router. Carbide-tipped cutters up to 2-in. wide, combined with high levels of RPMs can provide maximum crack routing performance with no bucking.
Importance of Dust Control
Reducing dust is not only important to maintain the safety of workers and the general public, it also may be required in some areas of the country.
Dust is Particulate Matter (PM), solid particles composed mostly of soil minerals (oxides of silicone, aluminum, calcium, iron) but can also contain sea salt, pollen, spores, tire particles, etc. Fugitive Dust is that particulate matter that is suspended in the air by wind, action and human activities, and may be referred to as PM10.
PM10 is very fine dust that makes up 50% of the fugitive dust particles in the air and can cause health issues. It is important for people on worksites to wear appropriate safety gear. When inhaled, PM10 particles can travel to the deep parts of the lungs and may remain there, causing respiratory illness, lung damage, and even premature death in sensitive individuals.
With the OSHA, EPA and local agencies becoming more stringent about dust, having dust control on your router is essential.
OSHA has new rules regarding respirable particulates and silica exposure beginning in 2017. The Dust Control Router has demonstrated that all airborne contaminant exposures measured were substantially below applicable Occupational Exposure Limits (OELs); the 8-hour Time Weighted Average (TWA) for respirable silica was substantially below the OSHA Action Level (AL) and the American Conference of Governmental Industrial Hygienists (ACGIH) Threshold Limit Values (TLV) - Time Weighted Average (TWA).
Pavement routers with dust control provide a cleaner working environment that can reduce dust by 96% vs. a standard model by emitting only 1.25% average dust opacity. This improves worker safety due to less dust, flying debris and clear line-of-sight. The dust suppression on the machine also contains the debris path for easier clean-up, saving time and money while extending the life of the air filter and engine.
Other Tools to Consider
Cracks must be free of all dirt, dust and debris before they can be sealed. Cleaning the crack so it is free of dirt, dust and debris starts with routing.
Surface preparation can be accomplished with compressed air being forced into a crack. This technique works well when the dirt is dry and not packed hard.
If the cracks are filled with wet dirt, the dirt needs to be removed and the crack must be completely dried. An air compressor or a hot air lance generates temperatures in excess of 2,000°F and can dry the clay and dirt, burn the vegetation and simultaneously blow out the crack.
Once a rout of the crack is complete, contractors should use compressed air (hot or cold) to remove the dust created by the router. Engine-powered steel wire brushes also can be used to clean cracks.